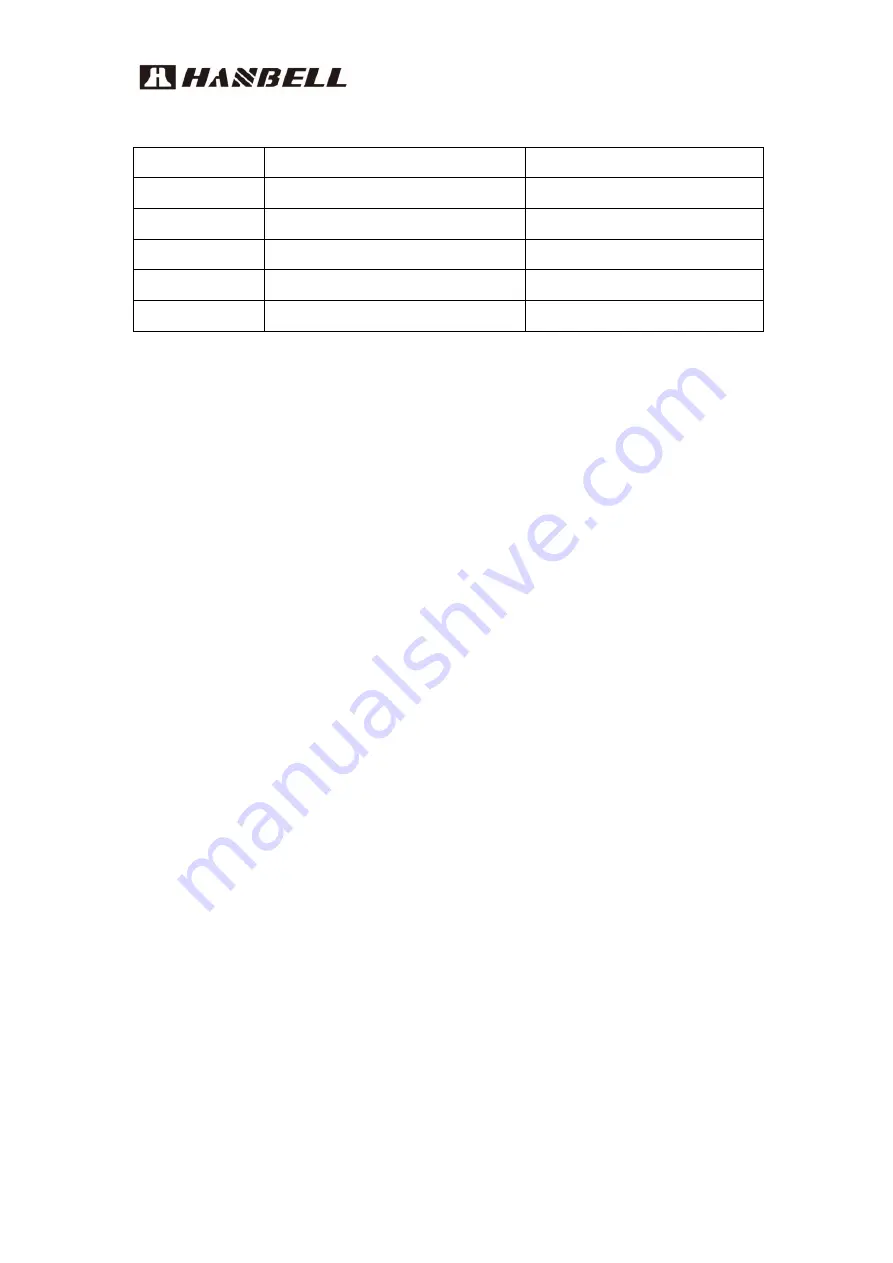
LT-S-(L) Technical manual
Model
Start current LRA
(△
start/Y start
)
Max. operation current MCC
(
A
)
LT-S-20/10-L
880/294
140
LT-S-45/20-L
1675/558
260
LT-S-55/25-L
1675/558
310
LT-S-65/32-L
2625/875
365
LT-S-83/41-L
2625/875
465
Table 6-1. MCC&LRA
1)
Above data is based on 380V, 50Hz power supply.
2)
The
LRA&MCC data above has nothing to do with the refrigerant or working
condition.