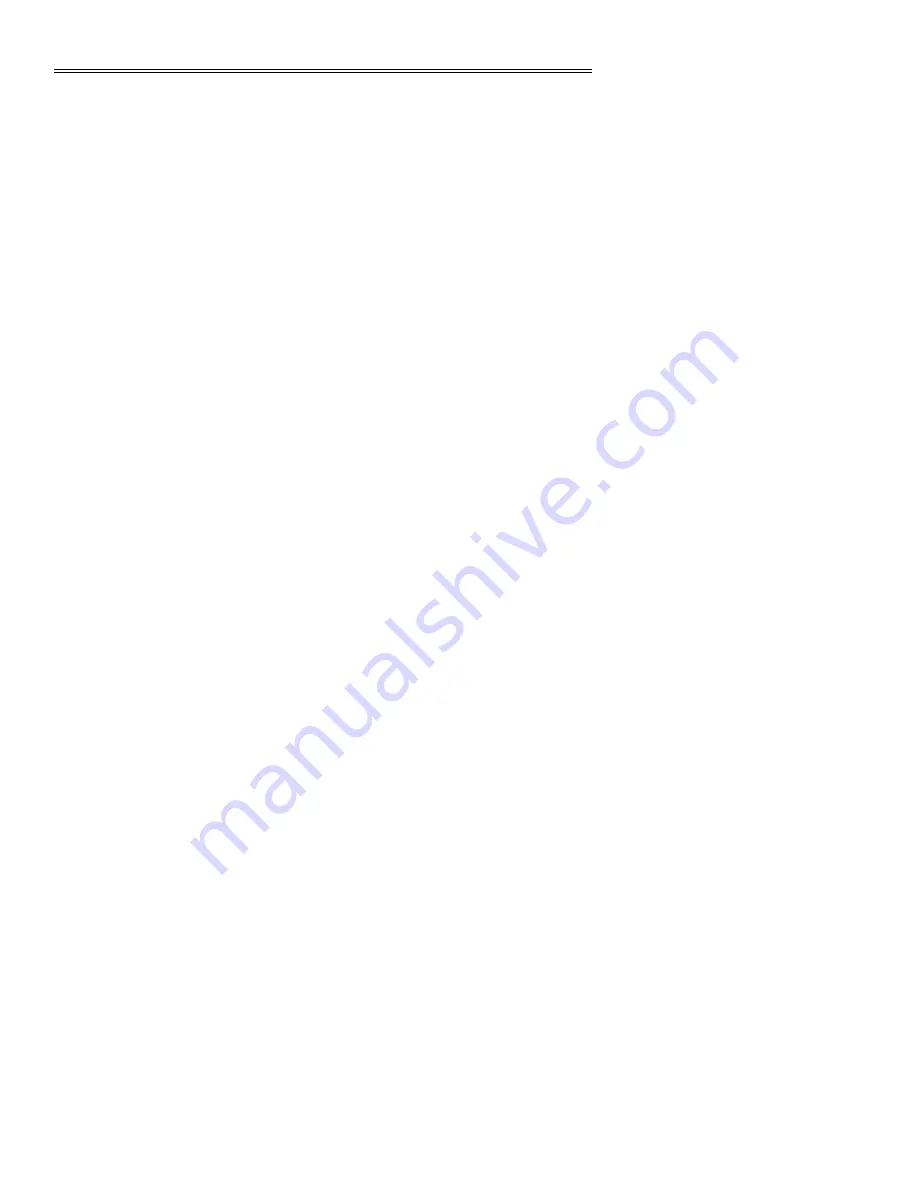
HI 2151 SERIES WEIGHT CONTROLLERS REMOTE I/O OPTION
1-2
should also read the Installation and Operation manual of the HI
2151WCs.
Information contained in this manual is subject to change. Always
check the latest version of this manual at our web site (http://www.har-
dysolutions.com) before beginning system design. This product incor-
porates technology which is licensed by Allen-Bradley Company Inc.
Allen-Bradley does not technically approve, warrant or support this
product. All warranty and support for this product is provided by Hardy
Process Solutions Inc. PLC
®
, PLC-2
®
, PLC-3
®
, PLC-5
®
, SLC500
®
Series are registered trademarks of the Allen-Bradley Company, Inc.
Common Applications
The HI 2151WC series can be used in conjunction with Allen-Bradley
programmable controllers to tackle a variety of process control needs.
The most basic use of the interface is to simply allow the programma-
ble controller to read weight data from one or more HI 2151WC series
weight controllers. In addition to reading weight some other applica-
tions are:
•
Filling
•
Dispensing
•
Batch Weighing Control
•
Monitoring Rate of Flow
•
Evaluating Totalized Weight
•
Check Weighing
•
Weight Level Alarming
NOTE:
There are two standard and six optional setpoint relays which provide control of
ingredient weighments and weight level alarming.
Monitoring
Weighing
Parameters
The HI 2151WC series weight controllers are capable of calculating
five types of weight data, including the standard Gross and Net
weights. In addition to the standard Gross and Net weights there are
three options such as Peak Force, Totalized Weight (block transfer
only), and Rate-of-Change or mass flow rate entering or leaving a ves-
sel.
Short Glossary of
Terms
1. Gross Weight - is used to describe the total weight of the container
and the contents.
2. Net Weight - is the weight of the contents of the container only.
3. Tare Value - The action of adjusting out the known weight of the
container from the total indicated weight, so that the indicator reads
weight directly.
4. Dead Load - The weight of the vessel and other equipment which
will be ignored during zero calibration.
Tare Value
Current Gross Weights becomes the Tare value by pushing the Tare
Push Button on the front panel of the HI 2151WC, remote functions
contact closure, discrete write or block transfer command by the PLC,