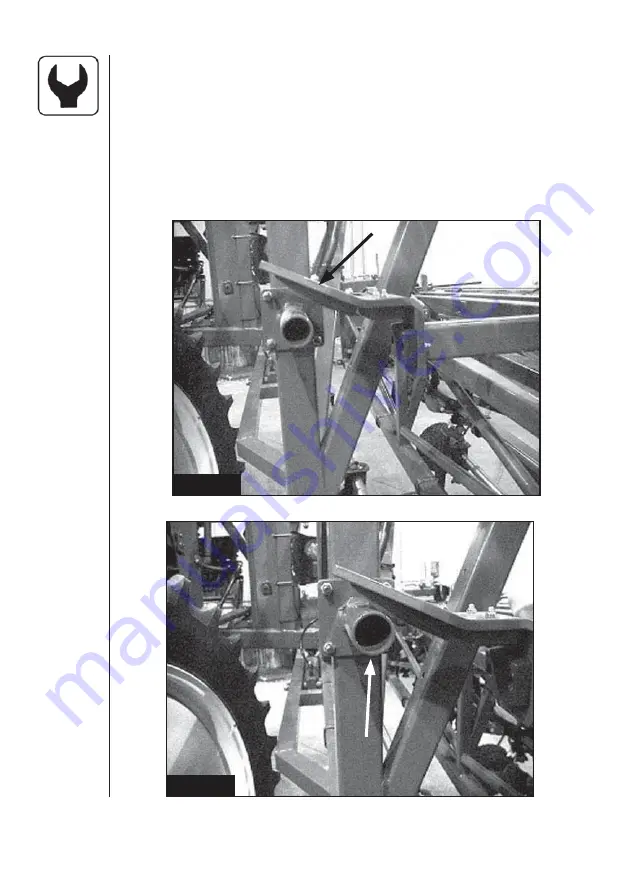
26
HARDI
®
FORCE™ BOOM OPERATOR’S MANUAL
Adjustment of transport stops 120' and 132'
Open the intermediate wing just enough to let the boom rest (
A
)(Fig.
22) move off the tube mount (
B
)(Fig. 23). In order to get maximum
engagement when completely folded, loosen the U-bolts on the tube
mount (
B
)(Fig. 23) and move it up until it makes contact with the pad
on boom rest (
A
)(Fig. 22). Test the engagement by completely opening
and then closing the wings. Re-adjust if necessary.
Fig. 22
Fig. 23
B
A
Summary of Contents for FORCE
Page 1: ...FORCE Boom Operator s Manual 10637903 10 04 ...
Page 2: ......
Page 49: ...47 HARDI FORCE BOOM OPERATOR S MANUAL 12 0 NOTES ...
Page 50: ...48 HARDI FORCE BOOM OPERATOR S MANUAL NOTES ...
Page 51: ......