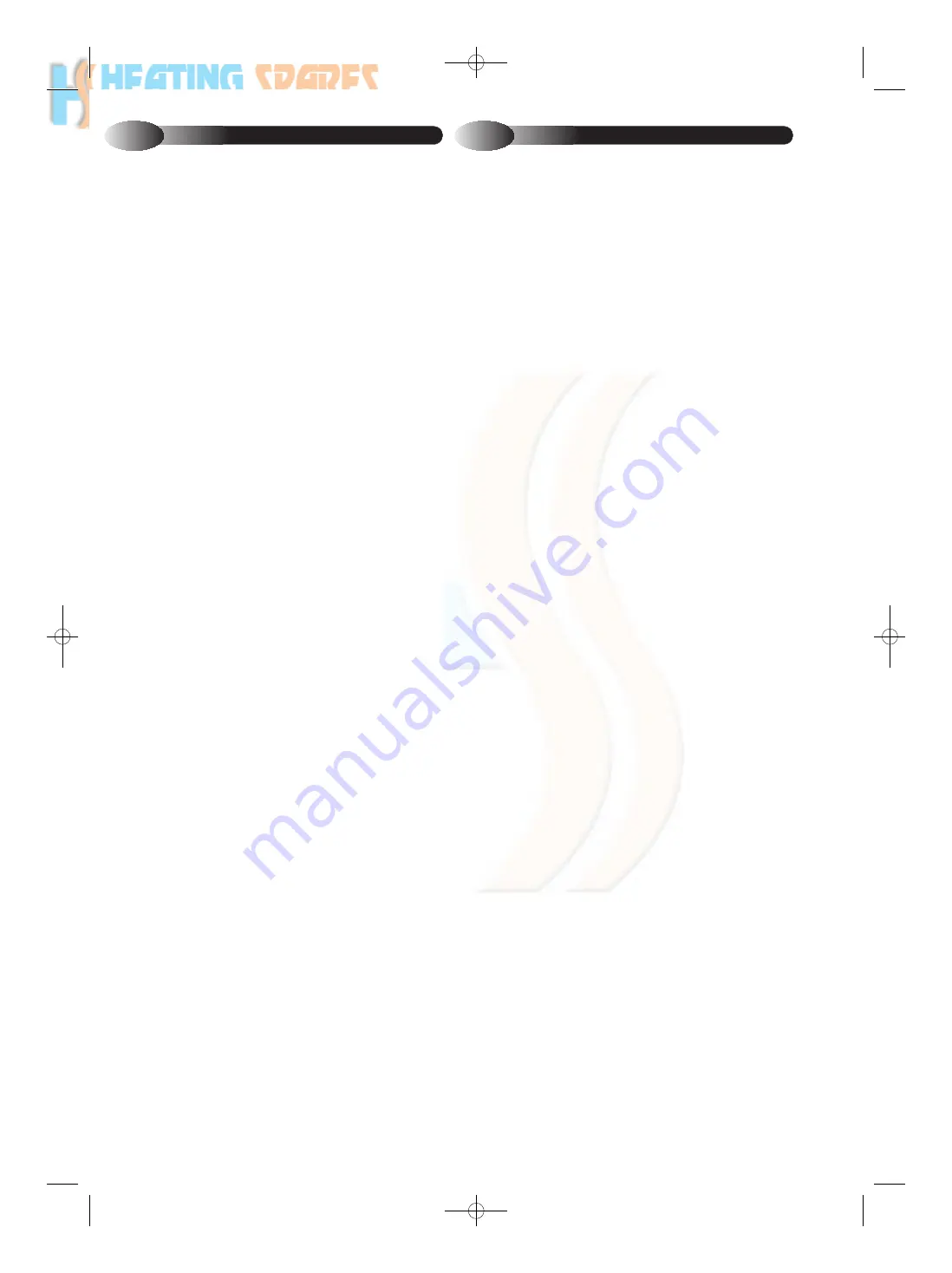
Supplied By www.heating spares.co Tel. 0161 620 6677
IT IS A STATUTORY REQUIREMENT THAT ALL GAS
APPLIANCES ARE INSTALLED BY COMPETENT PERSONS,
(i.e. CORGI REGISTERED INSTALLERS) IN ACCORDANCE
WITH THE GAS SAFETY (INSTALLATION AND USE)
REGULATIONS (CURRENT EDITION). FAILURE TO
COMPLY WITH THESE REGULATIONS MAY LEAD TO
PROSECUTION.
