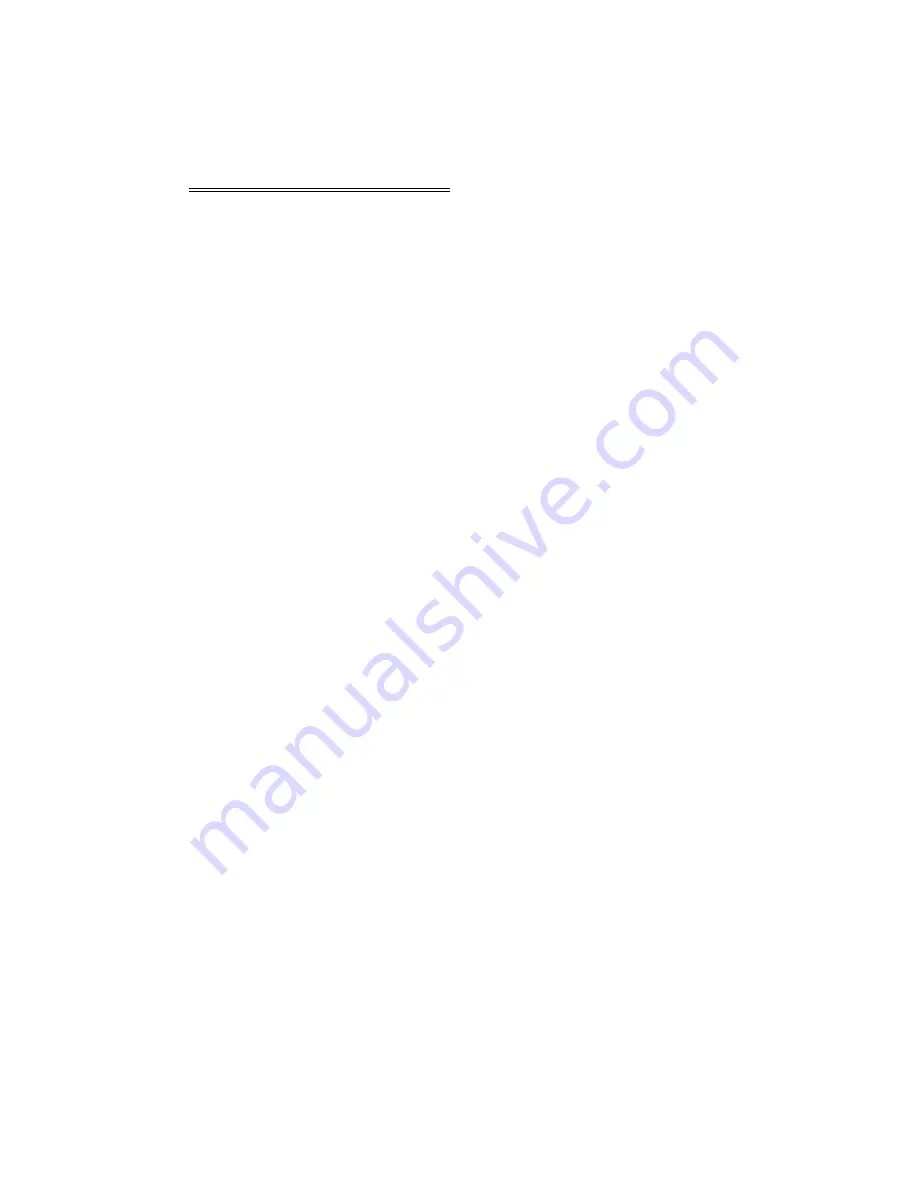
HI 1756-WS WEIGH SCALE MODULE
4-2
LEDS
Scale Data
LEDs
Flashing Green Error No Calibration
Steady Green
Running (Normal)
Steady Red
Error Read Failure or Error eeprom
write. Contact HI Customer Sup-
port
Flashing Red
Read Convert Error.
LED is Off
Channel is Inactive
OK Module
Status LED
Brief Steady
During power up the LED lights
Red for about one second.
Flashing Green
In Program mode. (Normal)
Steady Green
In Run Mode. (Normal)
Steady Red
Config. Fault The eeprom
(Backplane
checksum failed - bad serial eeprom
Available)
data or blank serial eeprom. Contact
HI Customer Support.
Steady Red
Internal Hardware watchdog timer
fault (e.g. bad Hardware or Firm-
ware). ASIC is non-operational.
Flashing Red
Communication Error.
Reset Module
Message
Modules with communication errors (indicated by a
flashing red Module Status LED) can be reset by a
reset message.
•
Message Type: CIP Generic
•
Service Code 5 (Hex)
•
Class Name: 1
•
Instance Name: 1
Setting Up
Communications
Between the PLC and
the HI 1756-WS (-2WS)
Weigh Scale Module
Follow these steps to set up communication between
the ControlLogix PLC and the Weigh Scale Module.
The steps require that you have a new or open RS
Logix
®
5000 project. For instructions, see your RS
LOGIX 5000 manual.
Step 1.
Look for a list of folders on the left side of
the screen. Scroll to and select the I/O
Config folder, which will open a menu.
Summary of Contents for A Series
Page 14: ...HI 1756 WS WEIGH SCALE MODULE 1 6 ...
Page 28: ...HI 1756 WS WEIGH SCALE MODULE 3 10 ...
Page 52: ...HI 1756 WS WEIGH SCALE MODULE 4 24 ...
Page 62: ...HI 1756 WS WEIGH SCALE MODULE 6 2 FIG 6 2 DISCRETE DATA ...
Page 72: ...HI 1756 WS MANUAL 7 10 ...
Page 80: ...HI 1756 WS MANUAL Write Parameters WRITEPARAM 4 18 Z Zero Command ZEROCMD 4 12 ...