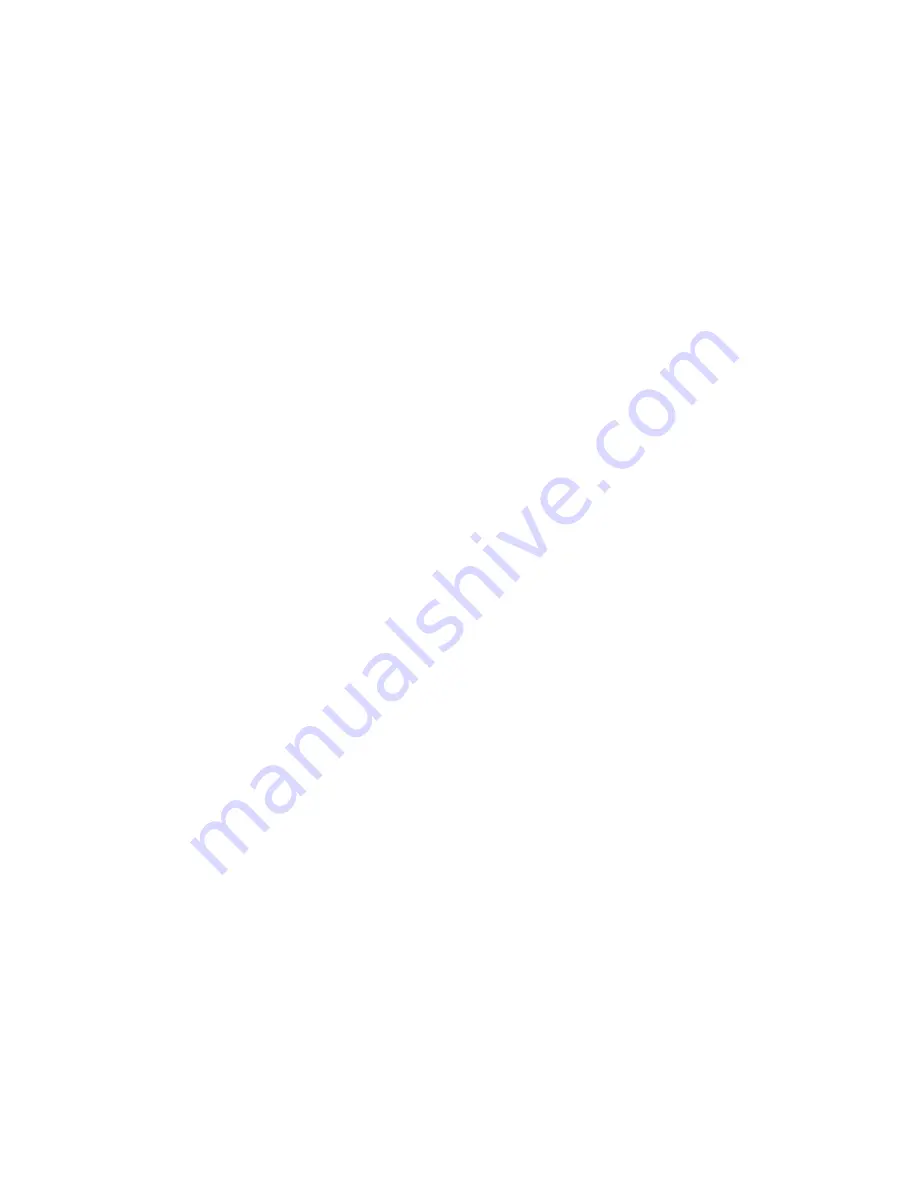
18
machine is equipped with an in-line cylinder that moves an electrode up and down through a ram. This
type of welder has the advantage that the electrodes are always in line providing fewer misalignment
problems as the electrodes wear.
HEAT PATTERN
An ideal welding condition is obtained when all of the resistance is concentrated at only one point;
the faying area clamped by the electrodes. However, in a typical weld situation there are several series
resistances.
1. Upper electrode.
2. Contact between upper electrode and upper sheet.
3. Upper sheet.
4. Contact surfaces between upper and lower sheets.
5. Lower sheet.
6. Contact between lower sheet and lower electrode.
7. Lower electrode.
DESCRIPTION OF WELD RESISTANCE
In the typical heat pattern, the heat should be concentrated at point 4, our highest level of resistance.
The next highest level of resistance is a points 2 and 6. The heat level at these points should rise slower
that at pint 4. One heat at 2 and 6 is dissipated by the electrodes and cooling water of 1 and 7, while the
heat at point 4 is trapped. Therefore, as the weld goes on, we can expect the rate of temperature rise to be
much greater at point 4, than any other points.
In an ideal weld, the weld temperature will be reached in an instant at the clamped faying surfaces and then
grow into a nugget as the weld time progresses.
CONTACTING SURFACES
Contacting surfaces consist of the electrodes and the material being welded. To reduce the
resistance at the electrode tips, both the electrode and the material must be reasonably clean. Dirt or scale
at the material to electrode surface, can cause spitting, burning and pitting of the electrode at loss of heat at
the nugget area.
In addition to reducing the resistance at electrode tips in between the contacting metal surfaces,
electrode force also forms a pressure vessel to contain the weld nugget. Since we are trying to concentrate
the greatest resistance between the two contacting metal surfaces, it might seem that electrode force could
work against a correct weld. However, since the electrodes are usually softer than the metals being welded,
better contact is made at the tip points than between the surfaces being welded. Additionally, while the
scale can increase the resistance between the sheets being welded, if the scale and dirt are absorbed into the
weld, it will usually be weakened. Scale and dirt also make it difficult to control the weld parameters.
TIME
Correct time in a weld is important to enable the weld to reach the correct temperature and to grow
the desired size. We can view current as being the main factor in how pliable the weld can be made and
time as assuring that the weld nugget will be the current size. Both, too short and too long heat times will
cause weld problems.