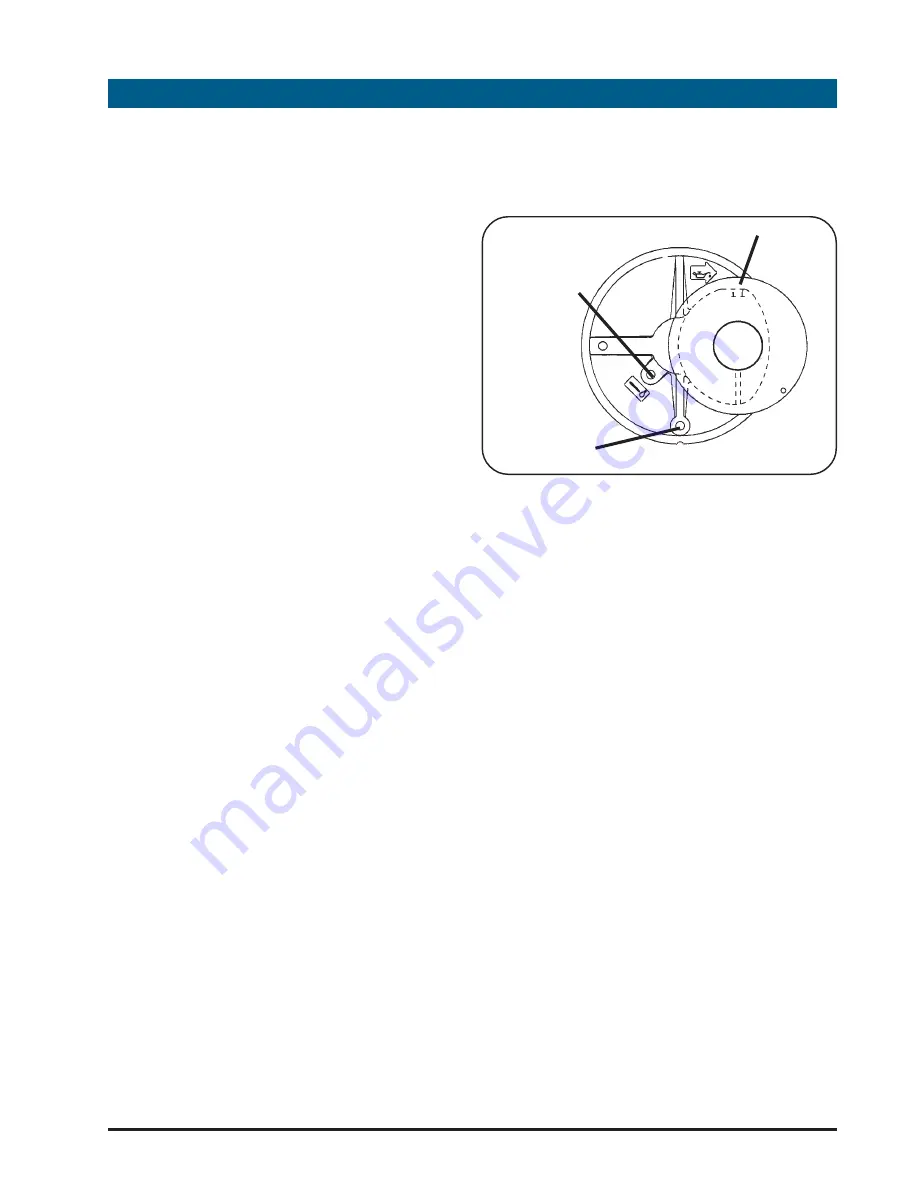
USER OPERATION AND MAINTENANCE
HP SERIES
PORTABLE PUMPS
29
The HP Series portable pumps are
designed to provide years of reliable
service with a minimum of maintenance
on the pump end. The pump must be
cleaned and flushed out after each use.
Failure to clean and flush the pump may
degrade pump performance. The only
maintenance that is usually required on
a regular basis is to hydrostatically test
the pump each year.
LEAK TEST
A leak test of the pump must be
performed each year. The leak test will
be conducted at the pump working
pressure.
WARNING: TO PREVENT
ACCIDENTAL STARTING
when
servicing the engine or pump
always disconnect the
negative wire from battery
terminal.
CHECK OIL LEVEL (HP100 GEARBOX)
The HP100 pump has a gearbox that
requires routine maintenance. The oil
should be checked in the gearbox every
eight hours of operation and after each
use of the pump. The following
procedures are used to check the oil
level in the HP100 gearbox.
1. Place pump on a level work
surface to gain access to the
gearbox.
2. Locate the oil fill fitting, the oil level
plug and the oil drain plug on the
pump gearbox.
3. Loosen oil level plug with wrench
and begin to remove slowly. If the oil
is at the proper level there should be
a slight trickle of oil from around the
plug.
4. Replace plug and tighten. If oil
needs refilling remove oil fill fitting,
vent and oil level plug. Add new
gear oil (SAE 30) through oil fill fitting
until oil starts to flow from oil level
plug. Replace and tighten oil level
plug.
8
PUMP MAINTENANCE
OIL DRAIN PLUG
OIL FILL FITTING
OIL LEVEL PLUG
Summary of Contents for HP 100
Page 2: ...HP SERIES PORTABLE PUMPS USER OPERATION AND MAINTENANCE 2...
Page 4: ...HP SERIES PORTABLE PUMPS USER OPERATION AND MAINTENANCE 4...
Page 44: ...HP SERIES PORTABLE PUMPS USER OPERATION AND MAINTENANCE 44 X Series Pump Mounting Dimensions...
Page 48: ...HP SERIES PORTABLE PUMPS USER OPERATION AND MAINTENANCE 48 I Series Pump Dimensions...
Page 72: ......