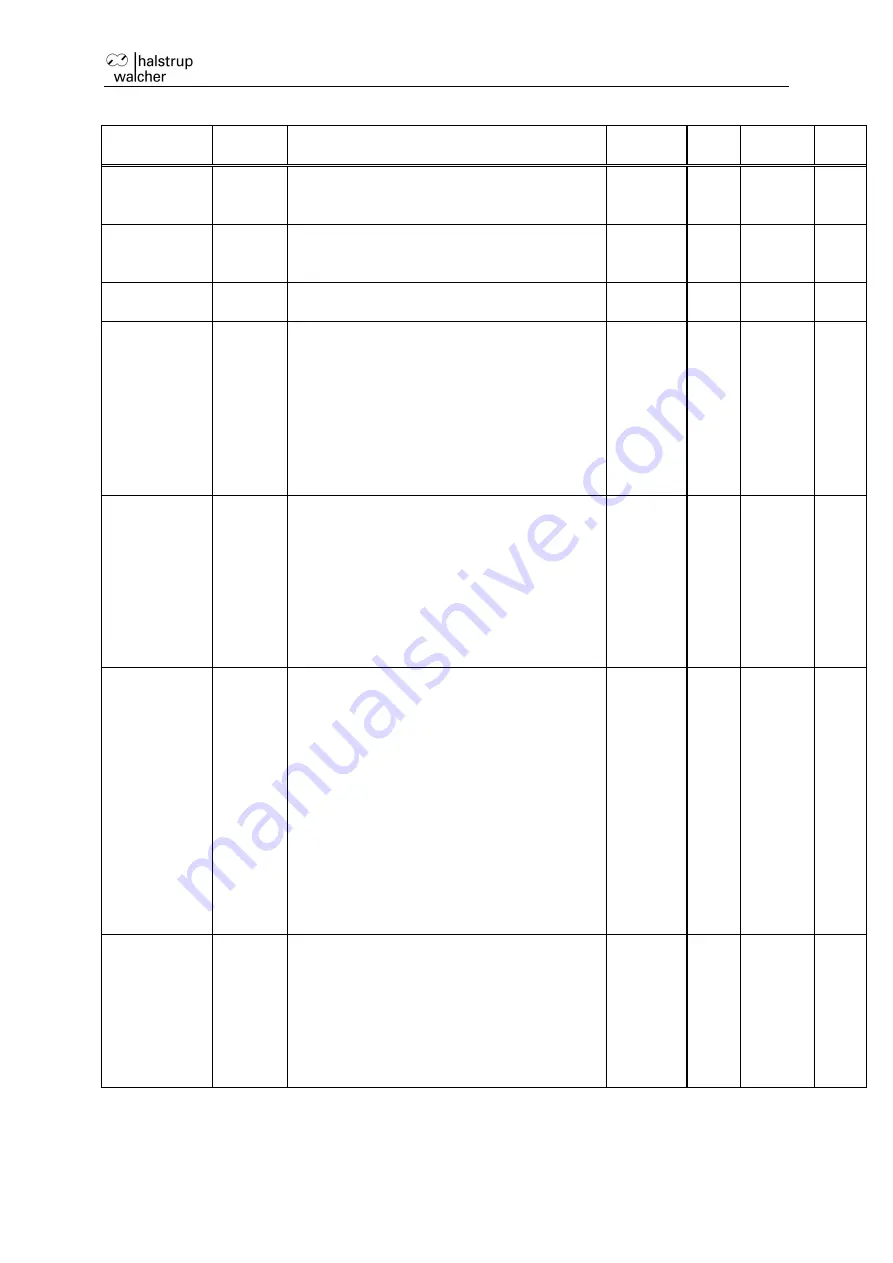
Instruction Manual HIPERDRIVE with EtherCAT
25
Name,
designation
Index
number
Function
Range of
values
Back
up?
Delivery
state
R/W
Serial
number of
the drive
209C
Serial number of the drive as string
R
Production
date of the
drive
209D
Year and week of manufacture of the
drive as string (format WW/YYYY)
R
Version of
the drive
209E
Software version number of the drive as
string (format x.xx)
R
Nominal data
of the drive
209F
Sub index 0: No. of indices (= 4)
8 bit
4
R
R
R
R
R
Sub 1:
Sub 2:
Sub 3:
Sub 4:
Nominal voltage [V]
Nominal current [A]
Nominal torque [Nm]
Nominal rated speed [r.p.m.]
The data are displayed as a string.
An “A”
preceding any value signifies that this
value must be divided by 10.
Timeout
20A0
Time for RS485 communication timeout
If the status of
the drive is at least “Ready
for operation” and no telegram is received
from the RS485 bus master within the
stated time, the drive enters the error
state. If the drive is running at that
moment, it will stop.
Specification is made in [0.1s]. Value 255
means that the monitoring is deactivated.
1… 100
or 255
16 bit
yes
20
R/W
Complete
time
20A1
RS485 message complete time [ms]
The drive considers the transmission of a
message to have been completed if no
further byte is received within the stated
period of time.
The parameter is reset automatically
during every power-up and every time the
drive is activated (SDO #20A4 from 0 to
1) with the value corresponding to the
desired baud rate (SDO #20A3).
The change to the message complete
time will only come into effect after a
reset.
16 bit
yes
R/W
Address
(drive)
20A2
RS485 address of the drive
The change of address will only come into
effect after a reset.
The address is not important for the
EtherCAT connection of the drive. Every
activation of the drive via EtherCAT sets
the address to 1.
0…253
8 bit
yes
1
R/W