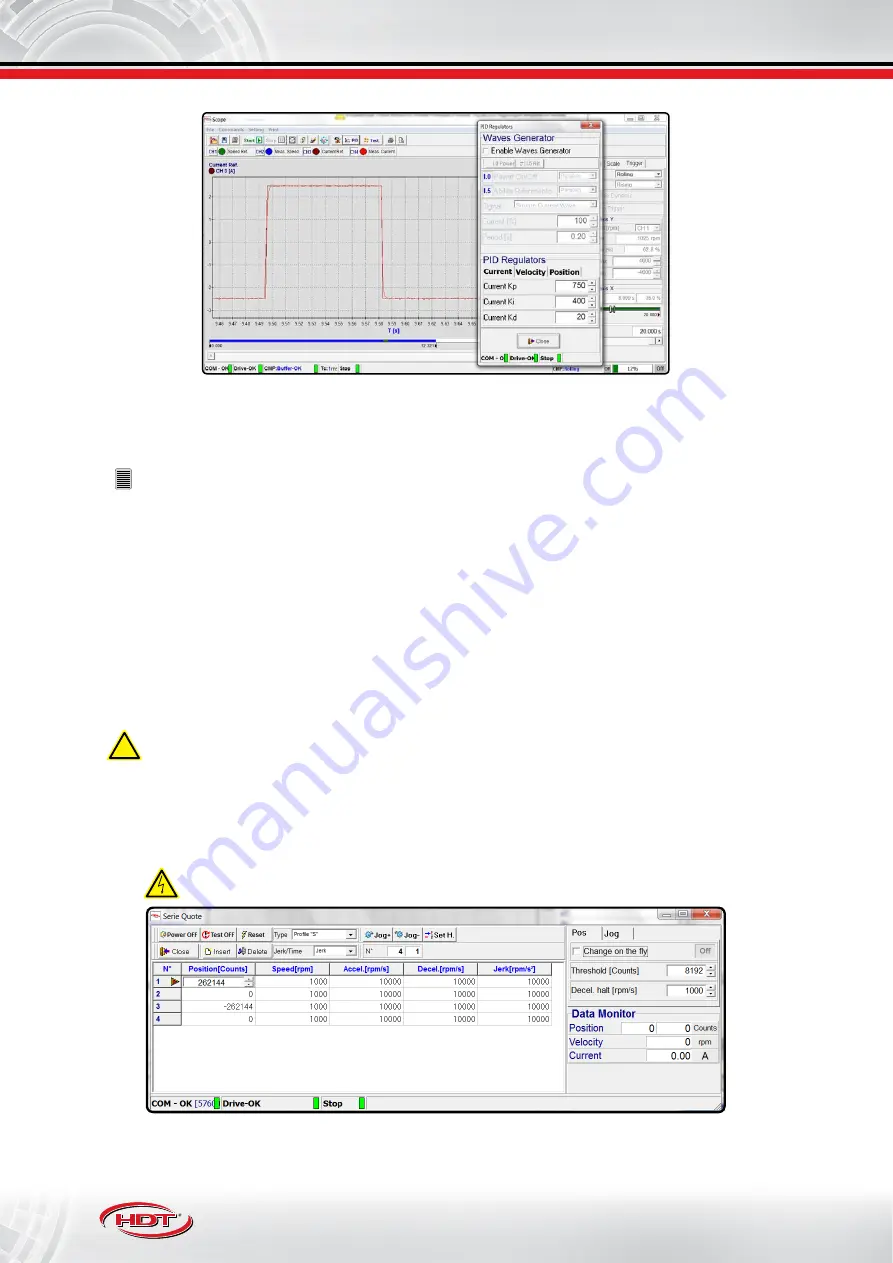
108
Installation and user guide
Rev: 4.0
NTT 240/460
Operation mode
An optimal current loop tuning is shown in picture below:
At the end of PID current tuning
, if a third parts motor is used, please perform a ‘Motor Autophasing’ (see
!
NOTES:
•
K
P
and K
I
optimum values could vary greatly depending on application.
•
In high inertia systems, resonance may not occur at any K
P
values lower than maximum set value (2000).
In these cases, set K
P
equal to 1000 and increase K
I
until misured current variable accurately follows the
desired current reference: repeat entire operation erasing K
I
and increasing K
P
at step of 200.
•
In any case, it’s recommended to set K
P
≤ 1800.
6.16.2 Speed loop tuning
Speed loop tuning must be performed with load connected because time constants depend on dinamic system
to control.
Speed loop tuning must be performed after current loop tuning and execution step are similar.
!
It’s recommended to perform motor autophasing
before speed loop tuning
(see
To perform tuning
, please do the following:
1.
generate appropriate cyclic target position
: use ‘TEST’ function into Caliper software to create desired
reference (see
). Set target position with appropriate acceleration and
deceleration parameters according to system dinamic, as shown in the image below:
In these conditions, drive follows a speed and cyclic position reference with ramp parameters: please,
pay attention to load during operation.
Summary of Contents for NTT 240
Page 129: ......