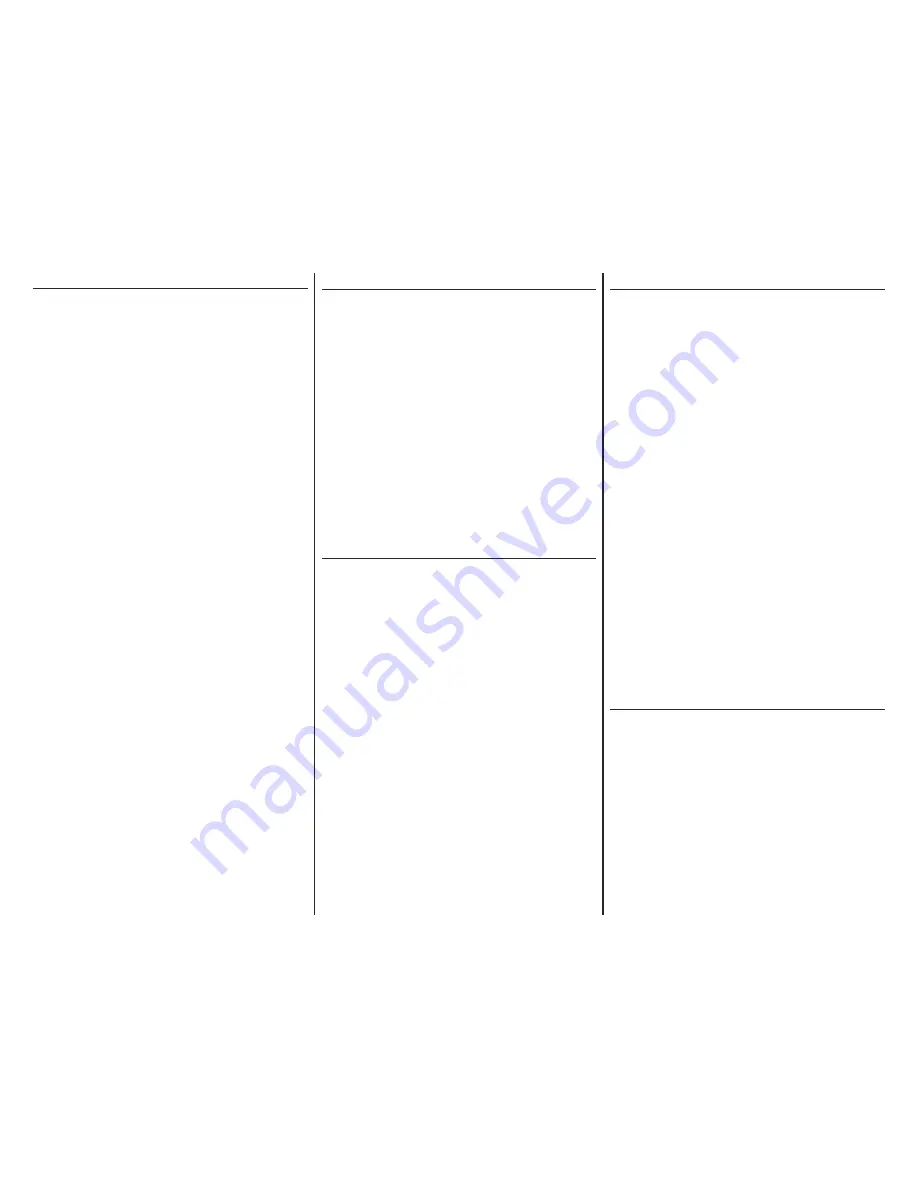
53
Hangar 9 Taylorcraft 20cc Assembly Manual
DAMAGE LIMITS
HORIZON SHALL NOT BE LIABLE FOR SPECIAL,
INDIRECT OR CONSEQUENTIAL DAMAGES, LOSS
OF PROFITS OR PRODUCTION OR COMMERCIAL
LOSS IN ANY WAY CONNECTED WITH THE
PRODUCT, WHETHER SUCH CLAIM IS BASED IN
CONTRACT, WARRANTY, NEGLIGENCE, OR
STRICT LIABILITY. Further, in no event shall the
liability of Horizon exceed the individual price of the
Product on which liability is asserted. As Horizon has
no control over use, setup, final assembly,
modification or misuse, no liability shall be assumed
nor accepted for any resulting damage or injury. By
the act of use, setup or assembly, the user accepts all
resulting liability.
If you as the Purchaser or user are not prepared to
accept the liability associated with the use of this
Product, you are advised to return this Product
immediately in new and unused condition to the place
of purchase.
Law: These Terms are governed by Illinois law
(without regard to conflict of law principals).
SAFETY PRECAUTIONS
This is a sophisticated hobby Product and not a toy. It
must be operated with caution and common sense
and requires some basic mechanical ability. Failure to
operate this Product in a safe and responsible manner
could result in injury or damage to the Product or
other property. This Product is not intended for use by
children without direct adult supervision. The Product
manual contains instructions for safety, operation and
maintenance. It is essential to read and follow all the
instructions and warnings in the manual, prior to
assembly, setup or use, in order to operate correctly
and avoid damage or injury.
QUESTIONS, ASSISTANCE, AND REPAIRS
Your local hobby store and/or place of purchase
cannot provide warranty support or repair. Once
assembly, setup or use of the Product has been
started, you must contact Horizon directly. This will
enable Horizon to better answer your questions and
service you in the event that you may need any
assistance. For questions or assistance, please direct
your email to [email protected], or
call 877.504.0233 toll free to speak to a service
technician.
IINSPECTION OR REPAIRS
If this Product needs to be inspected or repaired,
please call for a Return Merchandise Authorization
(RMA). Pack the Product securely using a shipping
carton. Please note that original boxes may be
included, but are not designed to withstand the rigors
of shipping without additional protection. Ship via a
carrier that provides tracking and insurance for lost or
damaged parcels, as Horizon is not responsible for
merchandise until it arrives and is accepted at our
facility. A Service Repair Request is available at
www.horizonhobby.com on the “Support” tab. If you do
not have internet access, please include a letter with
your complete name, street address, email address
and phone number where you can be reached during
business days, your RMA number, a list of the
included items, method of payment for any non-
warranty expenses and a brief summary of the
problem. Your original sales receipt must also be
included for warranty consideration. Be sure your
name, address, and RMA number are clearly written
on the outside of the shipping carton.
WARRANTY INSPECTION AND REPAIRS
To receive warranty service, you must include your
original sales receipt verifying the proof-of-purchase
date. Provided warranty conditions have been met,
your Product will be repaired or replaced free of
charge. Repair or replacement decisions are at the
sole discretion of Horizon Hobby.