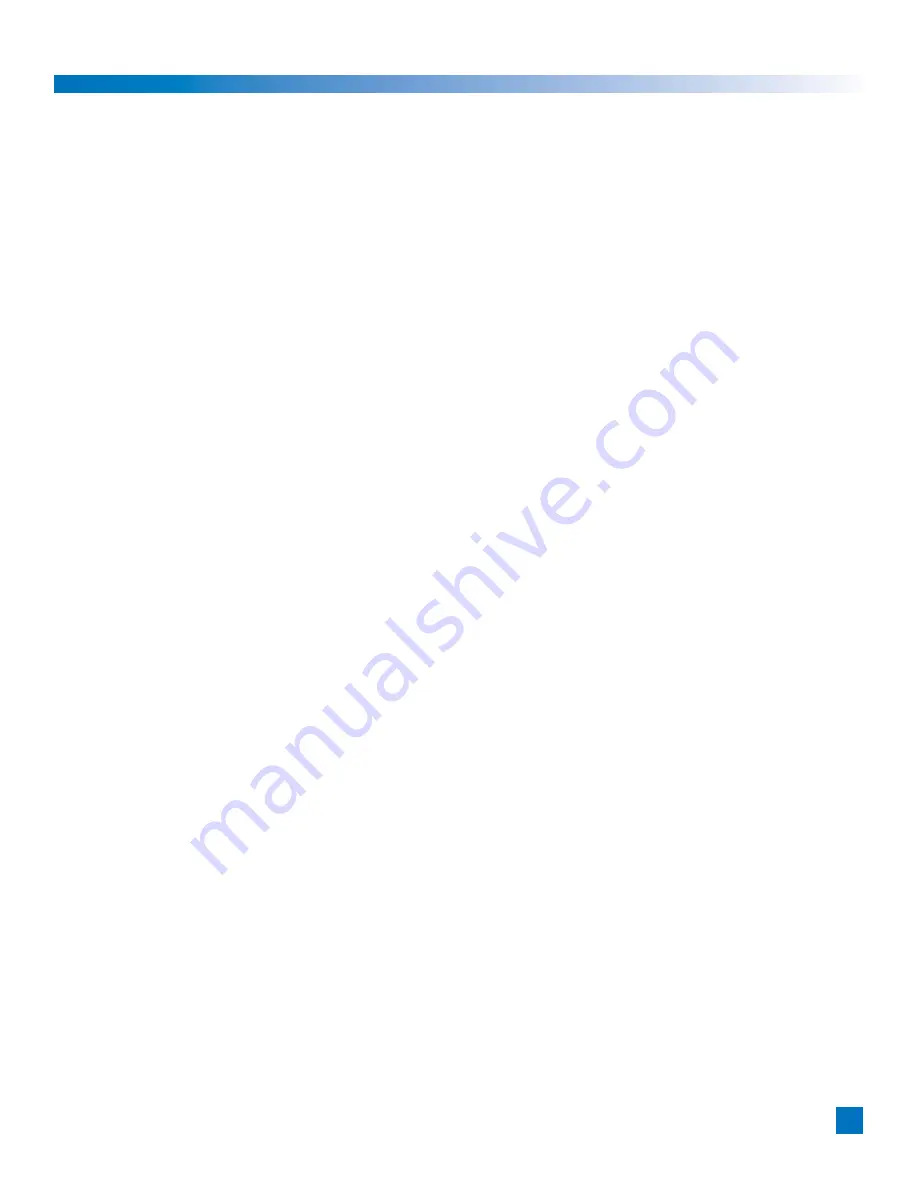
Harmonic Drive LLC 800-921-3332
CAUTIONS FOR ACTUATORS IN OPERATIONS
Do not exceed the allowable torque of the actuator.
• Be aware, that if a load arm attached to the output hits by accident an obstacle, the output shaft may become uncontrollable.
Never connect cables directly to a power supply socket.
• An actuator must not be operated without a corresponding driver.
• Failure to observe this caution may lead to injury, fire or damage of the actuator.
Protect the actuator from impact and shocks
• Do not use a hammer to position the actuator during installation
• Failure to observe this caution could damage the encoder and may cause uncontrollable operation.
• Avoid handling of the actuator by its cables.
• Failure to observe this caution may damage the wiring, causing uncontrollable or faulty operation.
CAUTIONS FOR DRIVERS IN APPLICATION DESIGN
Always use drivers under the following conditions:
•
Mount in a vertical position keeping sufficient distance to other devices to let heat generated by the driver radiate freely.
•
Ambient temperature: 0º to 50º
•
Ambient humidity: less than 95% RH (Non condensation)
•
No contamination by water, oil or foreign matters
•
No corrosive, inflammable or explosive gas Use sufficient noise suppressing means and safe grounding.
•
Keep signal and power leads separated.
•
Keep leads as short as possible.
•
Ground actuator and driver at one single point, minimum ground resistance class: D (less than 100 ohms)
•
Do not use a power line filter in the motor circuit. Pay attention to negative torque by inverse load.
–Inverse load may cause damages of drivers.
•
Please consult our sales office, if you intent to apply products for inverse load. Use a fast-response type
ground-fault detector designed for PWM inverters.
•
Do not use a time-delay-type ground-fault detector.
CAUTIONS FOR DRIVERS IN OPERATIONS
Never change wiring while power is active:
•
Make sure of power non-active before servicing the products.
•
Failure to observe this caution may result in electric shock or personal injury.
Do not touch terminals or inspect products at least 5 minutes after turning OFF power.
•
Otherwise residual electric charges may result in electric shock.
•
Make installation of products not easy to touch their inner electric components. Do not make a voltage resistance test.
•
Failure to observe this caution may result in damage of the control unit.
•
Please consult our sales office, if you intent to make a voltage resistance test.
•
Do not operate control units by means of power ON/OFF switching.
•
Start/stop operation should be performed via input signals.
•
Failure to observe this caution may result in deterioration of electronic parts.
DISPOSAL OF AN ACTUATOR, A MOTOR, A CONTROL UNIT AND/OR THEIR PARTS
•
All products or parts have to be disposed of as industrial waste.
•
Since the case or the box of drivers have a material indication, classify parts and dispose them separately.
2
FHA-C series Safety Guide
Summary of Contents for FHA Series
Page 2: ...FHA C series...