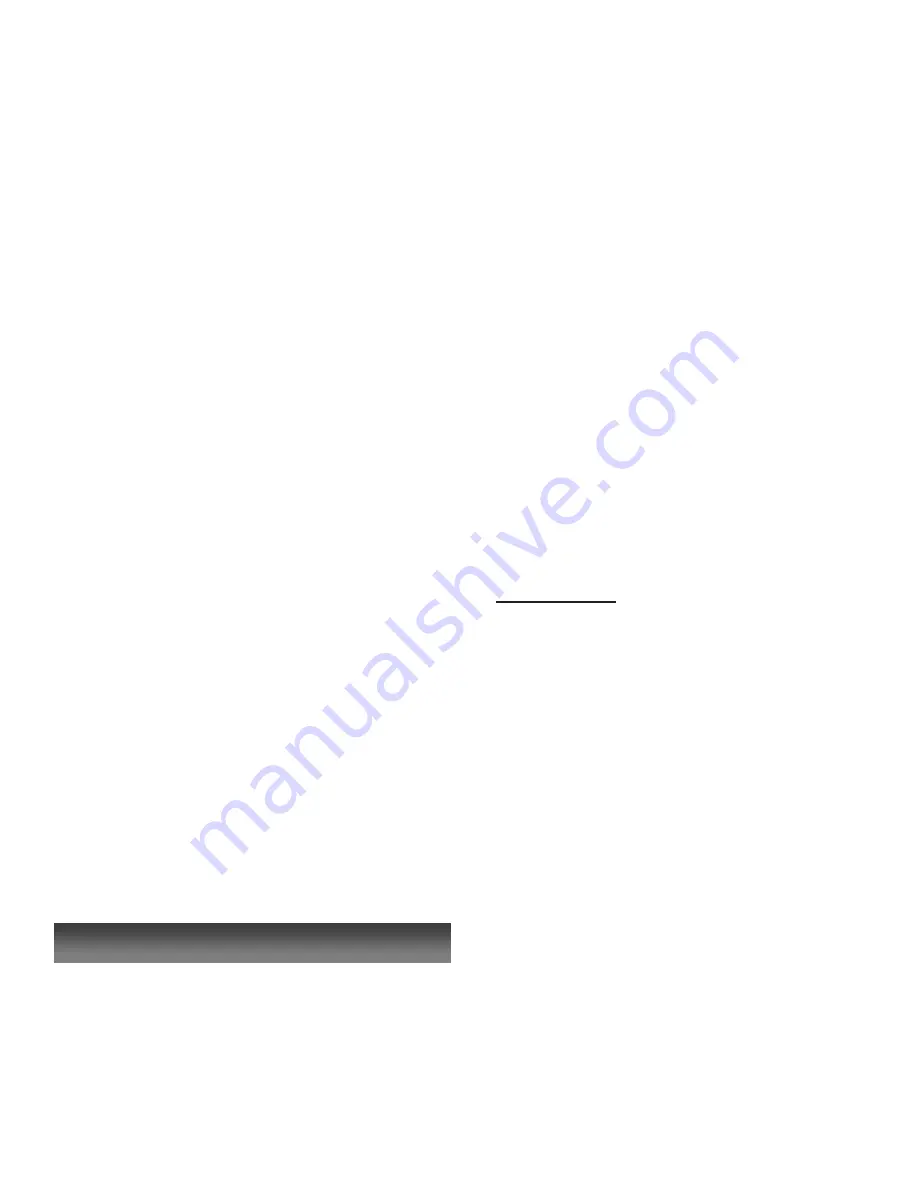
1/17
9.
To reduce the potential for fouling, implement the
following policies and procedures
:
1. Test cycle the actuator system at least once per
month when in service.
2. Specify that the chlorine
supplier provide only
cylinders or ton containers equipped with
Chlorine Institute approved Teflon valve packing.
