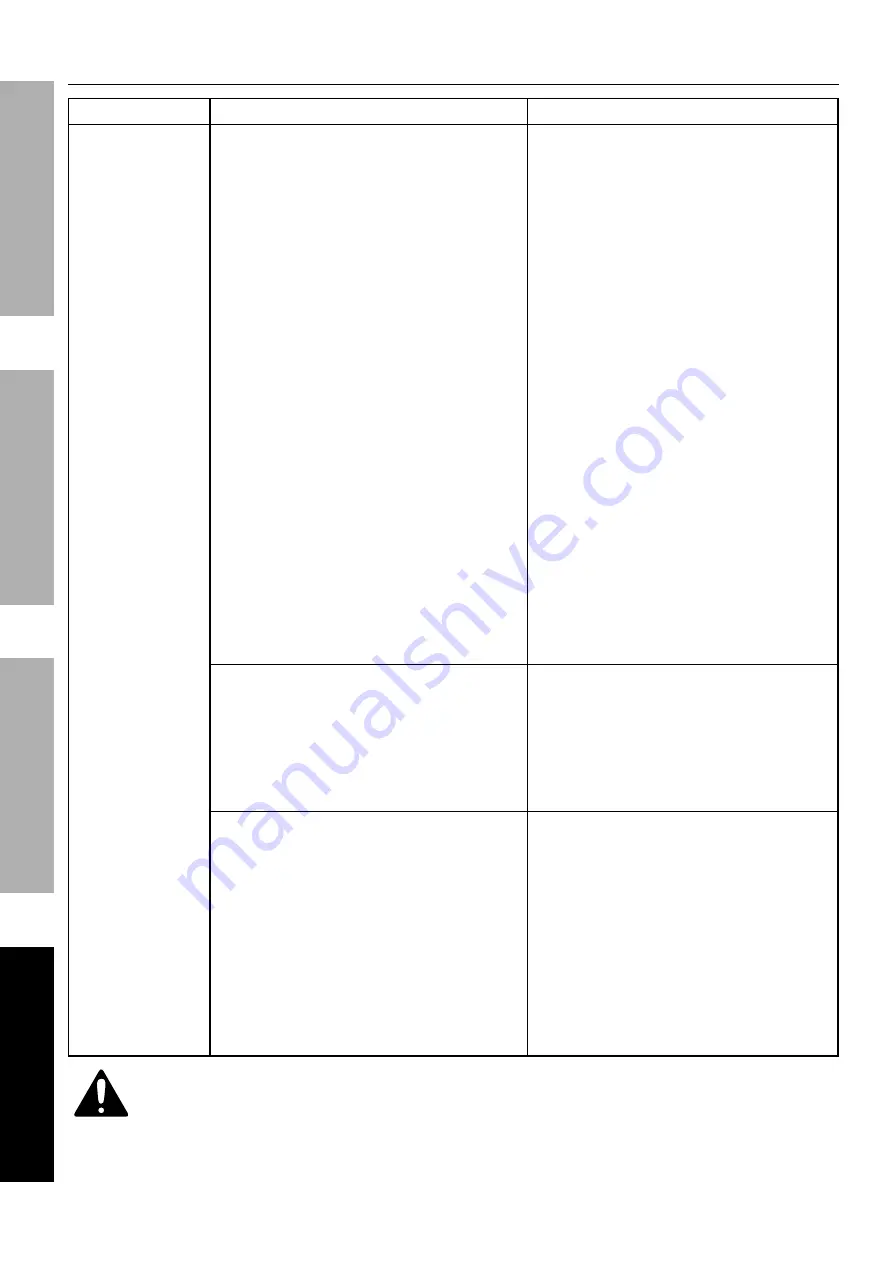
Page 14
For technical questions, please call 1-888-866-5797.
ITEM 57531
S
AFETY
S
ETU
p
INST
ALLA
TION
M
AINTENANCE
Troubleshooting
problem
possible Causes
probable Solutions
Engine will not start
FUEL RELATED:
1. No fuel in tank or fuel valve closed.
2. Choke not in START position, cold engine.
3. Gasoline with more than 10% ethanol used.
(E15, E20, E85, etc.)
4. Low quality or deteriorated, old gasoline.
5. Carburetor not primed.
6. Dirty fuel passageways.
7. Carburetor needle stuck.
Fuel can be smelled in the air.
8. Too much fuel in chamber. This can be
caused by the carburetor needle sticking.
9. Clogged Fuel Filter.
FUEL RELATED:
1. Fill fuel tank with fresh 91+ octane
stabilizer-treated unleaded gasoline and
open fuel valve.
Do not use gasoline with more than
10% ethanol (E15, E20, E85, etc.).
2. Move Choke to START position.
3. Clean out ethanol rich gasoline from fuel
system. Replace components damaged by
ethanol. Use fresh 91+ octane stabilizer-
treated unleaded gasoline only.
Do not use gasoline with more than
10% ethanol (E15, E20, E85, etc.).
4. Use fresh 91+ octane stabilizer-treated
unleaded gasoline.
Do not use gasoline with more than
10% ethanol (E15, E20, E85, etc.).
5. Pull on Starter Handle to prime.
6. Clean out passageways using
fuel additive. Heavy deposits
may require further cleaning.
7.
Gently
tap side of carburetor float
chamber with screwdriver handle.
8. Turn Choke to RUN position.
Remove spark plug and pull the start
handle several times to air out the
chamber. Reinstall spark plug and
set Choke to START position.
9. Replace Fuel Filter.
IGNITION (SPARK) RELATED:
1. Spark plug cap not connected securely.
2. Spark plug electrode wet or dirty.
3. Incorrect spark plug gap.
4. Spark plug cap broken.
5. Incorrect spark timing or
faulty ignition system.
IGNITION (SPARK) RELATED:
1. Connect spark plug cap properly.
2. Clean spark plug.
3. Correct spark plug gap.
4. Replace spark plug cap.
5. Have qualified technician diagnose/
repair ignition system.
COMPRESSION RELATED:
1. Cylinder not lubricated.
Problem after long storage periods.
2. Loose or broken spark plug.
(Hissing noise will occur
when trying to start.)
3. Loose cylinder head or damaged
head gasket. (Hissing noise will
occur when trying to start.)
4. Engine valves or tappets
mis-adjusted or stuck.
COMPRESSION RELATED:
1. Pour tablespoon of oil into
spark plug hole. Crank engine a
few times and try to start again.
2. Tighten spark plug.
If that does not work, replace spark plug.
If problem persists, may have
head gasket problem, see #3.
3. Tighten head.
If that does not remedy problem,
replace head gasket.
4. Have qualified technician adjust/
repair valves and tappets.
Follow all safety precautions whenever diagnosing or servicing the equipment or engine.