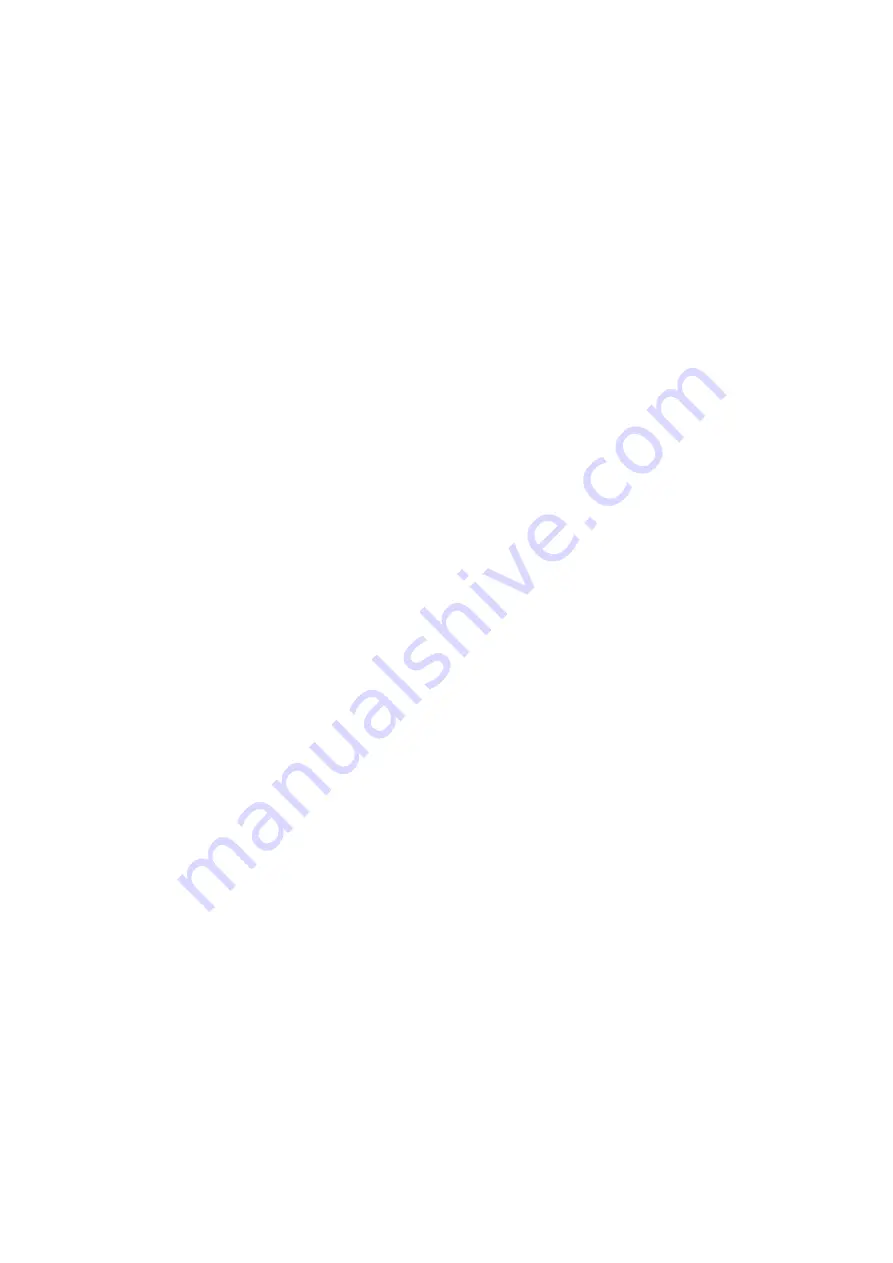
43
In addition to the pre-start checking given in the above table, please also consider the following:
a. It is necessary to pay more attention to the auxiliary facilities while the chiller is commissioning at the job-site and the periodic
maintenance after the initial start-up.
