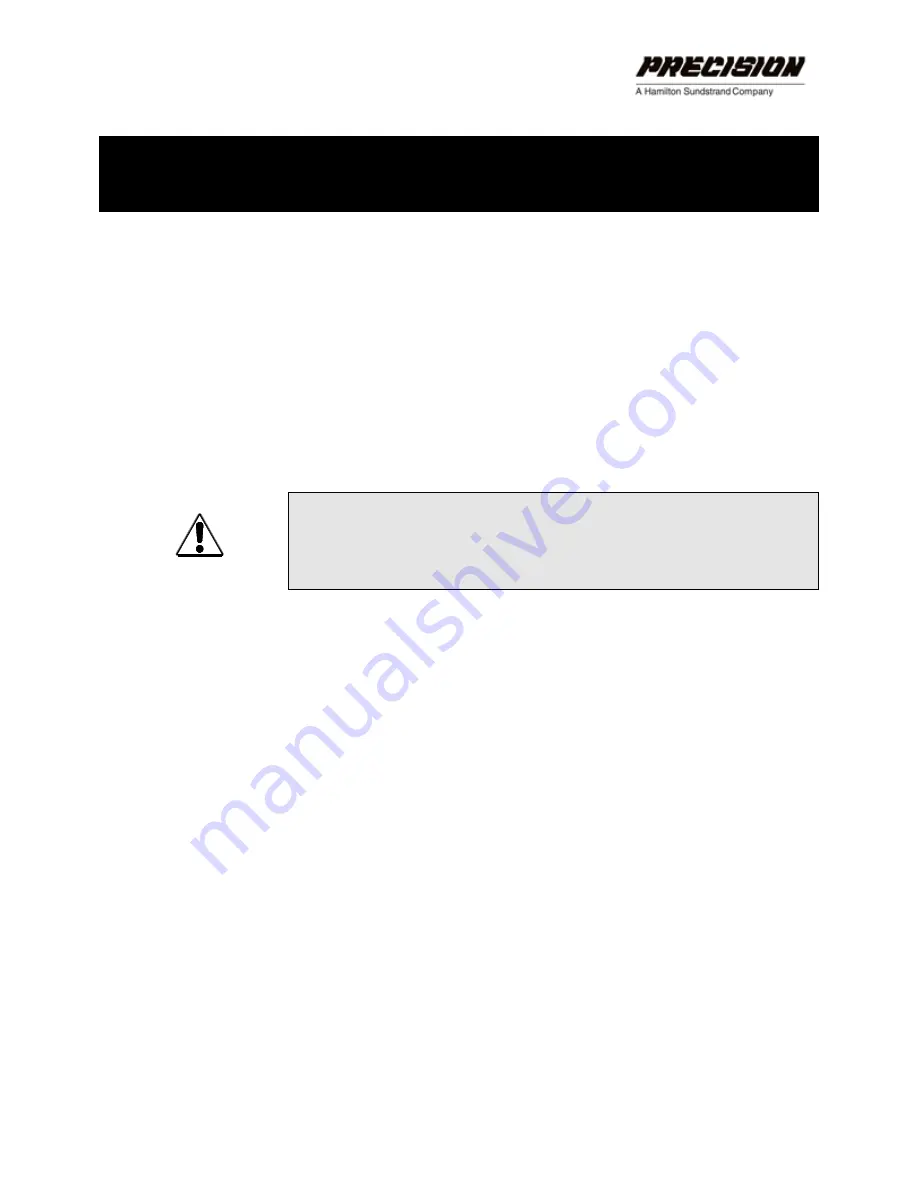
5 TROUBLESHOOTING
This section provides troubleshooting information for the ACT2000. You
can isolate most electrical faults by using an external oscilloscope and
digital voltmeter (DVM).
The ACT2000 is comprised of highly reliable components and should not
develop service problems under normal operating conditions. However,
whoever is responsible for fault analysis should be thoroughly acquainted
with physical and electrical configurations, Theory of Operation
(Section 2), and Installation (Section 1).
Resolve problems noted during operation or maintenance as soon as
possible. The causes of many problems can be traced through the
information contained in the block diagram shown in Section 2.
CAUTION
Continuing to operate the actuator in a malfunctioning condition is
hazardous to personnel and can cause property damage.
Tables 5-1 and 5-2 list common failures that can occur before or after
actuator installation, respectively.
In addition, the ACT2000 has on-board troubleshooting capability. The
ActWiz software has a fault file that you can upload to pinpoint a failure
cause. See the ActWiz Software Manual for more details.
If, after following the troubleshooting procedures, you still can’t find the
cause of the problem and repair it, contact the factory for assistance.
CH. 4: TROUBLESHOOTING THE ACT2000
49
Summary of Contents for Precision ACT2000 Series
Page 13: ...Figure 1 1 ACT2000 590P Dimensions INSTALLING THE ACT2000 7...
Page 14: ...8 ACT2000 USER GUIDE Figure 1 2 ACT2000 200F Dimensions...
Page 15: ...Figure 1 3 ACT2000 590P Pin Mounting Provisions INSTALLING THE ACT2000 9...
Page 16: ...10 ACT2000 USER GUIDE Figure 1 4 ACT2000 200F Flange Mounting Provisions...
Page 29: ...Figure 2 1 ACT2000 Electronics System Block Diagram CH 2 UNDERSTANDING THE ACT2000 23...
Page 34: ...28 ACT2000 USER GUIDE Figure 2 2 ACT2000 590P Cut Away View...
Page 37: ...Figure 2 5 Typical Refurbishment Plate CH 2 UNDERSTANDING THE ACT2000 31...
Page 38: ...32 ACT2000 USER GUIDE INTENTIONALLY BLANK...
Page 41: ...Figure 3 1 ACT2000 Basic Operation Flow Chart CH 3 OPERATING THE ACT2000 35...
Page 52: ...46 ACT2000 USER GUIDE INTENTIONALLY BLANK...
Page 54: ...48 ACT2000 USER GUIDE INTENTIONALLY BLANK...
Page 60: ...54 ACT2000 USER GUIDE INTENTIONALLY BLANK...