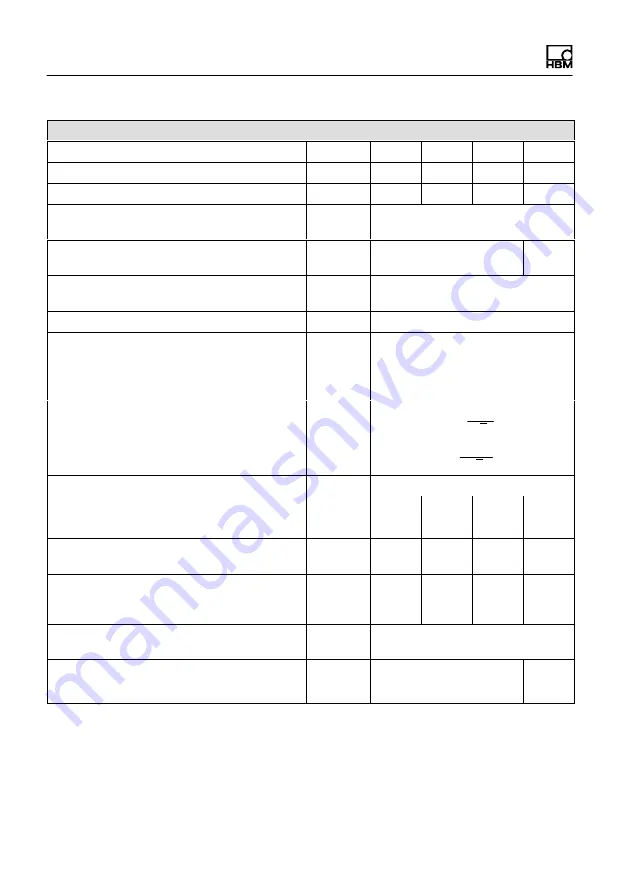
Specifications
76
A0608-14.0
HBM: public
T10F
Mechanical values 50 N
V
m ... 500 N
V
m
Nominal (rated) torque M
nom
N
V
m
50
100
200
500
Torsional stiffness c
T
kN
⋅
m/ rad
160
160
430
1000
Torsion angle M
nom
Degree
0.018
0.036
0.027
0.028
Maximum deflection at longitudinal force
limit
mm
< 0.03
Additional max. radial run‐out deviation at
lateral limit force
mm
< 0.01
< 0.02
Additional plane/parallel deviation at
bending moment limit
mm
< 0.2
Balance quality level per DIN ISO 1940
G 6.3
Max. limits for relative rotor vibration
displacement (peaktopeak)
Undulations in area of connection flange, based
on ISO 7919-3
Normal operation (continuous operation)
μ
m
s
(p
*
p)
+
9000
n
Ǹ
(nin min
*
1
)
Start and stop operation/resonance ranges
(temporary)
μ
m
s
(p
*
p)
+
13200
n
Ǹ
(nin min
*
1
)
Mass moment of inertia of the rotor
I
V
(around axis of rotation) x 10
-3
kg
⋅
m
2
1.3
1.3
3.4
13.2
I
V
with speed system x 10
-3
kg
⋅
m
2
1.7
1.7
3.5
13.2
Proportional mass moment of inertia
(measuring body side)
%
51
51
44
39
Proportional mass moment of inertia
with speed measuring system (measuring
body side)
%
40
40
43
39
Max. permissible static eccentricity of the
rotor (radially)
mm
"
2
Perm. axial displacement
between rotor and stator
mm
"
2
"
3
6)
The influence of radial run‐out deviations, eccentricity, defects of form, notches, marks, local
residual magnetism, structural variations or material anomalies needs to be taken into account
and isolated from the actual wave oscillation.
7)
Refer to limited values for speed measuring system