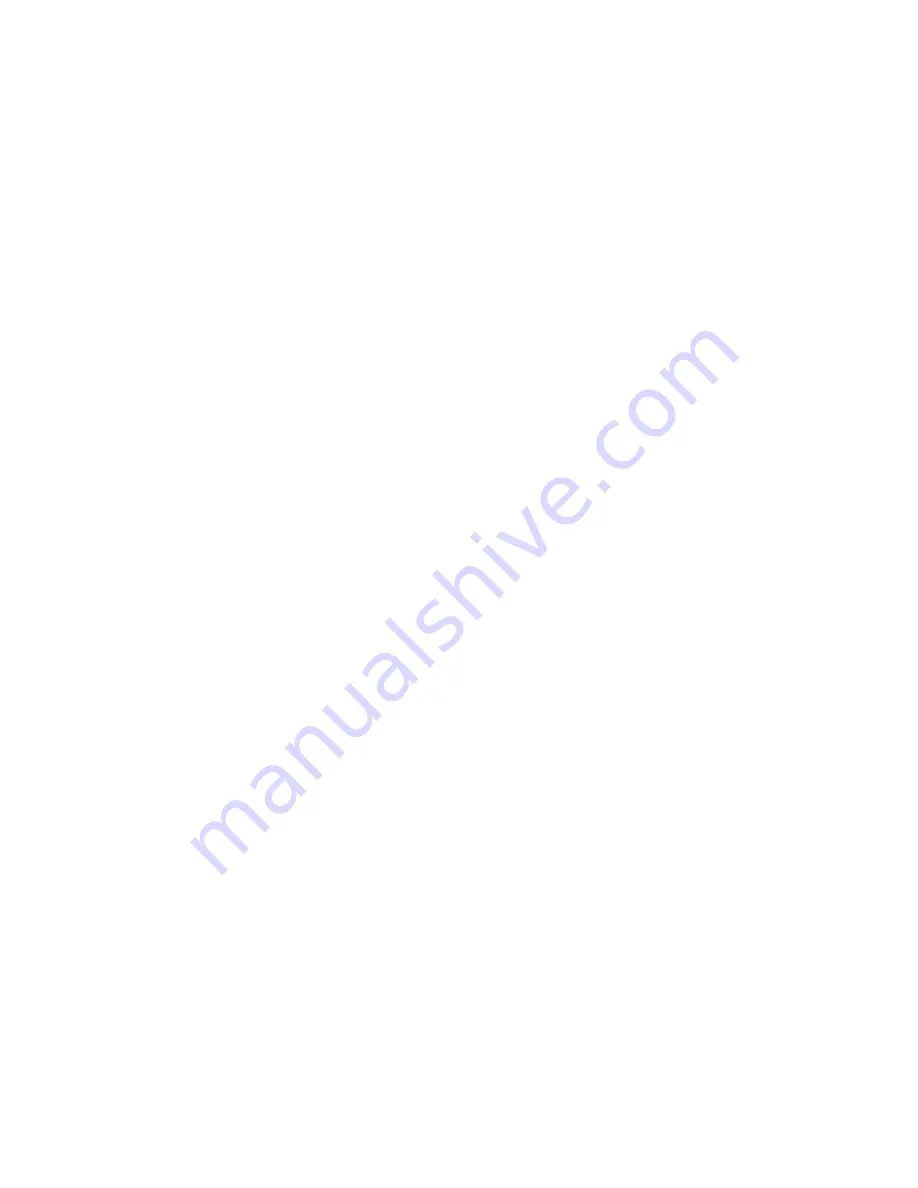
24
Q U A L I T Y C O N T R O L
In any types of welding operation, whether it is pots and pans or airplanes, the manufacturer is
interested in obtaining a quality of weld consistent with his product.
The machine, after all, is a machine. It cannot think. The machine control has the responsibility
of producing identical timing, current and pressure on each weld. However, the same problem must be
presented to the machine on each weld. Some of these include, material thickness, cleanliness, of the
part fit-up. Other problems are the maintenance of electrode contour, electrode material, proper water flow
and water temperature and material cleaning. These are the responsibility of the Quality Control
Department.
It is also the responsibility of Quality Control to establish the machine settings for each material
combination to be welded, and check the machines to see that the operators maintain these settings.
FLATNESS
Formed parts, when assembled, must be in contact in those areas to be spot welded. This spot
welding machine is not a forming machine. If a portion of the machine pressure is utilized to bring the
parts into intimate contact, then there will be a sufficient pressure to contain a molten metal. The expulsion
will result. Inadequate forging pressure after welding may lead to cracking problems.
SPOT SPACING
If spots are located too close to each other, a large portion of the welding current to produce the
second or subsequent spots will shunt through the spot or spot already made. This will result in the
formation of a small nugget or no nugget at all. The single good weld and subsequent poor welds may not
be strong enough to support the load for which the structure was designed.
CLEANLINESS CONSIDERATIONS
In resistance welding any metallic material or alloy, in the presence of foreign matter on the surface,
such as oxides, oil, grease, paint and dirt, It is a source of difficulty due to the high resistance of such
material to the passage of an electrical current. The need for cleanliness before attempting to weld cannot
be over emphasized.
All metals oxidize in air. The oxide film so formed has high unit electrical resistance, but the total
resistance of an oxide film is largely dependent on it’s thickness. Chemical pickling will be found to be the
most satisfactory method of removing oxides. This is particularly true of aluminum, where the resistance
of the oxide varies across the sheet. On steel, the oxide would be in the form of rust, which should be
removed before welding, if best welding conditions are to be maintained after sheering a weld, a round spot
will be seen if the material was clean when welded. If the edges of the spot are ragged or star shaped, it
indicates that the material was not cleaned.