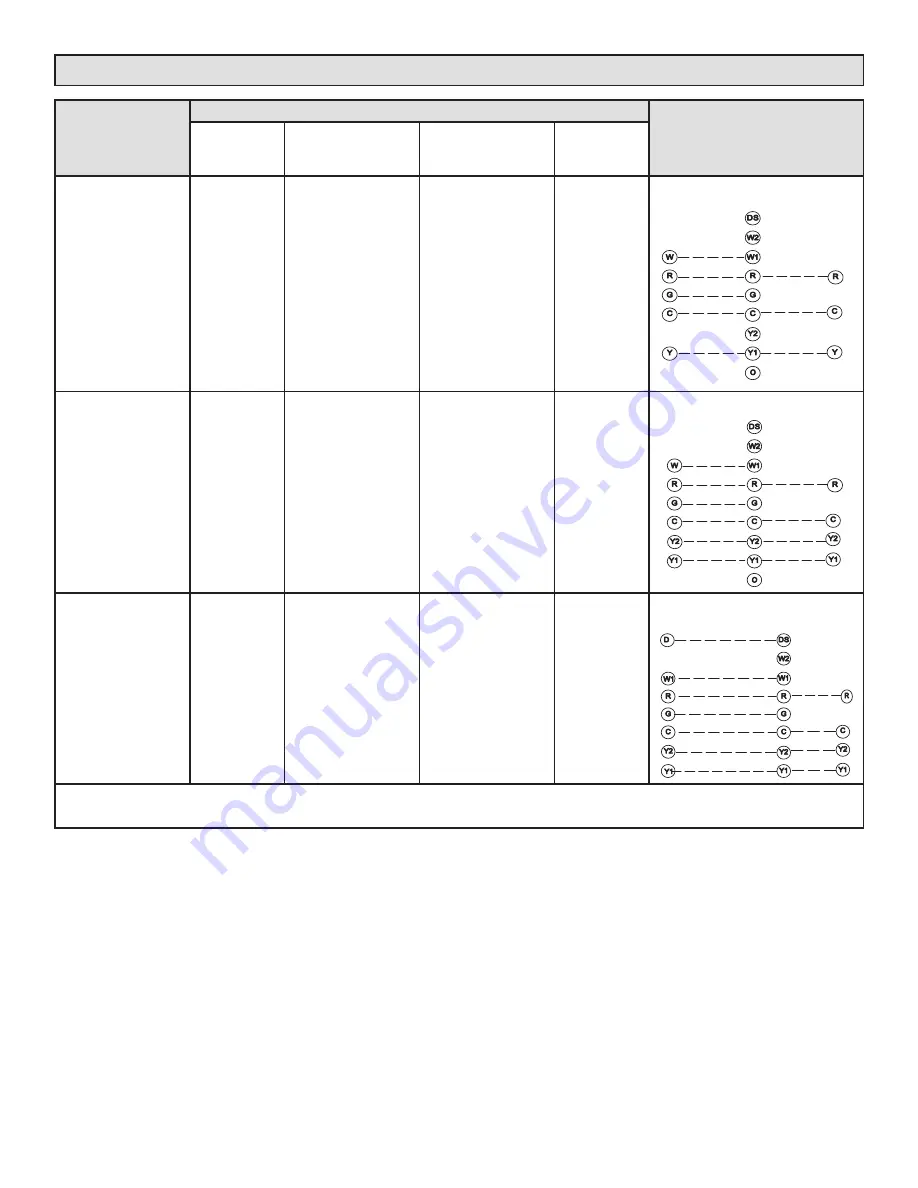
Page 61
31-5000724 Rev. 0
Field Wiring Applications with Conventional Thermostat
Thermostat
DIP Switch Settings and On-Board Links
Wiring Connections
DIP Switch 1
W915
(Y1 to Y2)
Two-Stage Cooling
W914
(DS to R)
Dehumidification
W951
(O to R)
Heat Pumps
1 Heat / 1 Cool
NOTE:
Use DIP
switch 3 to set
sceond-stage heat
ON delay.
OFF - 7 minutes
ON - 12 minutes
ON
Intact
Intact
Intact
T'STAT
CONTROL
TERM. STRIP
OUTDOOR
UNIT
*
1 Heat / 2 Cool
NOTE:
Use DIP
switch 3 to set
sceond-stage heat
ON delay.
OFF - 7 minutes
ON - 12 minutes
ON
Cut
Intact
Intact
T'STAT
CONTROL
TERM. STRIP
OUTDOOR
UNIT
*
1 Heat / 2 Cool
with t’stat with
dehumidification
mode
NOTE:
Use DIP
switch 3 to set
sceond-stage heat
ON delay.
OFF - 7 minutes
ON - 12 minutes
ON
Cut
Cut
Intact
T'STAT
CONTROL
TERM. STRIP
OUTDOOR
UNIT
*
* “R” required on some units.
** Connect W1 to W1 ONLY if using defrost tempering kit
Table 30. Field Wiring