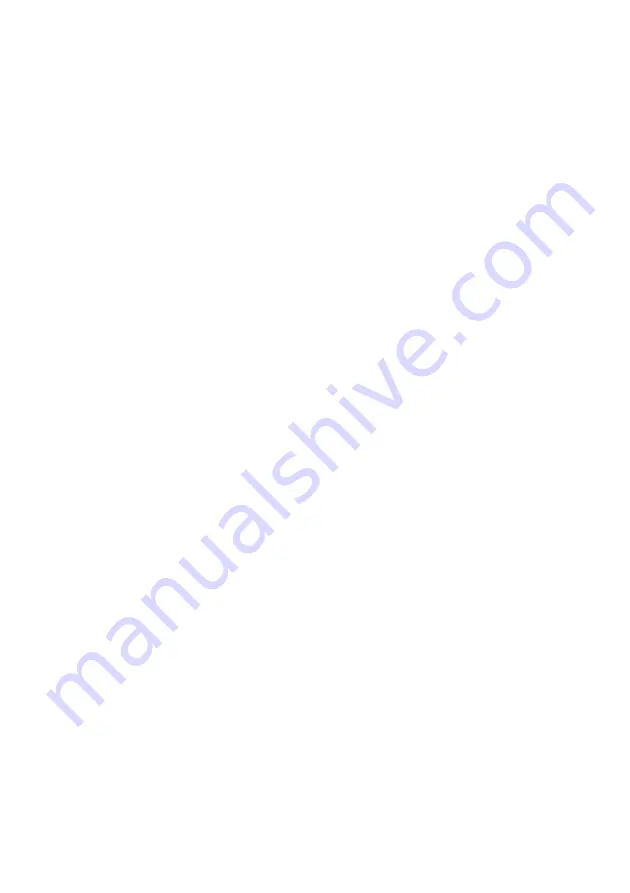
1
JAZZ
Instruction book
674097-GB-98/4
HARDI INTERNATIONAL A/S reserve the right to make changes in design or to add new features
without any obligation in relation to implements purchased before or after such changes.
Contents
EU Declaration of Conformity ......................................... 2
Operator safety .............................................................. 3
Description ..................................................................... 4
Function diagram BK operating unit ............................... 5
Connecting the sprayer .................................................. 6
Transmission shaft .................................................... 6
Rear lights (if fitted) ................................................... 8
Roadworthyness ....................................................... 8
Operating instructions .................................................... 8
Filling the main tank .................................................. 8
Operation of the boom .............................................. 9
Adjustment of the BK controls ................................ 10
Drain valve operation .............................................. 11
Maintenance ................................................................. 12
Cleaning the sprayer .................................................... 12
Filters ...................................................................... 14
Lubrication .............................................................. 14
Re-adjustment of the boom .................................... 16
Changing of valves and diaphragms ...................... 17
Changing the ball seat in operating unit ....................... 18
Nozzle tubes and fittings ......................................... 18
Replacement of transmission
shaft protection guards ........................................... 19
Replacement of transmission shaft cross journals. 19
Off-season storage ....................................................... 20
Operational problems ................................................... 21
Technical specifications ............................................... 22
Pictorial symbols .......................................................... 25
Spare parts ................................................................... 32
Summary of Contents for JAZZ
Page 15: ...15 1 X 40 2 A X 12 B X 40 3 X 40 4 X 40 17 6 7 19 10 18 16 8m SB ...
Page 26: ...26 A10 1202 foot ...
Page 27: ...27 Unit BK 180K 92 B9 ...
Page 28: ...28 B13 Distributor BK 180K 94 ...
Page 29: ...29 Damper HJ73 B300 ...
Page 30: ...30 D2 SB 6 8 10 m ...
Page 31: ...31 Boom tube SNAP FIT D903 ...
Page 32: ...32 E2 BL 200 300 ...
Page 33: ...33 15 l Clean water tank K107 ...
Page 35: ...35 Notes ...
Page 36: ...36 Notes ...