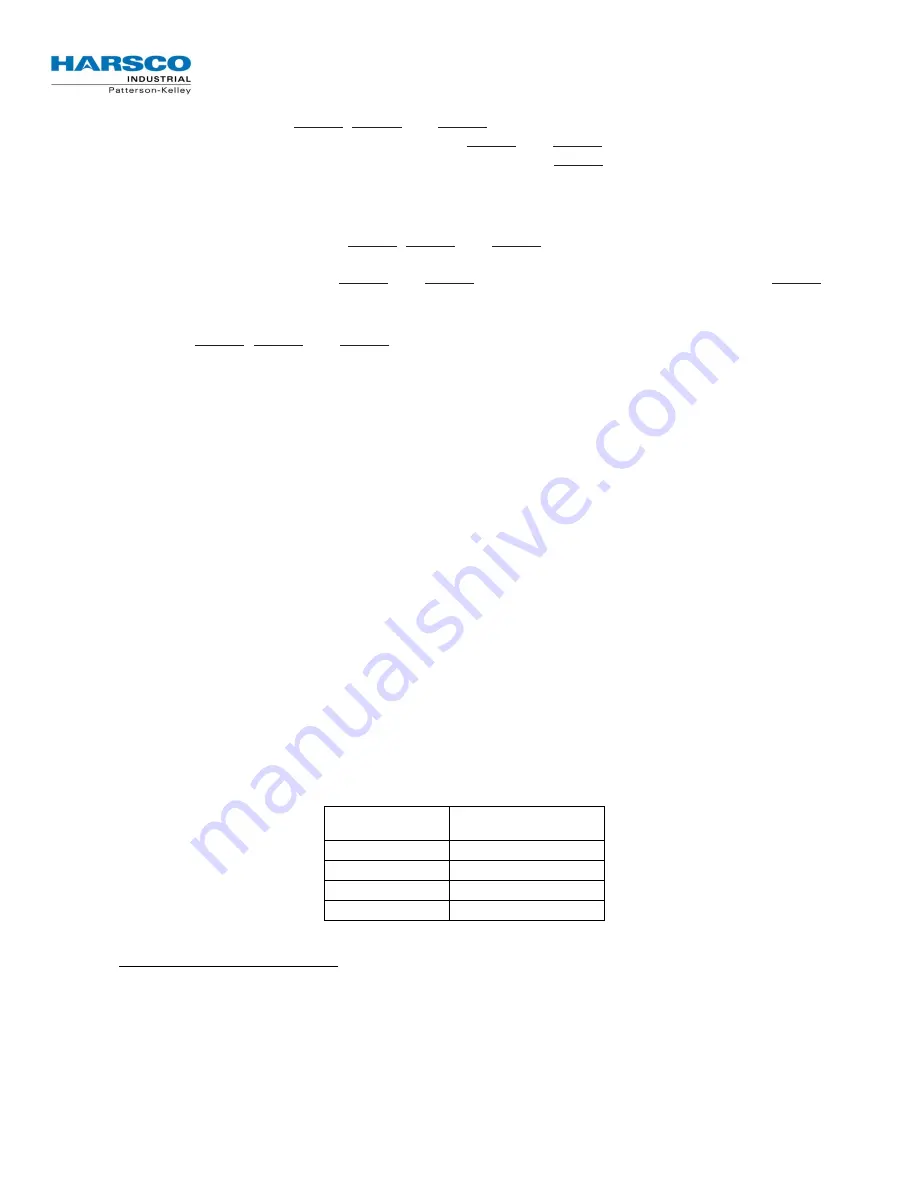
P-K SONIC
TM
Gas Fired Boiler
T
T
T
Technical Service 1.877.728.5351
echnical Service 1.877.728.5351
echnical Service 1.877.728.5351
echnical Service 1.877.728.5351
Cascade Shield & Cascade
–
TB1-18
,
TB1-19
and
TB1-20
can be used to setup a cascade system with
multiple SONIC boilers with NURO controls. Terminals
TB1-19
and
TB1-20
are reserved for the cascade
communication between the master and member boilers. Terminal
TB1-18
should be used to connect the
cascade communication wiring shield between all boilers. The cascade and shielding must be wired from the
master boiler to each individual member boiler in a daisy-chain fashion.
NOTE
: Only ground the shield at the
master boiler.
MODBUS COM & MODBUS Shield
–
TB1-22
,
TB1-23
and
TB1-24
can be used to integrate the boiler with a
Building Management System (BMS), Protocol Converter, or other device capable of RS-485 2-wire
MODBUS communication. Terminals
TB1-22
and
TB1-23
are reserved for MODBUS and terminal
TB1-18
provides a connection for the MODDBUS communication wire shield.
NOTE
: Only ground the shield at the
master boiler.
ECOM 1, 2 & 3
–
TB1-25
,
TB1-26
and
TB1-27
can be used to connect a wireless outdoor air temperature
sensor. The wireless receiver should be installed at or near the boiler, and the wireless temperature sensor
should be installed on the North face of the building and shielded from direct sunlight exposure.
3.3 Combustion Air
The air intake duct can be fabricated from PVC, CPVC, single wall galvanized steel, or other suitable
materials. The duct must be rigid enough to maintain the full required cross sectional area under all operating
conditions. Proper sealing of the intake ductwork is necessary to prevent infiltration of air from conditioned
space. Joints in PVC or CPVC must be cemented. For galvanized duct, wrap each joint and seam with
adhesive aluminum tape or other sealant. The installation of a bird screen on the intake termination is
recommended. Ensure that the screen does not become blocked with snow, ice, insects etc. Combustion air
duct should be designed with maximum 0.22” w.c. friction loss.
Combustion air must be free from dust, lint, etc. The presence of such materials in the air supplied to the
burner could cause nuisance "Low Air" shutdowns or premature burner failure. The boiler should not be
operated during construction while the possibility of drywall dust, demolition dust, etc. exists.
The combustion air supply must be completely free of chemical fumes which may be corrosive when burned
in the boiler. Common chemicals which must be avoided are fluorocarbons and other halogenated
compounds, most commonly present as refrigerants or solvents, such as Freon®, trichloroethylene,
perchloroethylene, chlorine, etc. These chemicals, when burned, form acids which quickly attack the boiler
and the boiler stack. The result is improper combustion and premature boiler failure.
Refer to the table below which summarizes the combustion air requirements for the SONIC boilers. Ensure
the combustion air piping is of sufficient size (and acceptable equivalent length) in order to carry the required
SCFM with a maximum friction loss of 0.22”
W.C.
P-K SONIC™
Boiler Model
Required SCFM
SC-1500
350
SC-2000
467
SC-3000
629
SC-4000
839
Acceptable Materials for Venting Systems
Manufactured Venting Systems
US and Canada:
AL29-4C Stainless Steel Vent Systems listed and labeled to UL1738 Venting Systems for Gas-
Burning Appliances, Categories II, III, and IV
316L Stainless Steel where certified and warranted by the vent manufacturer for venting of Category
II, III, or IV appliances