These appliances have been tested and certified in order to
satisfy the necessary European Directives and comply with the
latest Building Regulations, including the efficiency requirements
of the SEDBUK scheme.
Gas Appliance Directive
90/396/EEC
Efficiency of Hot Water Boilers Directive
92/42/EEC
Low Voltage Directive
93/68/EEC
Electromagnetic Compatibility Directive
92/31/EEC
No modifications to these appliances should be made unless they
are fully approved by the manufacturer.
Appliance installation must be carried out by a competent person
and must be in accordance with the current legislation in force at
the time of installation, in the country of destination.
The manufacturer’s instructions must not be taken as overriding
any statutory requirements.
GAS LEAKS. DO NOT OPERATE ANY
ELECTRICAL SWITCHES, OR USE A NAKED
FLAME. TURN OFF THE GAS SUPPLY.
VENTILATE THE AREA BY OPENING DOORS AND
WINDOWS. CALL OUT YOUR LOCAL GAS SUPPLIER
TEL: 0800 111 999.
Control of Substances Hazardous to Health
Under Section 6 of the Health and Safety at Work Act 1974, it is
required to provide information on substances hazardous to health.
The adhesives and sealants used in this appliance are cured and
give no known hazard in this state.
Insulation Pads – These can cause irritation to skin, eye and the
respiratory tract. If you have a history of skin complaint you may be
susceptible to irritation. High dust levels are usual only if the
material is broken. Normal handling should not cause discomfort,
but follow normal good hygiene and wash your hands before
eating, drinking or going to the lavatory. If you do suffer irritation to
the eyes or severe irritation to the skin seek medical attention.
Gas and Electricity Consumer Council (Energywatch)
Energywatch is an independent organisation, which protects the
interests of gas users. If you need advice concerning energy
issues, they may be contacted on their consumer help line
number: 08459 060708, or via their web site;
http://www.energywatch.org.uk.
The appliances incorporate a microprocessor based, fully
modulating air/gas ratio control system with direct burner
ignition, which provides a modulated heat output to either central
heating (CH) or domestic hot water (DHW) demands, and with
internal frost protection provided as standard. The heat exchanger
is constructed from stainless steel encased in high temperature
polymer.
A combined circulating pump, diverter valve and automatic air
vent assembly, pressure gauge, safety valve and system
expansion vessel are included. Isolation valves are fitted to the
service connections. The appliances have a DHW flow detection
device, which gives priority to DHW demand and proportions the
required heating load to the DHW flow rate, an electro-
mechanical 24 hour time clock is also fitted as standard.
The appliances may be used with any certified mains voltage
room thermostat, and can operate without the need for an
automatic bypass valve, however if thermostatic radiator valves
are installed it is recommended that one radiator is fitted with
lockshield valves, to allow the pump overrun facility to operate
correctly. A separate CH expansion vessel is not required if the
total CH system content is less than 84 litres, but one is required
for systems with volumes greater than 84 litres; refer to section
3.7. A separate DHW expansion vessel is not required.
It is recommended that a drain cock is fitted at the lowest point in
the system.
1.1
IMPORTANT INFORMATION
1.2
GENERAL DESCRIPTION
!
1
751094 ACE HE INST MANUAL:751094 ACE HE 28/9/10 09:44 Page 3