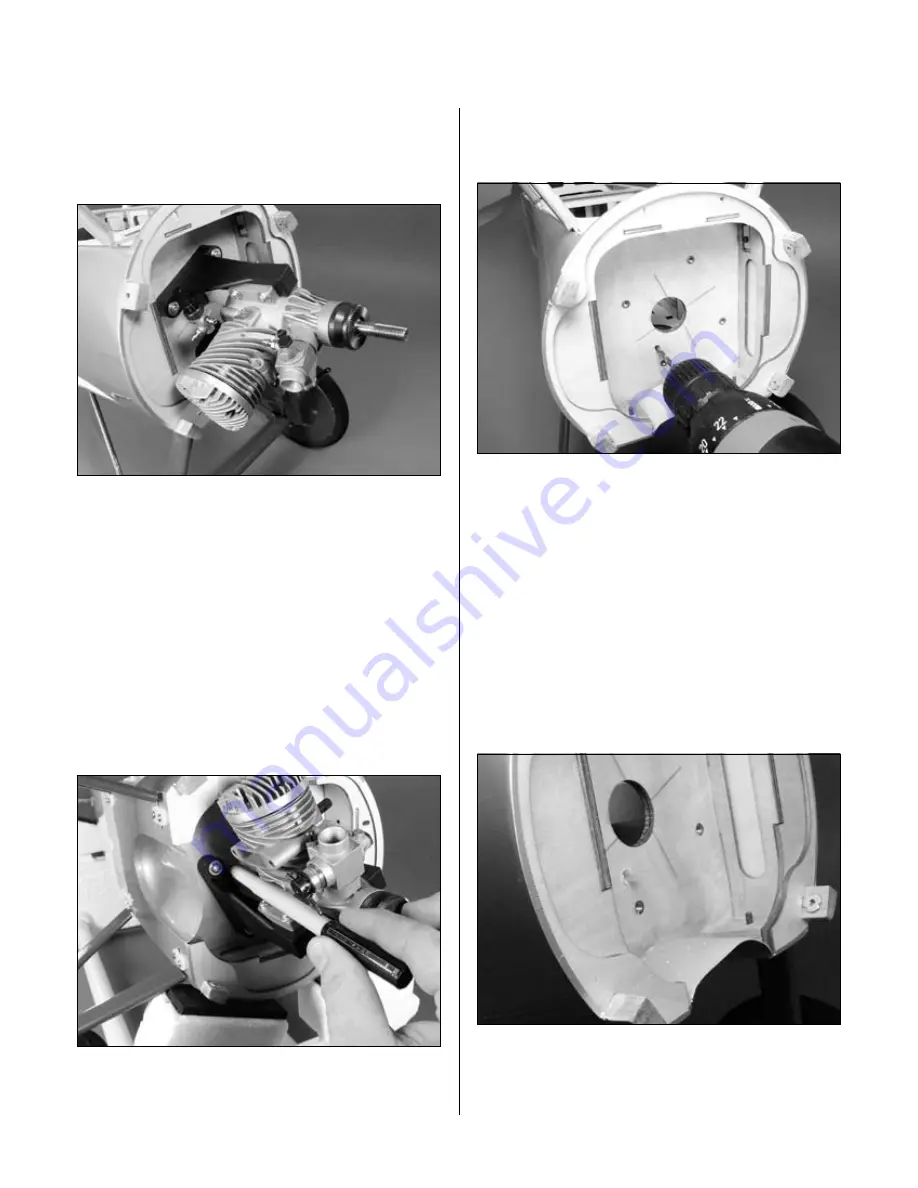
14
.
Step 4
Attach.the.engine.to.the.engine.mount.using.four..
8-32.x.1
.
1
/
4
".machine.screws,.four.8-32.lock.nuts.and.
eight.#8.washers.
Hint
:.If.you.are.having.trouble.getting.to.the.
screws,.remove.the.mount.from.the.firewall.
and.install.the.screws.holding.the.engine..
Reattach.the.mount.back.onto.the.firewall.once.
the.engine.is.secure..This.is.also.helpful.with.
the.Evolution..61.as.the.needle.valve.will.need.
to.be.removed.to.access.the.left.rear.screw.
.
Step 5
Use.a.felt-tipped.pen.to.mark.the.firewall.in.the.area.that.
will.allow.the.throttle.pushrod.line.up.with.the.carburetor.
throttle.arm.
.
Step 6
Use.a.drill.and.5/32".(4mm).drill.bit.to.drill.the.location.
for.the.throttle.pushrod.tube.
Hint
:.You.may.have.to.remove.the.engine.
from.the.firewall.as.shown..Even.better.
is.to.have.an.extended.length.drill.bit.
that.can.reach.back.to.the.firewall.
.
Step 7
Roughen.the.throttle.pushrod.tube.using.medium.grit.
sandpaper..Wipe.the.tube.down.using.rubbing.alcohol.
and.a.paper.towel.to.remove.any.oils.from.the.tube..Slide.
the.tube.into.the.hole.in.the.firewall,.leaving.about.1/2".
(13mm).protruding.from.the.firewall..Use.medium.CA.to.
glue.the.tube.to.the.firewall.
Section 3A: Engine Installation
Summary of Contents for sopwith camel 60 arf
Page 49: ...49 Notes ...