This greatly reduces friction between the
packing and stem. In the past, graphite-
impregnated, split packing rings were the only
approved packing system for cylinder and
container valves. These require greater gland
nut tightness to seal, resulting in higher friction
between the valve stem and packing. Friction is
increased even more when the stem is corroded
or fouled. The solid, non-split Teflon packing
seals better, with less gland pressure, and
requires less force to open or close even if the
stem is corroded. New seal kits are available for
suppliers to convert existing valves to the new
Teflon packing at nominal cost.
3. Wet chlorine is the primary cause of corrosion of
the internal components of these valves. This
may be due to poor quality control during the
refilling of containers by the supplier.
Additionally, moisture and/or other contaminants
may not be fully evacuated from the chlorine
container before refilling. Moisture can also enter
the valve and cylinder through "suck-back" from
the dispensing piping or atmosphere. This
problem is the result of temperature changes or
other design deficiencies.
4. Consult with your supplier concerning their
refilling equipment and techniques as well as
valve reconditioning and repackaging. Detailed
procedures are covered in the Chlorine Institute
(C.I.) Pamphlet # 17,
Cylinder and Ton
Container Procedure for Chlorine Packing,
to
insure high quality, dry chlorine and contaminant
free valves that turn freely and easily (less than
10 ft-lb. of torque).
5. Consider the installation of equipment that
dispenses chlorine gas with a vacuum regulator.
This can eliminate "suck-back" and the intrusion
of atmospheric moisture. Your Halogen
Valve
Systems representative can provide information
on devices engineered to dispense chlorine
while precluding the introduction of
contaminants.
A. Operational Testing
The system test sequence described in
In-
Service Testing
, (section B on page 8) should
be performed each time a tank or cylinder
change-out is done. For cylinders or ton
containers kept in extended service, this system
test should be performed at least once per
month, and preferably once a week. The battery
capacity is not appreciably affected by one or
even several test cycles of the actuator when
normal AC charging power is available.
B. Gas Detector & Emergency Shutoff Switch
Testing
If a leak detector senses chlorine gas from a leak
or from residual released during tank or cylinder
change-out and triggers the Gemini Controller to
close the chlorine valve, make sure that the room
is completely clear of chlorine gas before
resetting the Gemini Controller (RESET:
Press
and hold
TEST B
key until
BATTERY STATUS
light turns OFF, +/- 6 seconds, then release).
Otherwise, the gas sensor will still be detecting
residual chlorine in the room causing an
emergency close signal to be sent the Gemini
controller, immediately activating another
emergency close sequence.
Test Procedure
The testing or calibration of a gas leak detector,
emergency shutoff switch or any remote input to
the controller may be checked by the following
procedure. This procedure also provides a check
of the electrical continuity of the entire system.
1. Place actuators in storage brackets.
2. Expose the gas leak detector sensor to a
calibration gas, press an emergency close
switch, or activate any other input device you
wish to test.
3. After the controller receives an input signal,
each actuator should run for about 3
seconds, indicating that the controller
received the signal correctly.
4. The
Armed/Ready
lights will alternately
flash, then turn off until system is reset.
5. To reset controller, press and hold the
TEST
B
key until
BATTERY STATUS
light turns
OFF (+/- 6 seconds), then release. System
will reboot and all lights should then indicate
normally.
VII. Maintenance
Summary of Contents for Terminator
Page 16: ...For the Gemini Controller IX Typical Circuit Board Wiring 1 17 13 ...
Page 17: ...1 17 14 X Optional Relay Interface Module Circuit Board TB2 JS1 JS2 COM N O K2 K1 PIN 1 TB2 V ...
Page 19: ...1 17 16 XII Remote Input Circuit Wiring N O ...
Page 20: ...XIII Remote Input Circuit Wiring N C 1 17 17 ...
Page 21: ...1 17 18 XIV Actuator Cable Extension ...
Page 22: ...1 17 19 XV Emergency Shutoff Switch ...
Page 23: ...1 17 20 XVI Optional Auxiliary Valve Adapter ...
Page 28: ...7 17 Bulletin 800 06 ...