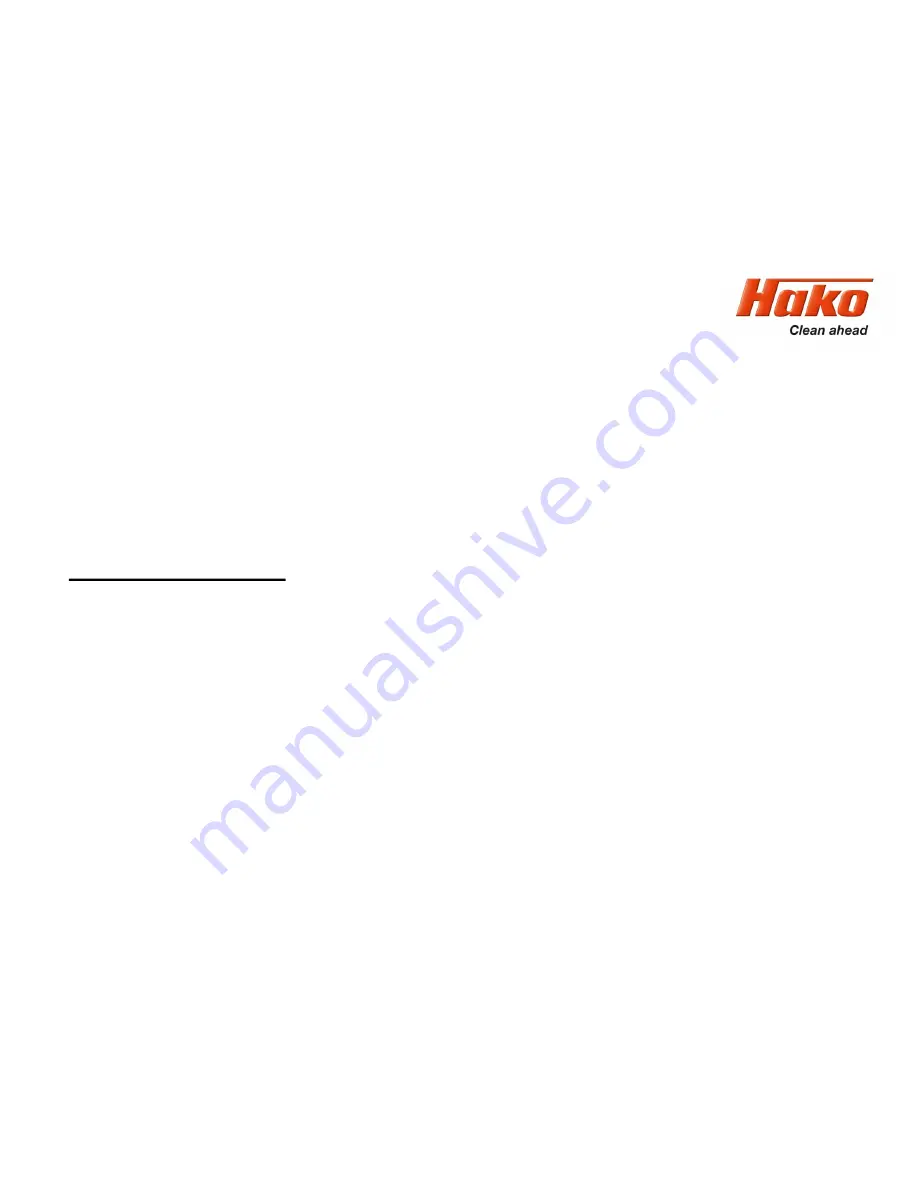
Sheet 15
With CANUSB interface PN 03501750 (**): (Alternative connecting opportunity)
Connect the D-Sub 9 connection of the diagnostics cable marked CAN1 (red
marking) to the round plug of the interface using the adapter piece (D-Sub 9 to
7-pole round plug) included in the scope of delivery of the diagnostics cable.
Flashing the software:
-
Turn on the machine.
-
Start the Hako diagnostics software. Select the “HAKO” button, then click the
“Scrubmaster B120R” button. The application independently searches for a new,
blank control unit.
-
Follow the instructions of the programme. Do not turn off the machine or
disconnect the connection before flashing has been completed.
-
Carry out the settings for operative units, options, battery and parameters via the
display according to the training documents.
2.1.2 Flashing the control unit
Summary of Contents for Scrubmaster B 120 R
Page 20: ...Sheet 20 2 2 1 Switching off vacuuming dirt water tank full P T S...
Page 30: ...Sheet 30 3 Technical data...
Page 31: ...Sheet 31 3 Technical data...
Page 32: ...Sheet 32 3 Technical data...
Page 33: ...Sheet 33 3 Technical data...
Page 34: ...Sheet 34 3 Technical data...
Page 38: ...Sheet 38 4 2 Hako system maintenance I...
Page 53: ...6 Machine settings 6 1 6 Charging characteristics of the integrated charger Sheet 53...
Page 60: ...Sheet 60 7 Mechanical components 7 1 Squeegee Fig 7 2a Fig 7 2b...
Page 62: ...Sheet 62 7 Mechanical components Height adjustment 7 1 Squeegee Figure 7 4...
Page 85: ...Sheet 85 11 Battery charger 11 1 Operating manual...
Page 86: ...Sheet 86 11 Battery charger 11 1 Operating manual...
Page 87: ...Sheet 87 11 Battery charger 11 1 Operating manual...
Page 88: ...Sheet 88 11 Battery charger 11 1 Operating manual...
Page 90: ...11 Battery charger 11 3 Charge data table Sheet 90...
Page 97: ...Sheet 97 14 Notes...
Page 98: ...Sheet 98 14 Notes...
Page 99: ...Sheet 99 14 Notes...