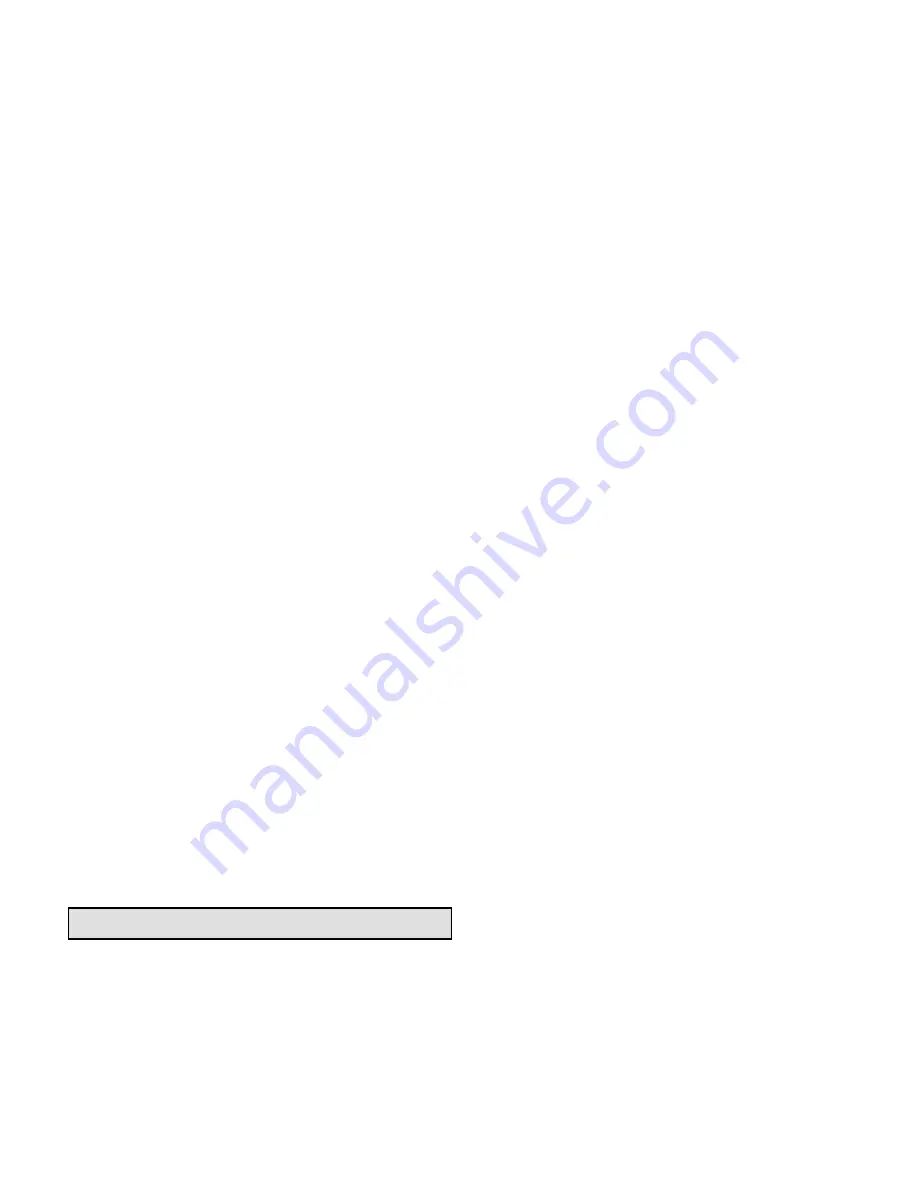
507961-01G / 31-5000653
Page 53 of 57
Issue 2128
For proper furnace operation the minimum gas supply
pressure is 4.5” w.c and the maximum gas supply pressure
is 10.5” w.c for natural gas. The minimum gas supply
pressure is 10” w.c. and the maximum gas supply pressure
is 13” w.c. for LP/propane gas.
Manifold Pressure Measurement
1. A manifold pressure post located on the gas valve
provides access to the manifold pressure. See Figure
71. Back out the 3/32 Hex screw one turn, connect a
piece of 5/16” tubing and connect to a manometer to
measure supply pressure.
2. Start unit and allow 5 minutes for unit to reach steady
state.
3. While waiting for the unit to stabilize, observe the
flame. Flame should be stable and should not lift from
burner. Natural gas should burn blue.
4. After allowing unit to stabilize for 5 minutes, record
manifold pressure and compare to value given in
NOTE:
Shut unit off and remove manometer as soon as
an accurate reading has been obtained. Take care to re-
tighten the 3/32 Hex screw.
Proper Combustion
Furnace should operate minimum 15 minutes with correct
manifold pressure and gas flow rate before checking
combustion. Take combustion sample beyond the flue
outlet and compare to the tables below. The maximum
carbon monoxide reading should not exceed 100 ppm.
High Altitude Information
NOTE:
In Canada, certification for installations at
elevations over 4500 feet (1371 m) is the jurisdiction of
local authorities.
Units may be installed at altitudes up to 4,500 ft. above
sea level without manifold adjustment. Units installed
at altitude of 4,501 - 10,000 feet (1371 to 3048 m) may
require a pressure switch change, which can be ordered
separately. Table 16 lists conversion kit and pressure
switch requirements at varying altitudes.
The combustion air pressure switch is factory-set and
requires no adjustment.
Other Unit Adjustments
Primary Limit
The primary limit is located on the heating compartment
vestibule panel. This limit is factory set and requires no
adjustment.
Flame Rollout Switches (Two)
These manually reset switches are located on the front of
the burner box.
Pressure Switches
The pressure switches are located in the heating
compartment on the cold end header box. These switches
check for proper combustion air inducer operation before
allowing ignition trial. The switches are factory set and
must not be adjusted.
Temperature Rise
After the furnace has been started and supply and return
air temperatures have been allowed to stabilize, check
the temperature rise. If necessary, adjust the blower
speed to maintain the temperature rise within the range
shown on the unit nameplate. See Table 12 for allowable
heating speeds. Increase the blower speed to decrease
the temperature. Decrease the blower speed to increase
the temperature rise. Failure to adjust the temperature rise
may cause erratic limit operation.
Fan Control
The fan ON time of 30 seconds is not adjustable. The fan
OFF delay (amount of time that the blower operates after
the heat demand has been satisfied) is 120 seconds and
is not adjustable.
Thermostat Heat Anticipation
Set the heat anticipator setting (if adjustable) according to
the amp draw listed on the wiring diagram that is attached
to the unit.
Electrical
1. Check all wiring for loose connections.
2. Check for the correct voltage at the furnace (furnace
operating).
3. Check amp–draw on the blower motor.
Motor Nameplate__________Actual__________
Electronic Ignition
The integrated control has an added feature of an internal
Watchguard control. The feature serves as an automatic
reset device for integrated control lockout caused by
ignition failure. This type of lockout is usually due to low
gas line pressure. After one hour of continuous thermostat
demand for heat, the Watchguard will break and remake
thermostat demand to the furnace and automatically reset
the integrated control to begin the ignition sequence.
Exhaust and Air Intake Pipe
1. Check exhaust and air intake connections for tightness
and to make sure there is no blockage.
2. Is pressure switch closed? Obstructed exhaust pipe
will cause unit to shut off at pressure switch. Check
termination for blockages.
3. Obstructed pipe or termination may cause rollout
switches to open. Reset manual flame rollout switches
on burner box assembly if necessary.