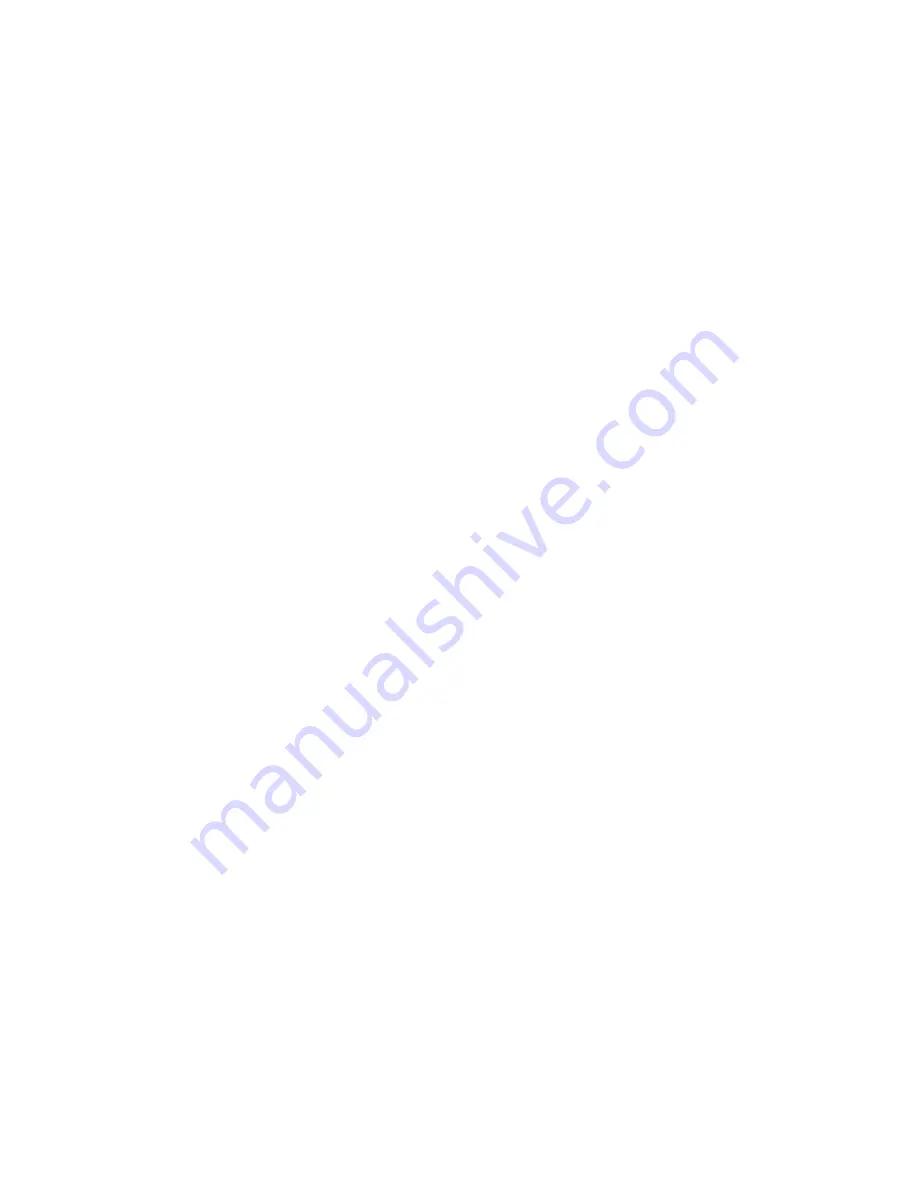
D. ELECTRONIC IGNITION:
All (I) (IS) HRDV series furnaces are equipped with a solid state design, intermittent pilot ignition system. This electronic
system consists of an ignition control module, combination pilot burner/igniter-sensor (sensor or flame rod) assembly, and
igniter-sensor lead. Activated by the units 24V transformer and controlled by a field installed thermostat or controller,
module will first perform a safe-start check which tests its internal components for a false pilot flame condition. If
satisfactory, the module then energizes the pilot gas valve to open and generates 15,000 V peak capacitive discharge
ignition spark to ignite pilot burner. When pilot is established, the flame monitoring circuit of module responds to the
presence of flame detected by the flame rod and discontinues ignition spark. The main gas valve is then energized to
open, pilot lights main burners, and burner operation continues until call for heat is satisfied. Module then deactivates both
pilot and main gas valves and unit shuts down.
Two types of ignition control modules are utilized. A non 100% shutoff design is used with natural gas ONLY. It provides
continuous spark for pilot ignition, but if pilot does not light, trouble must be isolated and corrected. A 100% shutoff design
may be used for natural and L.P. gas. It provides a 90 second gas trial for pilot ignition. If pilot does not light within the trial
time, module deactivates pilot valve (100% safety lockout) but continues spark for pilot ignition. This system may be reset
at the thermostat or controller and trial for ignition resumed. If pilot still fails to ignite, trouble must be isolated and
corrected.
E. OPERATION:
*WARNING: USE CAUTION ON FOLLOWING PROCEDURES.
*1. Purge all air from gas piping.
*2. Carefully follow lighting instructions shown on the SPECIFICATION PLATE for electric ignition and main burner
operation.
*3. Adjust pilot burner to a quiet blue flame. Flame must surround the end of the flame rod for proper operation of
the flame sensing circuit. No combustion air adjustment is required on main burners.
*4. Pressure regulator setting must NOT be changed except under qualified supervision. If necessary, contact gas
company before adjusting.
*5. With the unit firing a maximum input, the gas line pressure should be maintained at designated inches of W.C.
marked under MINIMUM SUPPLY PRESSURE on the specification plate. On multiple unit installations, each
furnace should be checked in sequence. Then, with all units firing at maximum rate, the line pressure should
be at least the minimum marked on the specification plate.
*6.
After the line pressure has been established, MANIFOLD PRESSURE should be as marked on the specification
plate. If the unit is equipped with modulating gas controls, they must be in the HIGH FIRE POSITION when
manifold pressure is read. Furnace may be severely overfired if regulator is adjusted without this precaution,
and factory warranty is VOID if heaters are operated in excess of rated BTU inputs.
7. If a fan control is used, check to be sure blower starts within two minutes after gas ignition.
8. Check entering and discharge air temperature to make certain that heat rise does NOT exceed limits specified
(see item 8 of INSTALLATION PRECAUTIONS) through ANY PORTION of the heat exchanger. Locate thermom-
eters in representative temperature zones of the duct system both upstream and downstream of the furnace
and to find the difference of the respective readings. The heat rise temperature may be changed by increasing
blower speed to lower the temperature or by decreasing the blower speed to raise the temperature.
9. Check for proper operation of the limit switch. Refer to item 13 of INSTALLATION PRECAUTIONS.
10. To maintain proper air circulation through the heating system, twice a year check blower sheaves for align-
ment and belts for tension. Inspect for residual accumulation on impeller blades and follow blower manufac-
turer’s instructions for lubrication and maintenance.
7