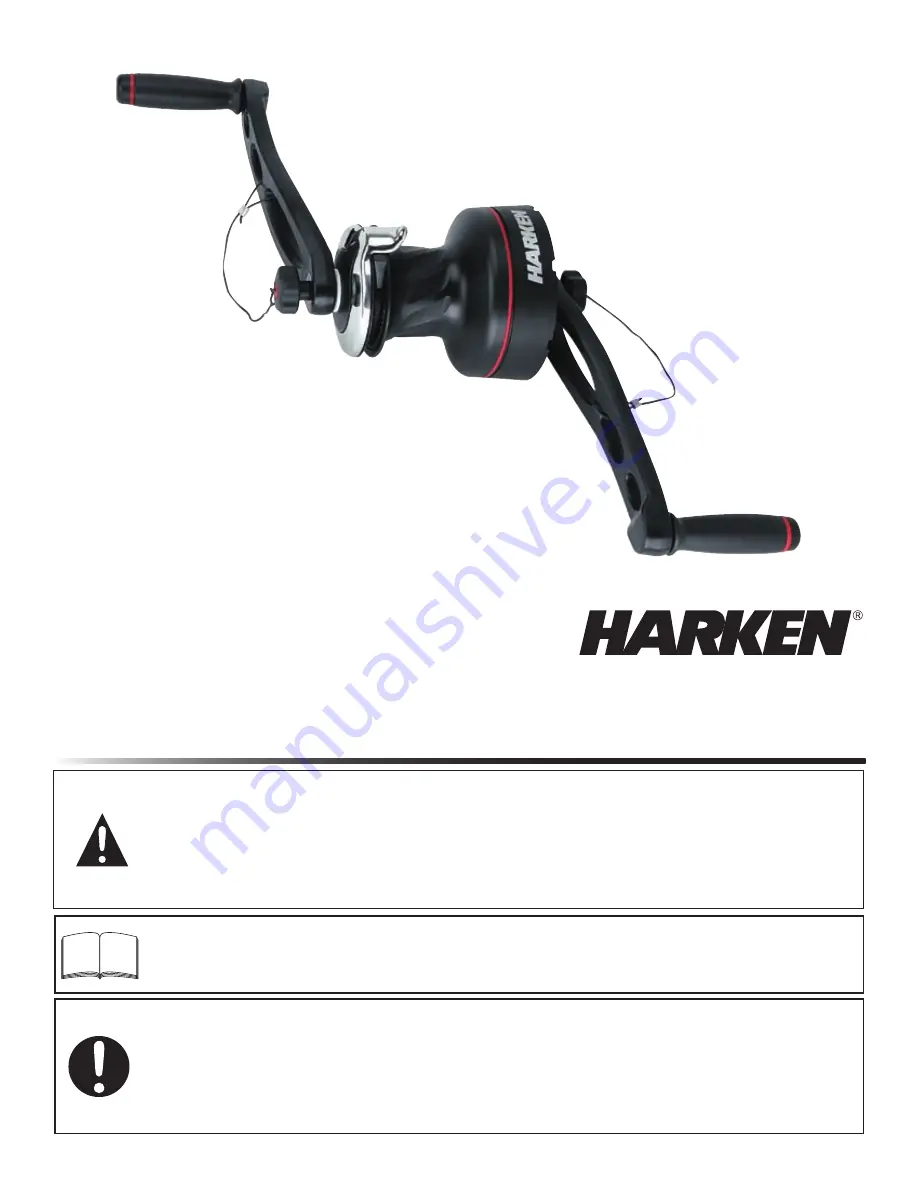
ACCESS WINCH WITH HANDLES
40.2STAACCSH
Instruction Manual
Harken does not accept any responsibility for damage or harm caused by failure to follow the safety
requirements and instructions in this manual.
The manufacturer cannot be liable for damage, injury or consequential loss resulting from installation
or servicing by unqualified personnel.
The manufacturer will also not be liable for damage, injury, or consequential loss resulting from
incorrect operation or modification of the equipment.
Please read these instructions carefully before operating equipment.
Keep these instructions in a safe place for future reference.
i
This product, as supplied by Harken, is considered to be applicable to general lifting operations and
is not intended to lift persons. Should this product be incorporated into systems for lifting persons,
it becomes “partly completed machinery” and, when appropriate additional safety devices are added,
must be certified for its intended application. Such systems are classified as “machinery for lifting
persons” and would require separate CE marking. Alternatively such systems may be classified as
personal protective equipment and would be within the scope of the PPE Directive.