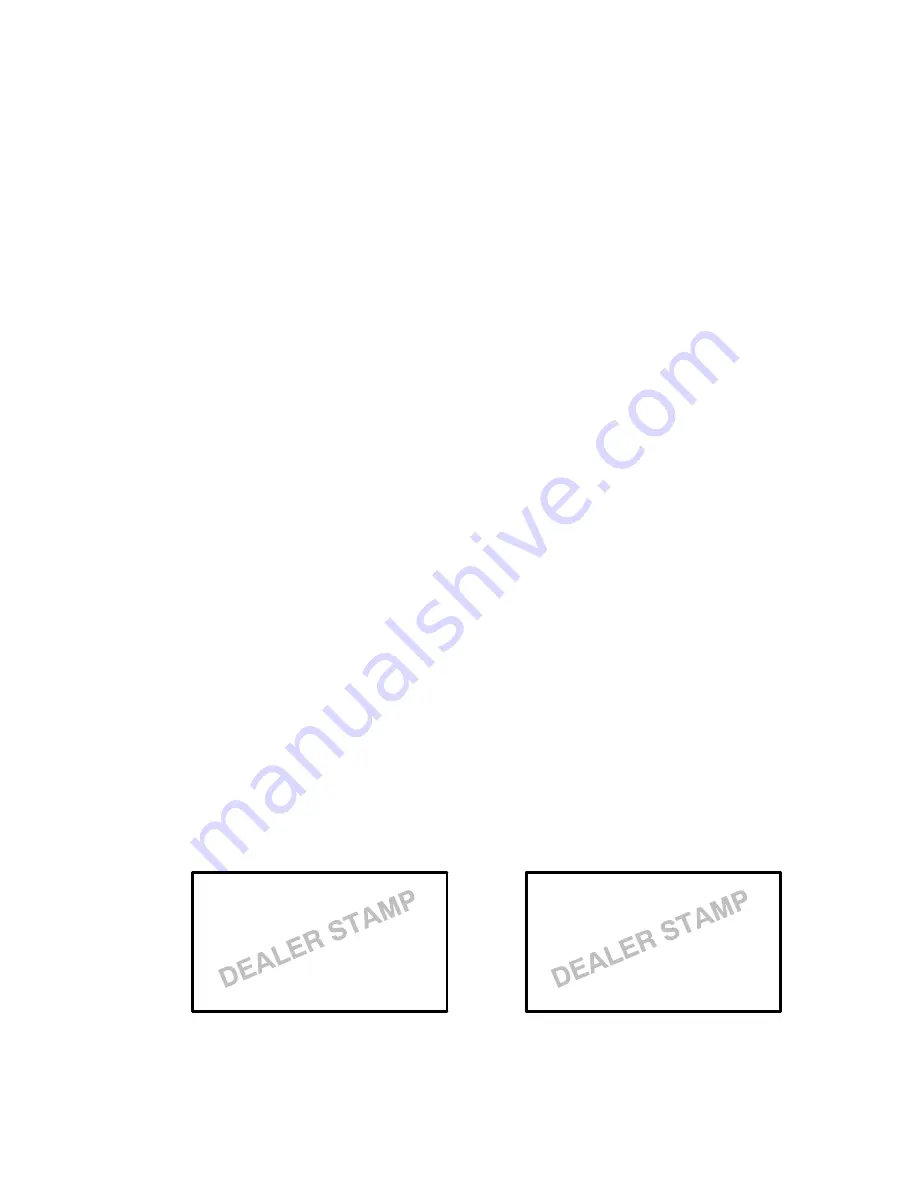
3
276798MA DRAFT COPY
Hayter Limited
warrants to the original user / purchaser that this unit shall be free from defects in
material and workmanship under normal use and service for a period of
three years
from the
date of purchase. The manufacturers of the engine and battery pack system (where applicable)
furnish their own warranty and services are provided through their authorised network (Refer to
“Engine/Battery Pack Warranty Statement”). To qualify for the full benefit of the warranty, the war-
ranty registration card must be returned within 60 days of purchase. Subject to the conditions and
exclusions noted in this limited warranty, we shall at our option, repair or replace any warranted
part during the applicable period. If you are in doubt or experience any difficulty, please consult a
Hayter
Authorised Service Dealer for clarification..
To qualify for the extended warranty (second and third year) of the three year limited warranty, the
machine must have annual services carried out by an Authorised Hayter Service Dealer. These
chargeable services should be carried out within 12 and 24 months of the date of purchase.
Excluded from the extended warranty period are those items which are subject to normal wear
and tear e.g. tyres, wheels, cutterbars, cables, batteries and other consumable wearing parts.
All consumer machines which are fitted with a
genuine
Hayter friction disc as original equipment,
before use, are covered by a
Lifetime Warranty
against the engine crankshaft bending.
Note:
friction washers, blade brake units and other such devices are not applicable. Only machines
fitted with a
genuine
Hayter friction disc, which are used in accordance with the recommended
operating and maintenance procedures, are covered.
This warranty does not apply to any unit that has been tampered with, altered, misused, abused
or used for hire, and will become invalid if non genuine Hayter parts are fitted. This warranty does
not cover minor mechanical adjustments unless they are due to defective materials or workman-
ship. Consult the Owner’s Handbook or a Hayter Authorised Service Dealer for assistance when
making these adjustments.
A warranty period of 90 days applies to machines used for commercial purposes.
To make a warranty claim, return the unit to a
Hayter
authorised dealer along with proof of pur-
chase stating the machine serial number and date of purchase. The service receipt(s) or this
Owner’s Handbook with the 1st/2nd year service boxes fully completed, must be produced as
proof of entitlement to the extended warranty period. Subject to the conditions and exclusions in
this limited warranty, the authorised dealer will, at our option, repair or replace any warranted part
within the duration of the warranty period.
This limited warranty gives you specific legal rights and is in addition to any statutory rights to
which you may be entitled and your statutory rights are not affected by this warranty. If you need
additional information concerning this written warranty, or assistance in obtaining services,
please write to:
HAYTER LIMITED,
Service Department,
Spellbrook,
Bishop’s Stortford,
Hertfordshire. CM23 4BU
LIMITED WARRANTY
1st Year
Service
Record
2nd Year
Service
Record
Date . . . . . . . . . .. . . . . . . . . . . . . . . . . . . . . . . .
Signed . . . . . . . . . . . . . . . . . . . . . . . . . . . . . . . .
Date . . . . . . . . . .. . . . . . . . . . . . . . . . . . . . . . . .
Signed . . . . . . . . . . . . . . . . . . . . . . . . . . . . . . . .
Summary of Contents for Powertrim 407D
Page 26: ...NOTES 26 276798MA DRAFT COPY...
Page 27: ...NOTES 27 276798MA DRAFT COPY...