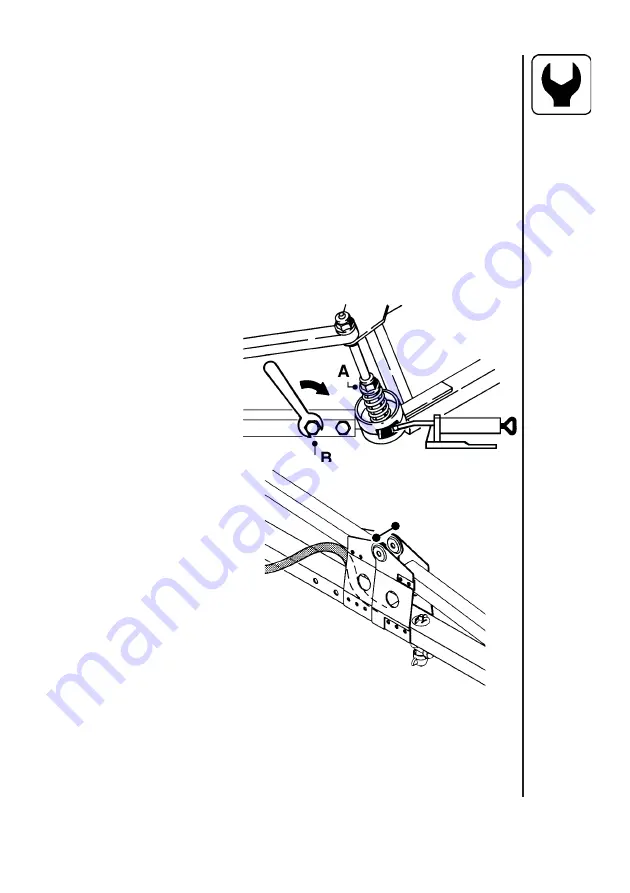
15
Re-adjustment of the boom
After having used the sprayer for some days the boom should be
adjusted as follows:
When adjusting the sprayer must be on level ground with unfolded
boom.
Boom breakaway
The function of the breakaway is to prevent or reduce boom damage if
it should strike an object or the ground. If it is over-tight, it will not
function. If it is too loose, it will yawn (forward and back movement)
under spraying.
Lubricate coupling before
adjusting spring tension.
Slacken nut A to decrease
breakaway resistance. Do
not overtighten; better
loose than over-tight. Minor
adjustments in the field
may be necessary.
Ensure also channel bolts
B are tight.
Outer section
The hinge should be firm. If
tight it is difficult to fold. To
adjust, tighten or loosen
nuts C.
C
Summary of Contents for NL Series
Page 1: ...NL Instruction book 674202 GB 10 1995 www hardi international com ...
Page 15: ...13 1 X 40 2 A X 12 B X 40 3 X 20 16 17 17 6 10 19 ...
Page 16: ...14 4 X 40 5 X 40 15 15 ...
Page 19: ...17 Model 1302 Model 320 ...
Page 35: ...33 22 Organise hoses it may be necessary to shorten some of them Secure with straps ...
Page 36: ...34 A6 600 foot ...
Page 37: ...35 320 A8 ...
Page 38: ...36 A10 1202 foot ...
Page 39: ...37 1303 foot A12 ...
Page 40: ...38 B5 Unit M 70 70 HT ...
Page 41: ...39 Distributor B6 ...
Page 42: ...40 B300 Damper HJ73 ...
Page 43: ...41 SB 6 8 10 m D3 ...
Page 44: ...42 D5 SB 12 m ...
Page 45: ...43 Boom tube 3 8 cap D901 ...
Page 46: ...44 E3 NK 300 400 ...
Page 47: ...45 NL NK 300 400 E102 ...
Page 48: ...46 E103 NL NK 600 800 ...
Page 50: ...48 Notes ...
Page 52: ...HARDI INTERNATIONAL A S Herthadalvej 10 DK 4840 Nørre Alslev DENMARK ...