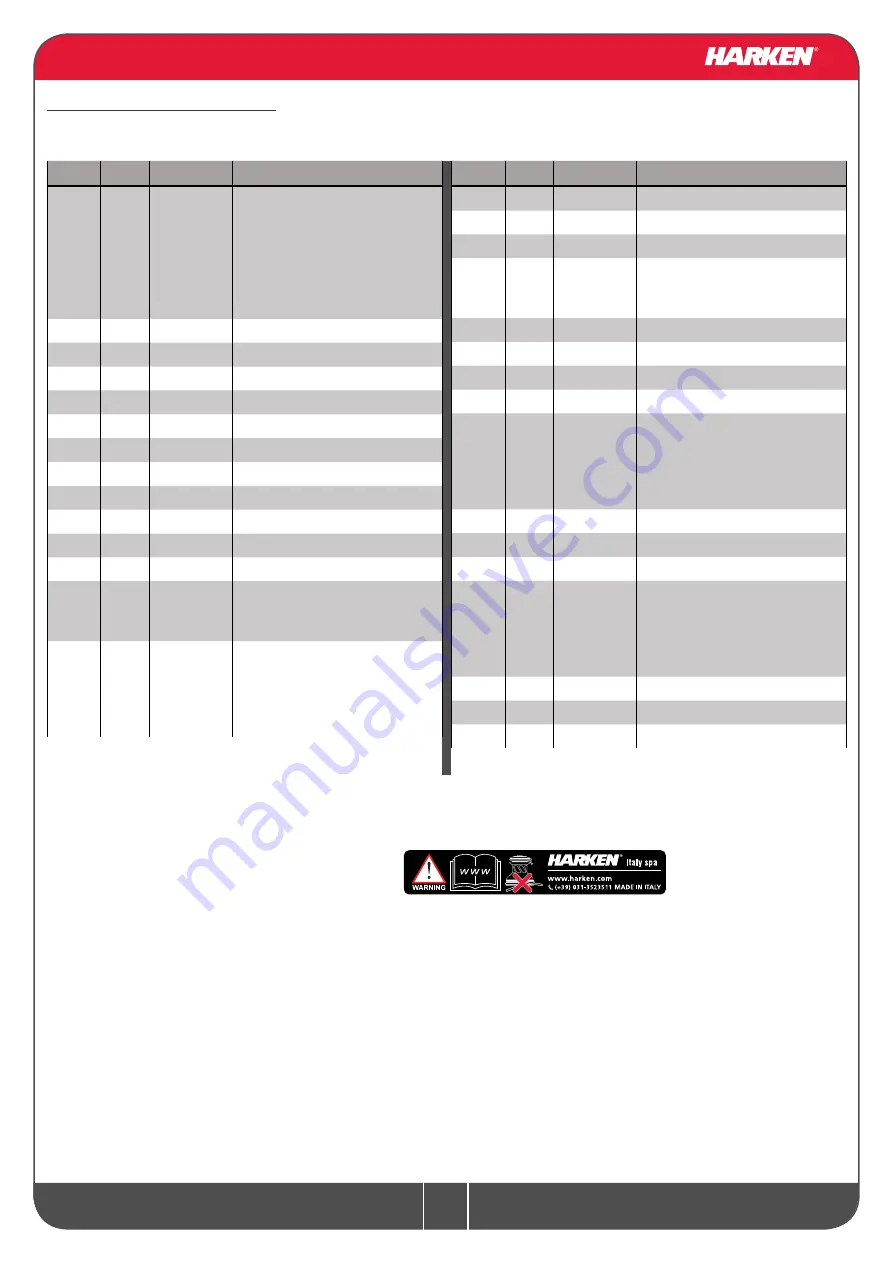
29
Radial Winch
35.2 ST E/HY
Installation and Maintenance Manual
*Available with service kit; see website www.harken.com
**Winch product sticker
Radial Winch 35.2 STCCC
CCC = All-Chrome bronze
Pos.
Q.ty Code
Description
1
1
1
1
1
1
A97160700
S413350080
S4130900A7
S413960085
S413330085
Assembly Base Winch 35 BBB/CCC EL/HY
Base W35
Heli-coil M6x9
Roller Ø6x19
Bushing Ø22xØ25x8.5
Bushing Ø9xØ11x12
Bushing Ø12xØ14x11
2
1
S413020004
Gear Z12
3
1
S413030004
Pawls Carrier Ø8xN2
4
4
S000080003
Pawl Ø8*
5
4
S000380001
Pawl Spring Ø8*
6
1
S412830041
Gear Z23
7
1
S413000004
Pin Ø9x55
8
1
S279090002
Washer 36x9,5x1
9
1
S415650004
Ratchet Gear Z18
10
1
S412850041
Pinion Z13
11
1
S413120002
Washer Ø22.5xØ45x1
12
1
S413070004
Pin Ø9-Ø12x32.5
13
1
2
A94130500
S414900080
Assembly Gear Z20
Gear Z20
Bushing Ø12xØ14x8
14
1
2
1
A94131100
S414890080
S4130900A7
Assembly Housing Winch 35
Housing Winch 35
Bushing Ø9xØ11x7
Heli-coil M6x9
Bushing Ø22xØ25x8.5
Pos.
Q.ty Code
Description
15
6
M0635103
Socket head screw M6x16 UNI 5931
16
1
S413150082
Washer Ø62xØ80x1.5
17
2
A74136000
Bearing Ø56xØ68x24
18
1
1
A94149600
S413880002
Assembly Central Shaft W35EL/HY
Central Shaft Pred. W35
Washer Ø17.2xØ32x1.5
19
Winch Serial Number Sticker
20
1
S4129400A0
Stripper arm support
21
1
S681040043
Drum CCC W35
22
1
S281680097
Red line
23
1
1
4
A96811900
S413610080W
S385970001
Assembly Jaws Winch 35/40 CCC
Lower Jaw W35/40 CCC
Upper Jaw W35-40 RAL9003
Peeler W20 - 40 RAL9003
SPRING
24
4
M0601803
Screw UNI EN ISO 1207 - M6x35 - A4
25
1
S414200019
Stripper Arm W35/40
26
3
M6007103
Screw M6x50 UNI6107
27
1
1
1
1
A94149300
S414940085
S414930003
M0679797
Assembly Socket W35-80 EL/HY
Socket Handle W20/80
Washer Ø25xØ15x4
Nut Screw for Disconnect Rod
O ring RC 2025 series
28
1
A76811100
Cover W35 CCC
29
Winch Product Sticker**
30
1
S414970002
Disconnect Rod W35 EL/HY