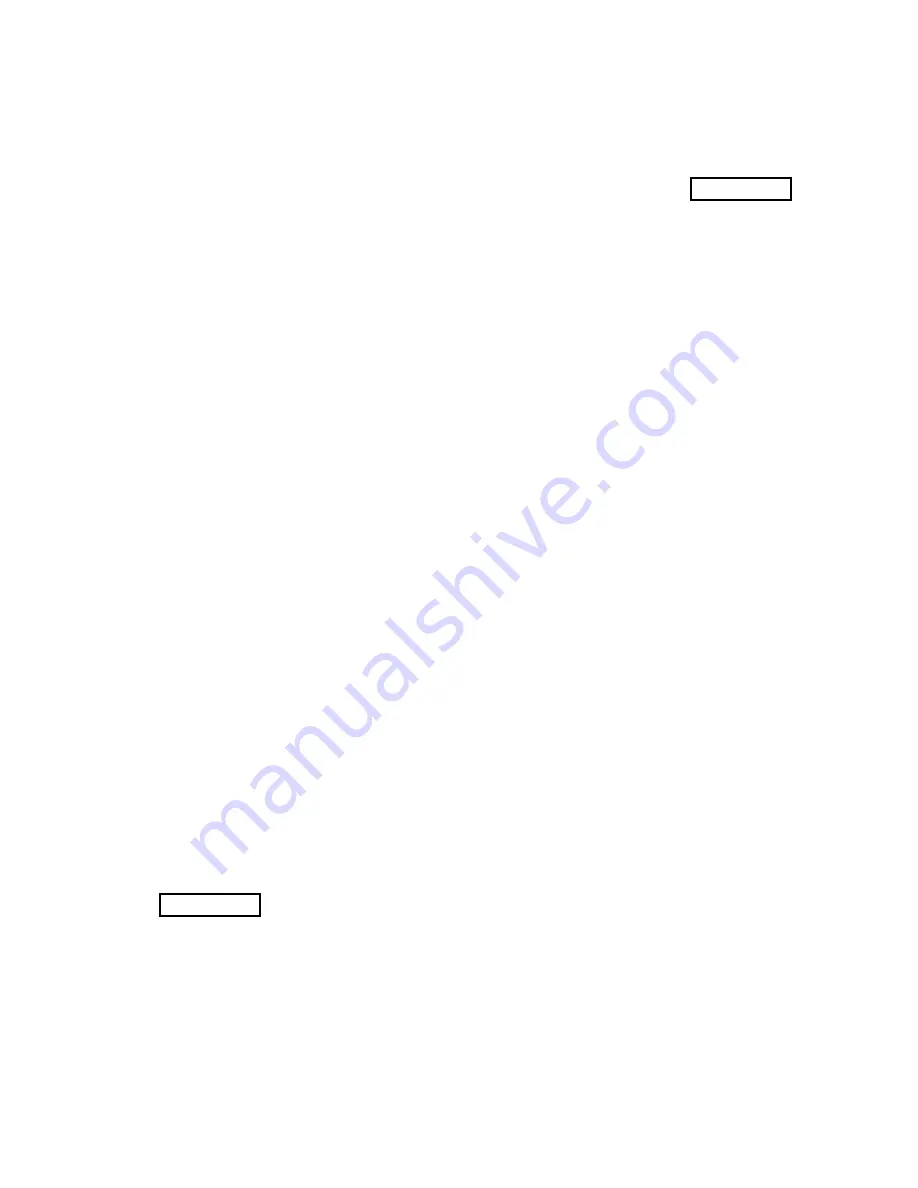
SECTION B
IPA (A5)
B.1.
Principles of Operation
The IPA Board consists of a class D bridge
amplifier using high power MOSFET tran-
sistors. This board uses 60-120 volts dc
from the IPA power supply. The IPA is
driven from the Oscillator through jack J2.
The carrier signal is applied to transformer
T11 and T12.
Capacitors C11, C12, C13, C14, C16,
C17, C18 and C19 RF bypass the IPA DC
supply.
Transistors Q11, Q12, Q13 and Q14 are
driven into class D operation. Transistors
Q11 and Q13 are driven 180 degrees out of
phase with respect to Q12 and Q14. During
the positive half of the RF cycle Q11 and
Q13 are simultaneously on; then during the
negative half of the RF cycle Q12 and Q14
are on. This produces a carrier squarewave
waveform of twice the supply voltage
across terminals E11 and E12. These termi-
nals then connect to the IPA output network.
B.1.1.
IPA Tuning Network
The IPA Output Network is a series tuned
circuit comprised of A26L1, A26L2,
A26C1, and the primary of A26T1. A26T1,
along with A26A1 (IPA Power Splitter
board) and the housing assembly forms a
step down transformer. The low impedance
presented by the drive cables is matched by
the one turn secondary on the IPA toroid and
the Splitter board. The primary consists of
several turns of enameled wire wound on a
toroid.
B.2.
Replacement/Alignment
When replacing the IPA module, be sure
an even coating of thermal compound is
applied to the mating heat sink surfaces. Be
certain to tighten down the captive fasteners
which mount the IPA module to the heat
sink.
B.3.
IPA Tuning and Testing
Procedure
WARNING
ENSURE THE HIGH VOLTAGE IS TURNED
OFF BEFORE PROCEEDING WITH THE
FOLLOWING STEPS.
RF Drive level is measured on the PA
modules with an oscilloscope. Place the
oscilloscope probe across R13 or the
equivalent terminal of any module.
