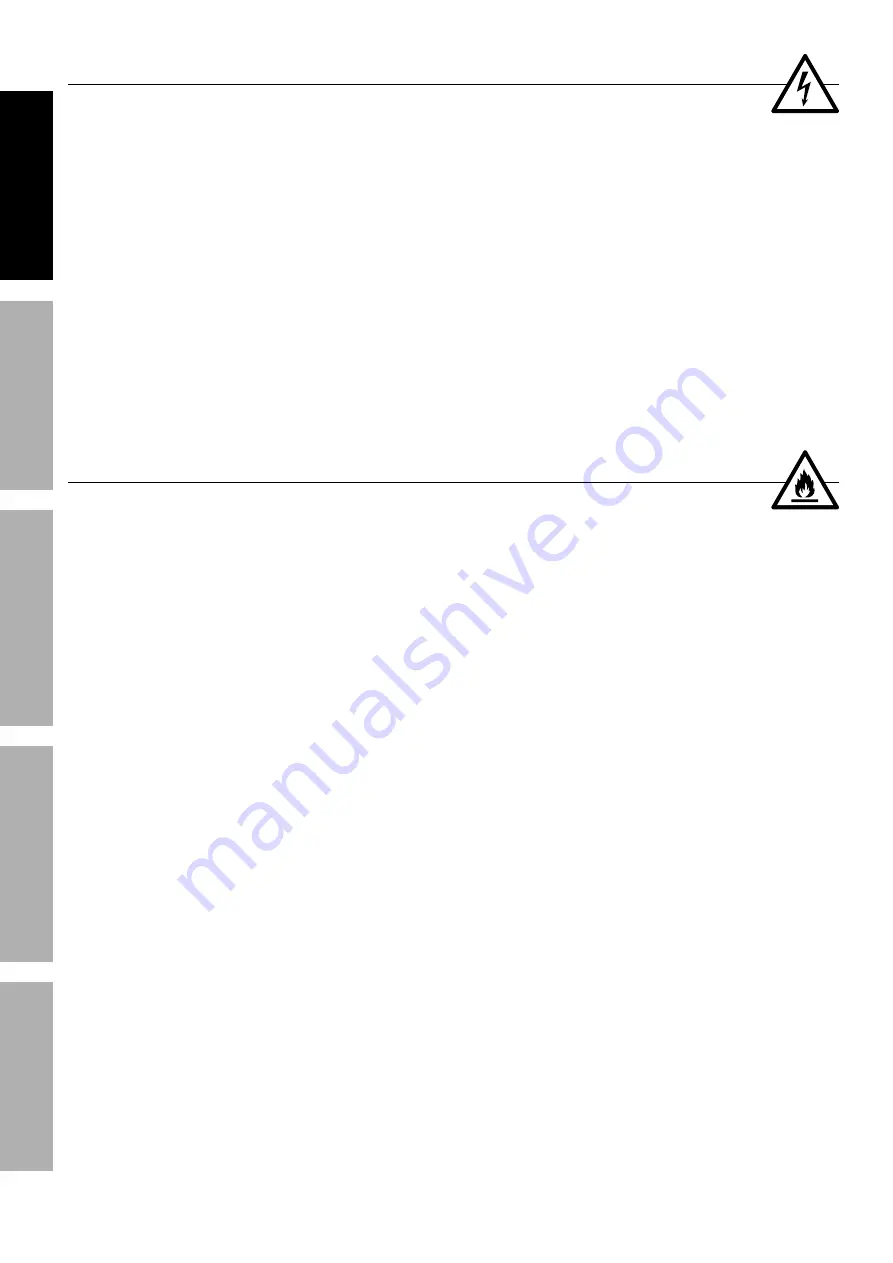
Page 4
For technical questions, please call 1-888-866-5797.
Item 56825
S
AFET
y
M
AINTENAN
c
E
B
ASI
c W
EL
d
IN
g
W
EL
d
IN
g T
Ip
S
SETUP
S
AFET
y
M
AINTENAN
c
E
B
ASI
c W
EL
d
IN
g
W
EL
d
IN
g T
Ip
S
SETUP
Electrical Safety
ELEcTRIc SHOcK can KILL.
1.
Turn off, disconnect power, and
discharge Electrode to ground before setting
down torch/Electrode holder and before service.
2.
do not touch energized electrical parts.
Wear dry, insulating gloves. Do not touch Electrode
holder, Electrode, welding torch, or welding wire with
bare hand. Do not wear wet or damaged gloves.
3.
connect to grounded, gFcI-protected
power supply only.
4.
do not use near water or damp objects.
5.
people with pacemakers should consult their
SK\VLFLDQVEHIRUHXVH
Electromagnetic fields
in close proximity to heart pacemaker could cause
pacemaker interference or pacemaker failure.
6.
do not expose welders to rain or wet conditions.
Water entering a welder will increase
the risk of electric shock.
7.
do not abuse the cord. Never use the cord
for carrying, pulling or unplugging the welder.
Keep cord away from heat, oil, sharp edges
or moving parts.
Damaged or entangled
cords increase the risk of electric shock.
8.
do not use outdoors.
9.
Insulate yourself from the workpiece and
ground.
Use nonflammable, dry insulating
material if possible, or use dry rubber mats,
dry wood or plywood, or other dry insulating
material large enough to cover your full
area of contact with the work or ground.
Fire Safety
ARc ANd SLAg can cause fire.
1.
clear away or protect flammable objects.
Remove or make safe all combustible materials for a
radius of 35 feet (10 meters) around the work area.
Use a fire resistant material to cover
or block all open doorways, windows,
cracks, and other openings.
2.
Keep ABc-type fire extinguisher near
work area and know how to use it.
3.
Maintain a safe working environment.
Keep the work area well lit.
Make sure there is adequate
surrounding workspace. Keep the work area free
of obstructions, grease, oil, trash, and other debris.
4.
do not operate welders in atmospheres
containing dangerously reactive or
flammable liquids, gases, vapors, or dust.
Provide adequate ventilation in work areas
to prevent accumulation of such substances.
Welders create sparks which may ignite flammable
substances or make reactive fumes toxic.
5.
If working on a metal wall, ceiling, etc.,
prevent ignition of combustibles on the
other side by moving the combustibles to a
safe location.
If relocation of combustibles is
not possible, designate someone to serve as
a fire watch, equipped with a fire extinguisher,
during the cutting process and for at least one
half hour after the cutting is completed.
6.
do not weld or cut on materials having
a combustible coating or combustible
internal structure, as in walls or ceilings, without
an approved method for eliminating the hazard.
7.
do not dispose of hot slag in containers
holding combustible materials.
8.
After welding, make a thorough examination
for evidence of fire.
Be aware that easily
visible smoke or flame may not be present
for some time after the fire has started.
9.
do not apply heat to a container that has held
an unknown substance or a combustible
material whose contents, when heated,
can produce flammable or explosive vapors.
Clean and purge containers before applying heat.
Vent closed containers, including castings,
before preheating, welding, or cutting.
Summary of Contents for TITANIUM TIG200
Page 33: ...JRXUD 5RDG DODEDVDV...