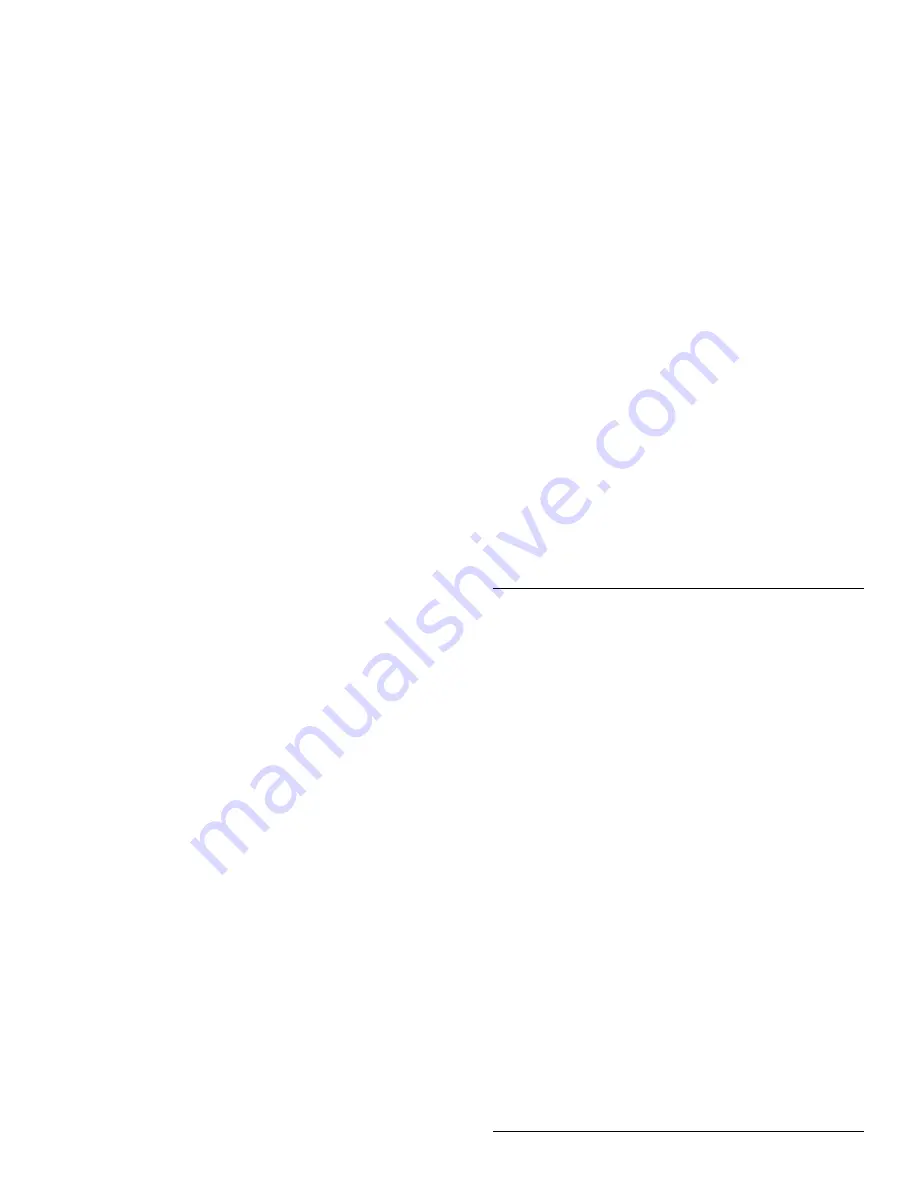
SERVICE AND MAINTENANCE
Failure to open:
Wrong coil or control module pilot;
low line voltage; controlling switch or thermostat not
contacting; coil is burned-out; adjacent shut-off valve
closed; adapter gasket hole not aligned with hole in body
and adapter; dirt packed under Teflon seal ring enabling
excessive blow by; large quantity of dirt particles in
solenoid module passages; dirt blocking internal pilot
passages; main valve seat is dirt jammed.
Failure to close:
Controlling switch or thermostat not
opening contacts; manual-opening stem is turned in;
valve installed in wrong direction; damage or dirt at
main valve seat or pilot seat; piston bleed hole plugged.
Under extreme conditions of liquid or oil “slugging” or
pressure drops exceeding 45 psi (3.1 bar g), special
construction may be required. Contact the factory.
Before opening the regulator or disassembling the
pilot for service, be sure it is isolated from the
system and all refrigerant is removed (pumped out
to zero pressure).
Follow usual refrigeration system
safe servicing procedures. Read the CAUTION section
of this bulletin on page 20.