Attach the probe ground lead to the RF
drive ground plane. Do not use the cabinet
or chassis ground as this will give an incor-
rect waveform. Proper drive level should be
26-32 volts peak to peak on all eight inputs
of each PA module A1, A2, A3, and A4, with
high voltage OFF.
If the RF Drive exceeds 32 volts peak to
peak, the secondary taps on A20T1 will
have to be changed to a lower number to
reduce the IPA supply voltage. For exam-
ple, moving from the 105 tap to the 90 tap
will reduce the IPA supply voltage and the
drive level.
If the drive level on the PA Module(s) is
below 20 Vp-p, the IPA module outputs
should be checked with an oscilloscope by
connecting the scope probe tip to A5 Q12
or Q13 while only the low voltage is on.
There should be an RF square wave at the
operating frequency with an amplitude
equal to the IPA supply voltage.
If square waves are not found at both Q12
and Q13, refer to the troubleshooting pro-
cedures which follow.
If there is no input, the RF Oscillator board
or the cabling is probably at fault. Refer to
the troubleshooting information in Section
A, covering the RF Oscillator.
If only one side of the IPA is producing
output, refer to the ohmmeter test proce-
dure.
B.3.0.1.
IPA Tuning
Adjust A26L2 with a slotted screwdriver
for a peak in drive level as measured on the
PA modules.
A26L1 is tapped to keep A26L2 within its
adjustment range.
Some of the components in the A26C1
position may not be used. Refer to the Fac-
tory Test Data Sheets for the proper amount
of capacitance.
If the RF Drive when peaked is lower than
25 volts peak to peak, make sure the IPA is
fully working, and that it is not being loaded
down by PA failures. Refer to the ohmmeter
troubleshooting procedure below, as well as
the checks of the PA modules.
If the drive is not low because of a com-
ponent failure, then the IPA power supply
secondary will have to be tapped for a
higher voltage output. For example, moving
a tap from the 105 volt connection to the
120 volt connection will increase the IPA
supply voltage and the RF drive level.
B.3.1.
Ohmmeter Testing the IPA
WARNING
ENSURE ALL AC POWER HAS BEEN RE-
MOVED FROM TRANSMITTER AND
GROUNDING STICK IS USED TO RE-
MOVE ANY RESIDUAL VOLTAGES THAT
MAY BE PRESENT PRIOR TO BEGINNING
THE FOLLOWING PROCEDURE.
a. Turn off AC power to the transmitter.
b. Remove P3, the molex connector, from
A5, the IPA board.
c. Check and remove both fuses. Discard
if open. If not, no further testing is
needed.
d. If more testing is needed, disconnect one
end of the large resistor R11 between
Q12 and Q13.
e. Connect an ohmmeter positive lead to
the center leg of Q11. Touch the negative
lead to the center leg of Q12. The ohm-
meter should read greater than 500k.
This is a test of Q11.
f. Connect the positive ohmmeter lead to
the center leg of Q12. Put the negative
lead on JP1. The ohmmeter should read
greater than 500k. This is a test of Q12.
g. Refer to paragraphs on Handling MOS-
FET’s and Testing MOSFET’s before
replacing any transistors.
h. Connect an ohmmeter positive lead to
the center leg of Q14. Touch the negative
lead to the center leg of Q13. The ohm-
meter should read greater than 500k.
This is a test of Q14.
i. Connect the positive ohmmeter lead to
the center of Q13. Put the negative lead
on JP1. The ohmmeter should read
greater than 500k. This is a test of Q13.
j. Refer to paragraphs on Handling MOS-
FET’s and Testing MOSFET’s before
replacing any transistors.
NOTE
Reconnect the large resistor previously
disconnected when finished with ohmme-
ter testing the IPA.
B.4.
Handling MOSFET’s
Due to the fragile nature of the gate of a
MOSFET, special care in their handling is
required. The gate junction may be de-
stroyed by static electricity if the static elec-
tricity is allowed to discharge through the
MOSFET. For example, walking across a
carpet to pick up a MOSFET that is not
protected by antistatic packaging could re-
sult in the destruction of the MOSFET. A
static charge could build up on a person as
Rev. AE 03-05-2002
888-2314-001
B-1
WARNING: Disconnect primary power prior to servicing.
Summary of Contents for Gates One 994 9202 002
Page 4: ......
Page 6: ...iv 888 2314 001 Rev X WARNING Disconnect primary power prior to servicing...
Page 8: ...vi 888 2314 001 Rev X WARNING Disconnect primary power prior to servicing...
Page 28: ...2 12 888 2314 001 Rev AC 2 29 00 WARNING Disconnect primary power prior to servicing...
Page 76: ...C 6 888 2314 001 Rev AE 03 05 2002 WARNING Disconnect primary power prior to servicing...
Page 82: ...E 4 888 2314 001 Rev AE 03 05 2002 WARNING Disconnect primary power prior to servicing...
Page 88: ...F 6 888 2314 001 Rev AE 03 05 2002 WARNING Disconnect primary power prior to servicing...
Page 96: ...H 2 888 2314 001 Rev AA 8 18 1999 WARNING Disconnect primary power prior to servicing...
Page 104: ...K 2 888 2314 001 Rev AE 03 05 2002 WARNING Disconnect primary power prior to servicing...
Page 108: ...L 2 888 2314 001 WARNING Disconnect primary power prior to servicing...