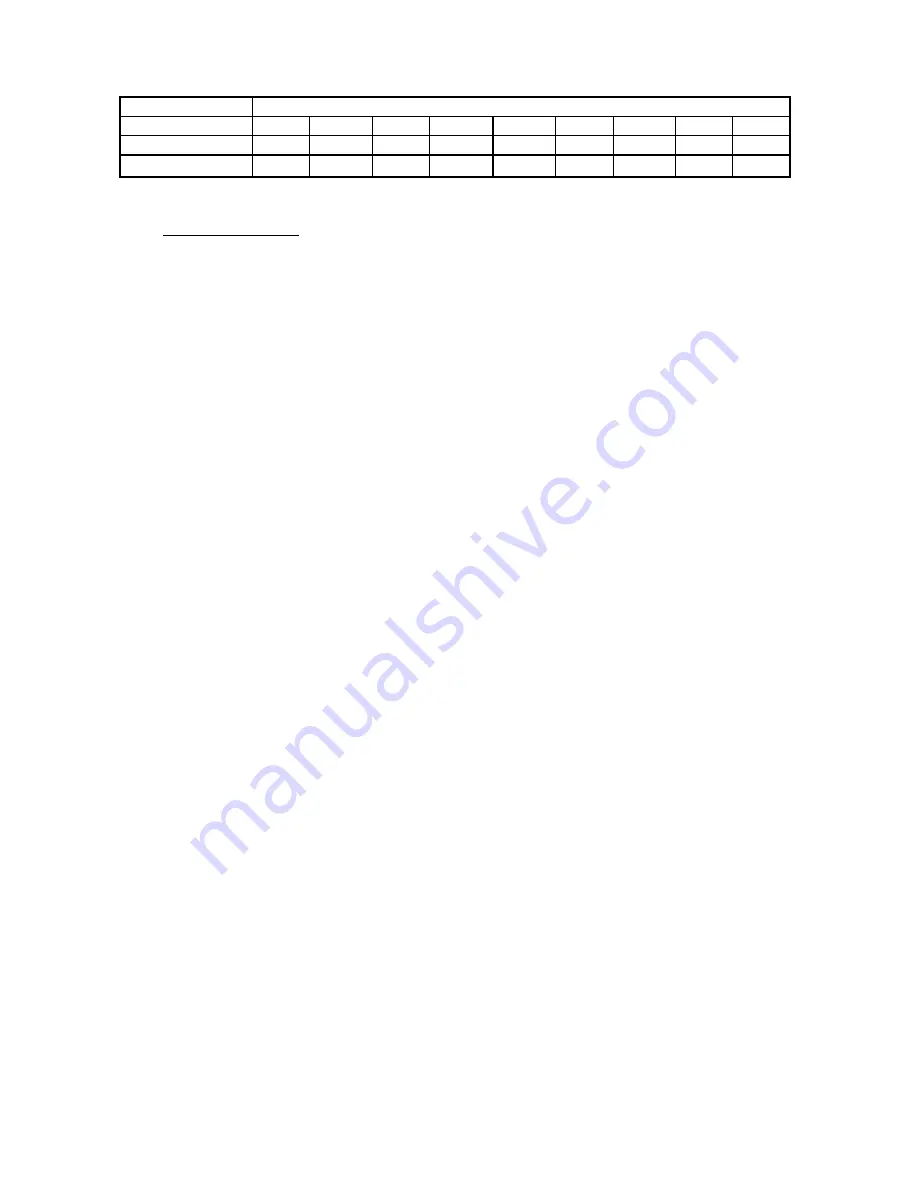
HAMWORTHY HEATING LTD
LILLIPUT HE
500001047/F
10
ensure they remain in position.
e.
Remove the two reducing plugs - located at
the top and bottom of the front section.
f.
Fit the boiler assembly tools* - one through
the flow (top) connection and the other
through the return (bottom) connection and
evenly compress the sections together.
g.
Fit the four tie rods, tighten the tie rod nuts to
a torque of 35 Nm (26 lbf.ft), and then
carefully remove the two assembly tools.
Replace the two reducing plugs in the front
section and fit the thermostat pocket and
drain valve in the top and bottom plugs
respectively. Slide the stainless steel baffle
plate into the roof of the combustion chamber
(see item 24 Fig 4) locating the returned
edges between the section fins.
h.
Fit the front door and rear combustion
chamber plate, together with ceramic
insulation, and secure with the nuts provided.
N.B.
The front boiler door may be hinged on either
left or right side, as required.
i.
Fit flue box to rear section and secure using
the screws provided.
j.
On completion of assembly, the heat
exchanger should be hydraulically pressure
tested to 1.5 times the maximum system
pressure operating for 30 minutes (BS779 -
1989, Amendment 1 - 1993).
•
Boiler assembly tools are available on loan,
from Hamworthy Heating Ltd.
6. BOILER
ASSEMBLY
6.1 Boiler
Sections
The heat exchanger is made up from THREE or
FOUR different types of section, each weighing
around 32kg (70 lb), as follows:
•
One rear section (R)
•
One front section (F)
•
Intermediate sections (I)
•
Special intermediate sections (SI)
For the purposes of identification the 'Intermediate'
sections have a joint face between the middle and
upper part of the section, whereas the 'Special
intermediate' sections do not.
These sections MUST be assembled in the correct
sequence working from the rear of the boiler as
detailed in table 4 above.
6.2 Assembly
Procedure
If it has been necessary to dismantle the boiler for
any reason, the following procedure should be
adopted to re-assemble it:
a.
Position the rear section and thoroughly clean
the nipple seatings (at both top and bottom of
the section) and the mastic rope groove
around the perimeter of the section.
b.
Taking two new nipples, smear them with
suitable nipple sealant and insert them into
their seatings - ensuring that they are at right
angles to the face of the section. Fit new
mastic rope into the groove around the
section.
Should the mastic rope break during this operation
the two ends must be overlapped and pressed
together to avoid the possibility of leakage.
c.
Taking an intermediate section, thoroughly
clean the four nipple seatings and the mastic
rope grooves, and then carefully fit it to the
rear section - locating the two nipples into
their corresponding seatings.
d.
Repeat this operation for each of the
remaining intermediate, special intermediate,
and front section, using new nipples and
mastic rope at each joint. The intermediate
sections may need support on chocks to
BOILER
SECTION TYPE
LILLIPUT HE 65
R
I
I
I
I
SI
F
LILLIPUT HE 90
R
I
I
I
I
SI
SI
SI
F
No. FROM REAR
1
2
3
4
5
6
7
8
9
TABLE 4.Composition of Sections within Heat Exchanger