To check solenoid pilot section of valve, disconnect
the electrical coil. Unscrew the coil nut and remove
washer. Lift coil housing away from valve. Remove the
four solenoid tube screws and remove solenoid tube
from valve. Inspect for dirt and damage to Teflon seat
and stainless steel pilot orifice. Clean, polish or replace
parts as necessary, then reassemble.
¾" through 1¼" (20mm through 32mm):
Use a
3
⁄
8
"
male hexagon wrench to loosen the four adapter bolts,
proceeding slowly to avoid refrigerant which may still
remain in the valve. If piston parts are stuck, remove
the 2" hex bottom cap in order to separate the valve
V-port/seat from the disc piston. Inspect disc and piston
bore for burrs, nicks, and other damage. Remove burrs
and nicks, clean or replace disc piston and Teflon seal
ring as necessary. Long-life seal on disc piston need
only be replaced when damaged or severely worn. If
replacing the disc piston seal, make sure the seal is
properly installed, with the edge up, and does not “twist”
during installation. Inspect V-port/seat and main valve
seat for nicks, marks, etc. The main valve seat may be
lapped by hand or power drill to remove marks. Clean,
polish or replace parts as necessary. If necessary, the
V-port tapered seat may be reconditioned by removing
up to 0.04" (1mm) of Teflon from it on a lathe. Lightly
lubricate all parts and gaskets with soft rag containing
refrigerant oil. Align hole in valve body, adapter gasket,
and adapter to assure proper operation. Reassemble
valve. Carefully check valve for leaks before returning
it to service.
1½" through 6" (40mm through 150mm):
Loosen
adapter bolts using a 12" adjustable wrench (15"
wrench for 5" and 6" valves), being careful to avoid any
refrigerant which may still remain in the valve. If disc
piston is difficult to remove, insert a ¼"-20 threaded
screw (
3
⁄
8
"-16 for 5"& 6" valves) into center of piston and
lift straight-up. Inspect piston and piston bore for burrs,
nicks and other damage. Remove burrs and nicks, clean
or replace piston as necessary. Long-life seal on disc
piston need only be replaced when damaged or severely
worn. If replacing the disc piston seal, make sure the
seal is properly installed, with the edge up, and does
not “twist” during installation. These valves also have
a removable stainless steel main valve seat. To remove
seat ring for inspection, first remove small hex head seat
screw. Turn the seat ring counterclockwise by turning
it out with a wrench and a steel bar tool positioned
horizontally or by carefully tapping the seat ring notch
with a punch and a hammer. Inspect the V-port/seat
and main valve seat for nicks, marks, and divots. The
main valve seat may be lapped by hand or power drill
to remove marks. Grease and replace the seat seal
O-ring. Clean and polish, or replace the par ts as
necessary. If necessary, the V-port tapered seat may be
reconditioned by removing up to 0.04" (1 mm) of Teflon
from it on a lathe. Lightly lubricate all parts and gaskets
with a soft rag containing refrigerant oil. Align the hole
in the valve body, adapter gasket, and adapter to assure
proper operation. Reassemble the valve. Carefully check
the entire valve for leaks before restoring it to service.
MANUAL OPENING
The manual-opening stem is designed to open the
valve, allowing upstream and downstream pressures to
equalize when needed for servicing, but not necessarily
to create a full-flow condition. The stem is located on
the top of the adapter cover. Slowly remove the seal cap
from the manual-opening stem, being cautious to avoid
any refrigerant which may have collected under the cap.
Using an appropriate wrench, turn the stem in (clockwise)
to open the valve manually; counterclockwise to return
the valve to automatic operation. Do not leave the stem
partially open because it may be dynamically damaged.
ABBREVIATIONS
BW:
Butt Weld end to match American Pipe
Schedule 40
CRN:
Canadian Registration Number
CSA:
Canadian Standards Association
Cv:
Valve capacity factor GPM (U.S.) of water at 1 psi
differential
FPT:
Female Pipe Thread, American National Standard
Kv:
Valve capacity factor m
3
/hr of water at 1 bar g
differential
mA:
milliampere
MPT:
Male Pipe Thread, American National Standard
NEMA:
National Electrical Manufacturers
Association: Class 4, watertight, approximate
equivalent to IP65; Class 1, general purpose,
approximate equivalent to IP20
NPT:
National Pipe Thread
ODS:
Outside Diameter Sweat, for copper tubing
PLC:
Programmable Logic Controller
psig:
Pounds per square inch, gauge
R/S:
Refrigerating Specialties Division, Parker
Hannifin Corp.
SPDT:
Single Pole Double Throw
SW:
Socket Weld to accommodate American and API pipe
WN or Weld:
Weld Neck to match American Pipe
Schedule 40
19
R429d
AUG 2015