b. In order to keep the capacity control smoothly under the low ambient temperature with the normal viscosity of oil, oil heater
should be kept energizing after compressor has been shut down for preparation for the next start-up.
c. Check that all the settings on each pressure switch are correct to maintain the normal pressure in operation.
d. Check if all the stop valves in the system are already open. Operation of valve should avoid the sparks, the recommended speed
does not exceed 1m/s.
e. Check the rotating direction of the compressor by starting the compressor for a split second (approx. 0.5…1 sec.) and check the
suction and discharge pressure gauges. The correct rotating direction is: suction pressure drops immediately and the discharge
pressure will go up.
f. Compressor’s lubrication oil should be checked immediately after starting. Oil level should be within sight glass range or higher
than the middle line of oil level sight glass.
Although the PTC could protect abnormal failure caused by high temperature, but the
oil level sensor should be connected with circuit to prevent the failure from the lose of oil.
g. Oil foaming can be generated during starting phase, but it should reduce when the compressor is under stable operating
conditions. Otherwise this can indicate excessive liquid in the suction gas.
h. The running condition of compressor after commissioning at the job-site should be adjusted as; the discharge temperature will be
at least 20K above the saturated condensing temperature and the suction vapor superheat should be within 10K to the saturated
evaporating temperature.
i. The whole plant, especially the pipelines and capillary tubes must be checked for abnormal vibrations. Please contact HANBELL
or local distributor if any abnormal vibrations or noise found while compressor is running.
j. Regularly check the plant according to national regulations and the following items should also be checked:
●
Operating data of the machine
●
Check the lubrication/ oil level
●
All compressor protection devices
●
Check electrical cable connections and tightness
k. Before charging the refrigerant, please pump out the system to remove the air and moisture from the system. Moisture in the
refrigerant of an operating system can freeze-up and cause failures in the expansion valve or cap tube. Also, water chemically
reacts with the refrigerant to form acids which can corrode and/or form deposits in critical areas of the system.
l.If the new compressor has been kept in the stock for a long time, we suggest to fuel 1~1.5L into the motor casing before
starting-up in order to avoid the insufficient lubrication of rotors.
m.Suction filter should not be dismantled when piping in order to prevent welding foreign materials from dropping into the
compressor.
n. Vacuum procedures:
●
Be sure to tighten the connectors on the compressor.
●
The hose connected to a low pressure angle valve.
●
Start vacuum pump to a vacuum of 750mm-Hg.(about 30min)
●
Close the vacuum pump and remove the hose.
●
The hose connected to the high-pressure angle valve.
●
Filling nitrogen 0.5kgf.
●
Remove the hose.
Summary of Contents for ExP Series
Page 1: ...1 ...
Page 6: ...6 1 4 ATEX code description II 2 G c IIB T4 II 2 G Ex d IIB T4 Gb ...
Page 8: ...8 RC2 180 ExP A B RC2 200 ExP A ...
Page 9: ...9 RC2 200 ExP B RC2 230 ExP A B UNIT SI mm Imperial in ...
Page 10: ...10 RC2 260 ExP A B SI mm Imperial in UNIT RC2 300 ExP 320 ExP A ...
Page 11: ...11 RC2 300 ExP 320 ExP B RC2 310 ExP A B ...
Page 12: ...12 RC2 340 ExP 370 ExP A RC2 340 ExP 370 ExP B ...
Page 13: ...13 RC2 410 ExP A B RC2 470 ExP A ...
Page 14: ...14 RC2 470 ExP B RC2 510 ExP A B ...
Page 15: ...15 RC2 550 ExP A RC2 550 ExP B ...
Page 16: ...16 RC2 580 ExP A B RC2 620 ExP A B ...
Page 17: ...17 RC2 710 ExP A RC2 710 ExP B ...
Page 18: ...18 RC2 790 ExP A RC2 790 ExP B SI mm Imperial in UNIT ...
Page 19: ...19 RC2 830 ExP A RC2 830 ExP B ...