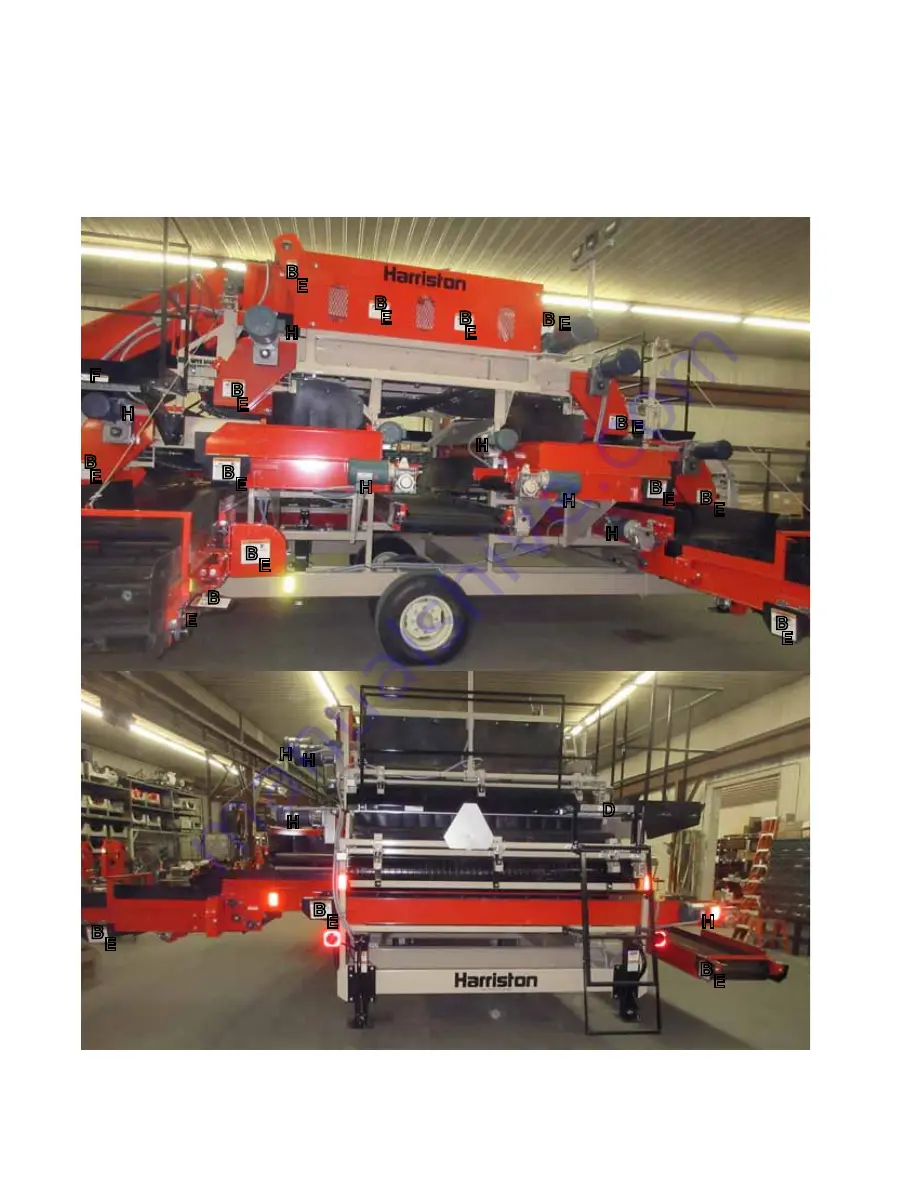
18
The types of safety signs and locations on the equipment are shown in the illustrations that follow. Good safety
requires that you familiarize yourself with the various Safety Signs, the type of warning and the area, or particu-
lar function related to that area, that requires your SAFETY AWARENESS.
• Think SAFETY! Work SAFELY!
REMEMBER - If Safety Signs have been damaged, removed, become illegible or parts replaced without safety
signs, new signs must be applied. New safety signs are available from your authorized dealer.
B E
B E
B
E
B
E
B
E
B
B
B
B
E
E
E
E
B
E
B
B
B
E
E
E
B
E
B
E
B
E
H
H
H
H
H
F
D
H
H
H
H
H
Summary of Contents for 4240 CLOD HOPPER
Page 1: ...HARRISTON INDUSTRIES 4240 CLOD HOPPER OPERATOR S MANUAL ...
Page 4: ......
Page 6: ......
Page 8: ......
Page 10: ...2 ...
Page 20: ...12 ...
Page 31: ...23 H a M F G K L E X A N J W Q D S Q W N R Z T A P E B ...
Page 32: ...24 Fig 1B MACHINE COMPONENTS V Y M O P N L a X U a F W R Q G H J a O R Y S T E ...
Page 63: ...55 4 Clean machine with a power washer Fig 43 machine ...
Page 76: ...68 ...
Page 77: ...69 SPECIFICATIONS SUBJECT TO CHANGE WITHOUT NOTICE 7 SPECIFICATIONS 7 1 MECHANICAL ...
Page 80: ...72 ...
Page 82: ......
Page 83: ......