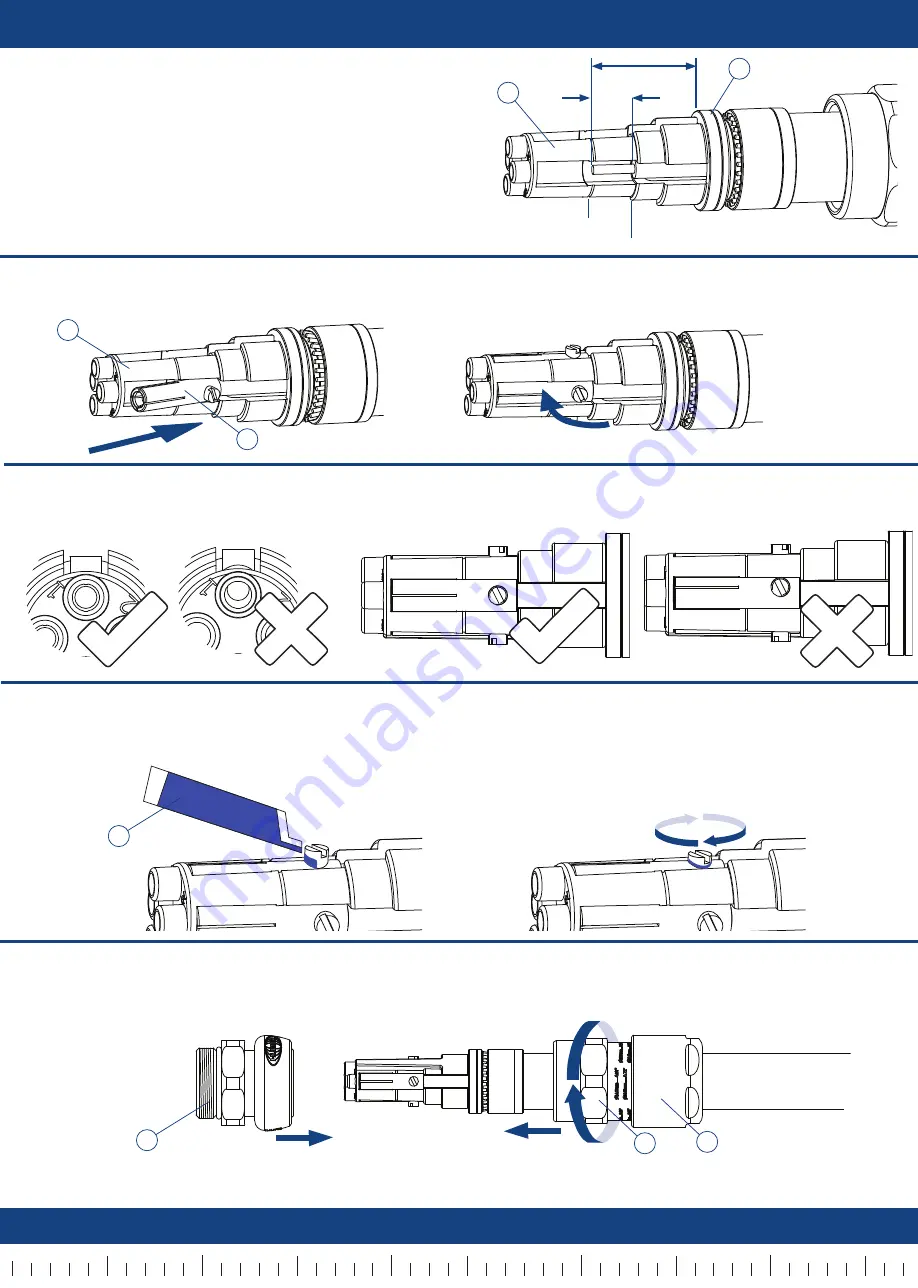
AI 2045 - Issue B / Page 5 of 9
Images for illustration purposes only.
Product supplied may differ from that shown.
STEP B7: Cut conductors to length and strip
Cut conductor to 26mm from top of spigot. Use the groove indicator in the
insert as a visual aid. The conductor should not extend past this cut line.
Strip conductor back past the insert shoulder which indicates the strip line
(approx 10mm).
The socket insert (7) may be removed from the spigot (9) to assist cable
stripping process then re installed as shown in step B2.
TIP:
Use a pen to mark cores in situ then remove insert to aid conductor
strip process.
26mm
Cut line
Strip line
STEP B8: Fit contacts to cable conductors
Take the first contact (8), slide over the conductor and press into slot in the insert (7). The contact (8) will now be retained in the insert (7).
Repeat for all remaining contacts
STEP B9: Check alignment of contacts
Firstly confirm all contacts (8) are concentric to the openings in the tip of the insert.
Then ensure the contacts (8) are correctly rotated so that the grub screw is in the centre of the slot.
STEP B10: Apply threadlock and tighten grubscrews
Take the threadlock sachet (14) supplied with the product and tear open. Dispense a drop of threadlock onto the exposed thread of one
contact grub screw. Tighten the grubscrew with a small screwdriver. Recommended torque is 0.75Nm. Wipe away any excess. Repeat for all
contacts.
STEP B11: Install middlenut (11) to centrenut (6)
Screw the centrenut (6) loosely onto the middlenut (11). Do not yet tighten.
IMPORTANT:
Ensure that the metalwork can still spin around the cable and insert assembly.
TIP:
If the backnut (12) does not spin around cable, it may need to be unscrewed from the middlenut (11).
7
9
7
8
14
6
11
The cable has now been successfully terminated with the 501/RCG Body.
The 501/RCG Body may now either be connected to a 501/RCG Entry (see Part C) or blanked off with an energised
end cap (see Part E).
10mm
12
10
20
30
40
5
15
25
35
45
10
20
30
40