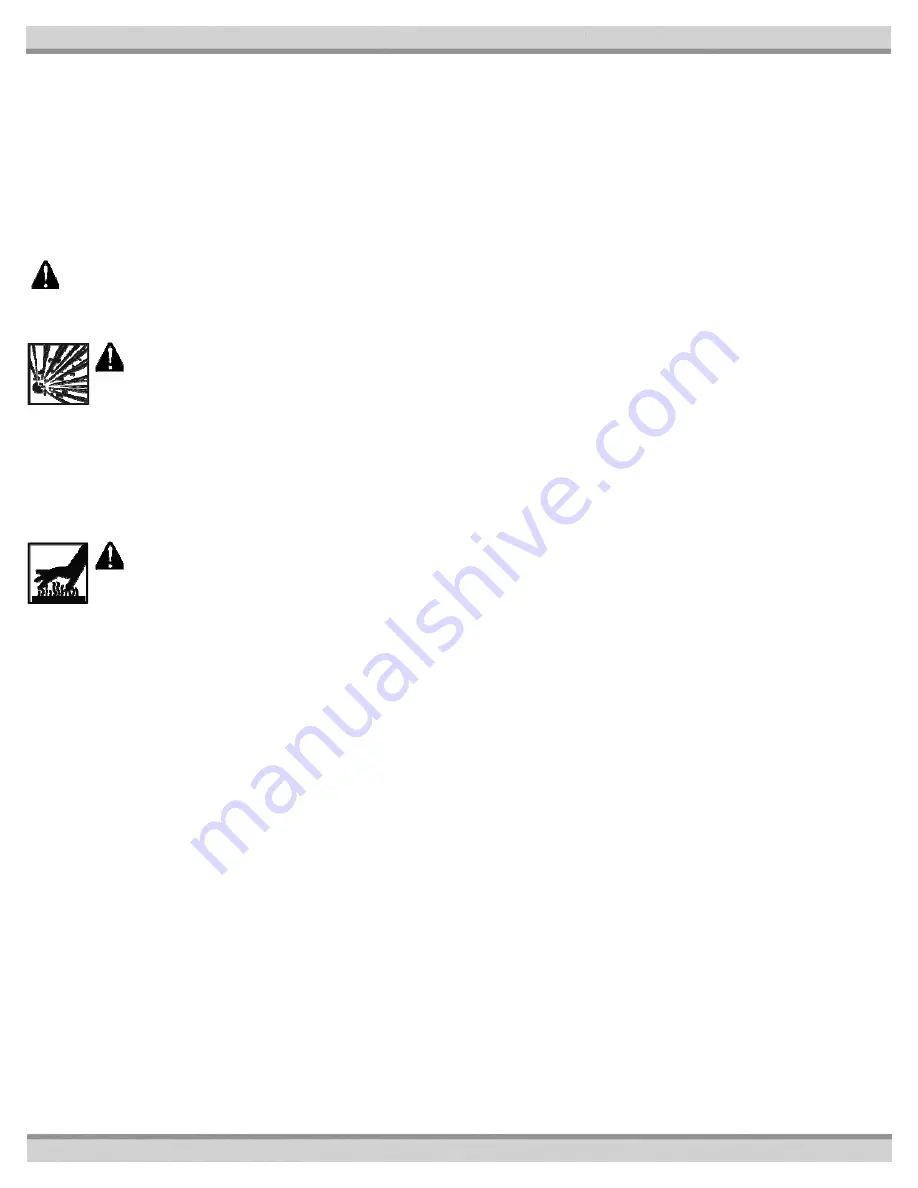
38
ONLY USE GENUINE HAYWARD REPLACEMENT PARTS
51300803801 REV B
SPRING START-UP:
This procedure should be performed annually to ready your heater for the upcoming season. In addition to the steps
outlined below, it is recommended that a
PERIODIC INSPECTION
also be performed.
1. Inspect and clean the heater, being sure the heater is free of leaves and debris prior to startup.
2. Be sure inlet and outlet piping are properly attached to the heater and the drain valve is closed.
3. Turn the filtration system pump “ON” and allow the system to run long enough to purge all the air from the lines.
4. Turn the gas supply to the heater “ON”.
5. Set the temperature control using the keypad to “POOL” or “SPA” and adjust the set point to the desired temperature setting.
6. If operating difficulties are encountered, contact a qualified service company for assistance.
COMPONENT SERVICE
WARNING:
Only qualified service technicians, with appropriate test equipment, should be allowed to service the heater. All of the com-
ponents that comprise the system have an effect on heater operation. Before proceeding with heater related troubleshooting tips, be cer-
tain that the pump is operating correctly, the filters and strainers are not blocked, the valves in the piping are properly positioned, and the
time clocks are properly set.
WARNING:
EXPLOSION HAZARD
Do not attempt to repair broken or faulty components of this heater. Do not modify the
heater or its components in any manner. To do so may result in a malfunction that could result in death, personal injury, or
property damage. Check with the pool owner to see if any part of the heater has been under water. Replace any electrically
operated component that has been under water
.
SERVICE OF HEATER:
The following service procedures:
HEAT EXCHANGER INSPECTION AND CLEANING
and
BURNER INSPECTION
AND CLEANING
are recommended to be performed as part of annual heater maintenance to ensure proper heater operation and long life.
HEAT EXCHANGER INSPECTION AND CLEANING:
Loosen the flare nut holding the gas manifold assembly to the combustion blower. Re-
move the blower and burner sub-assembly (see Figure 1: Sub-Assemblies) and inspect the exposed surfaces of the heat exchanger for debris
or soot accumulation. If heat exchanger needs cleaning perform the following procedure:
WARNING:
BURN HAZARD
:
Let heater cool before performing any disassembly or servicing of the heater. Wear proper
PPE when servicing heater.
1. Turn pump, main gas valve and heater power “OFF”.
2. Remove debris by hand, soft-tipped brush or shop VAC.
3. Check combustion chamber refractory is still in good shape with no pieces missing or damaged, no holes, and no large cracks extending
through the entire thickness of the pieces. This evaluation can be performed with heat exchanger in place with additional lighting. If com-
bustion chamber refractory is damaged, the entire chamber must be replaced.
4. Re-assemble the heater by reversing the disassembly steps. Turn pump, main gas valve and heater power “ON”. Test fire heater.
NOTICE:
Although the heat exchanger should be cleaned of soot, the fact that soot occurred should be investigated. It may indicate oth-
er problems such as: Insufficient air supply; Inadequate venting; High or low gas pressure; Blockage of burner or orifices; Blockage of
blower inlet; Low voltage supply causing blower to “spin” slower; Improper heater location / installation; Incorrect gas supply pipe size;
Excessive water flow through heat exchanger; or an LP tank below 30% full level.