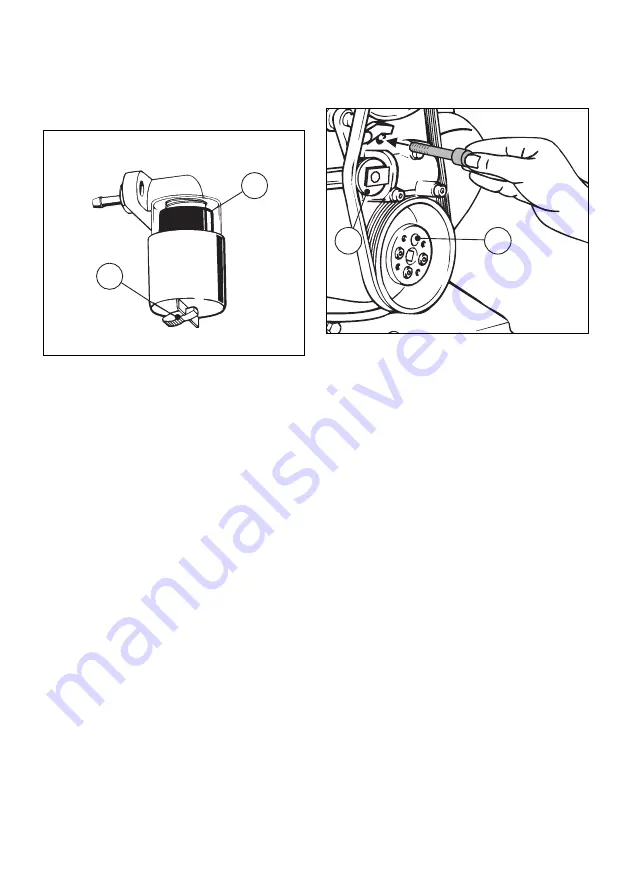
Mechanical maintenance indicator
– Pull hose „2“ off air intake pipe and build up a
strong vacuum at the open end (Figure 61).
63
– Red zone „1“ will appear and engage in
position.
– After the functional check, release red zone „1“
by pressing reset knob „2“.
Renew any defective components without delay.
1
L3/78
2
6.2.
Renewing fan drive belt, checking
operation of belt monitor
64
– Remove one machine screw at belt pulley „1“.
– Press back tensioning pulley „2“ and lock it
with the machine screw provided.
– Unscrew and remove the belt pulley.
– Take off the Poly-V belt.
Note:
If any grooves on the belt pulley have broken off
or are bent, always renew the pulley.
Checking operation of belt monitor
Always check operation of the shutdown device
when the belt is renewed.
2
1
L3/249
38