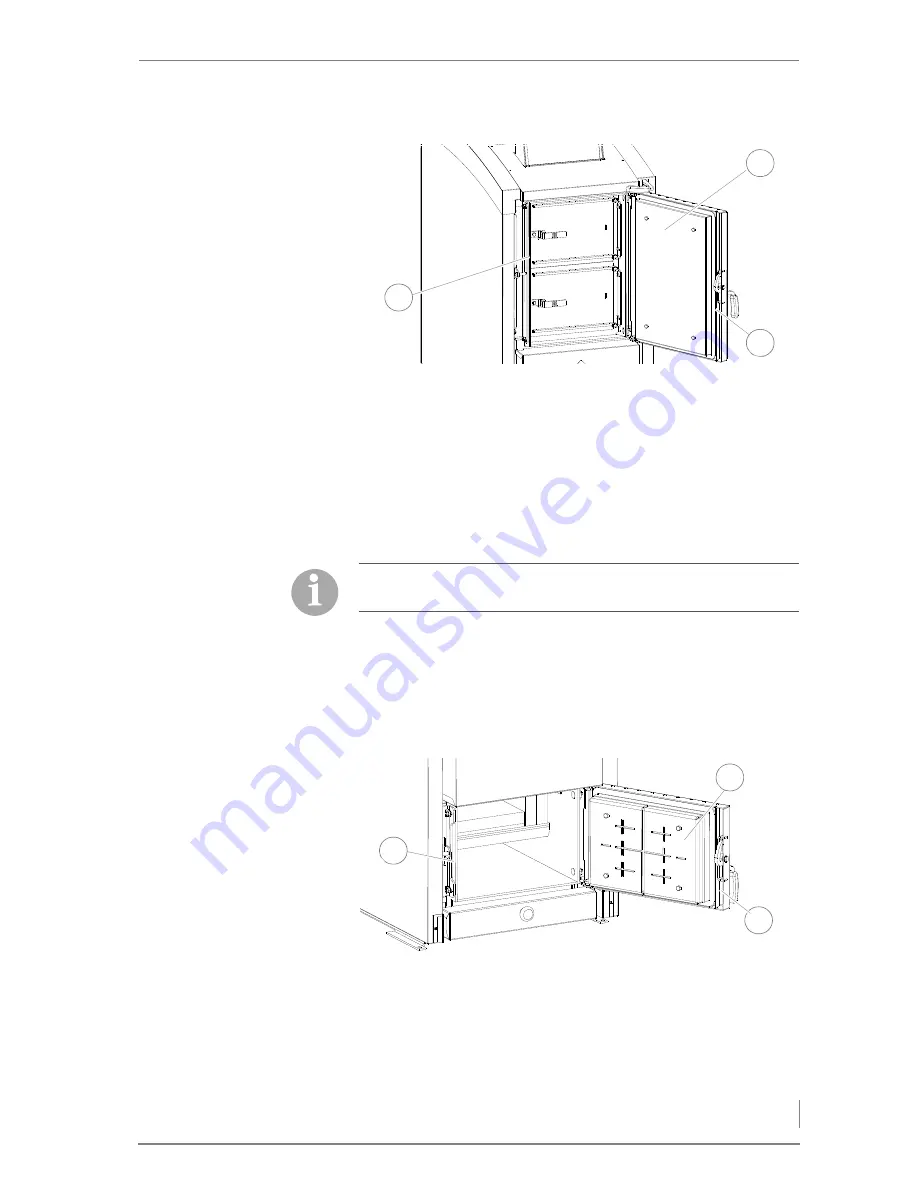
7 Cleaning and servicing the heating system – Procedure
67
3.
Clamp a sheet of paper (approx. 30 cm long and 2 cm wide)
between the contact surface (3) and the seal (2) of the fuel
chamber door.
4.
Close the fuel chamber door (1).
5.
Pull on the paper.
✓
If the paper moves, the door is not properly sealed.
✓
If the paper does not move, the door is properly sealed.
6.
Repeat the procedure from step 2 to step 5 until you have
inspected all four of the contact surfaces (3).
7.
Remove the paper and close the fuel chamber door (1).
✓
The inspection of the fuel chamber door is complete.
I
NSPECTING
THE
COMBUSTION
CHAMBER
DOOR
8.
Open the combustion chamber door (1).
9.
Clamp a sheet of paper (approx. 30 cm long and 2 cm wide)
between the contact surface (3) and the seal (2) of the combustion
chamber door.
10.
Close the combustion chamber door (1).
Figure 7/16 - Checking the fuel chamber door for leaks
3
1
2
If a correction to the fuel chamber door is necessary, consult a
qualified specialist.
Figure 7/17 - Checking the combustion chamber door for leaks
2
3
1
Summary of Contents for Navora 20
Page 1: ...hdg bavaria com HDG Navora 20 25 30 HDG Navora 40 45 50 Operation Manual ...
Page 2: ......
Page 77: ...77 NOTICE ...
Page 78: ...78 HDG Navora 40 45 50 Version 1 de HDG Bavaria GmbH 06 2008 NOTICE ...
Page 79: ......