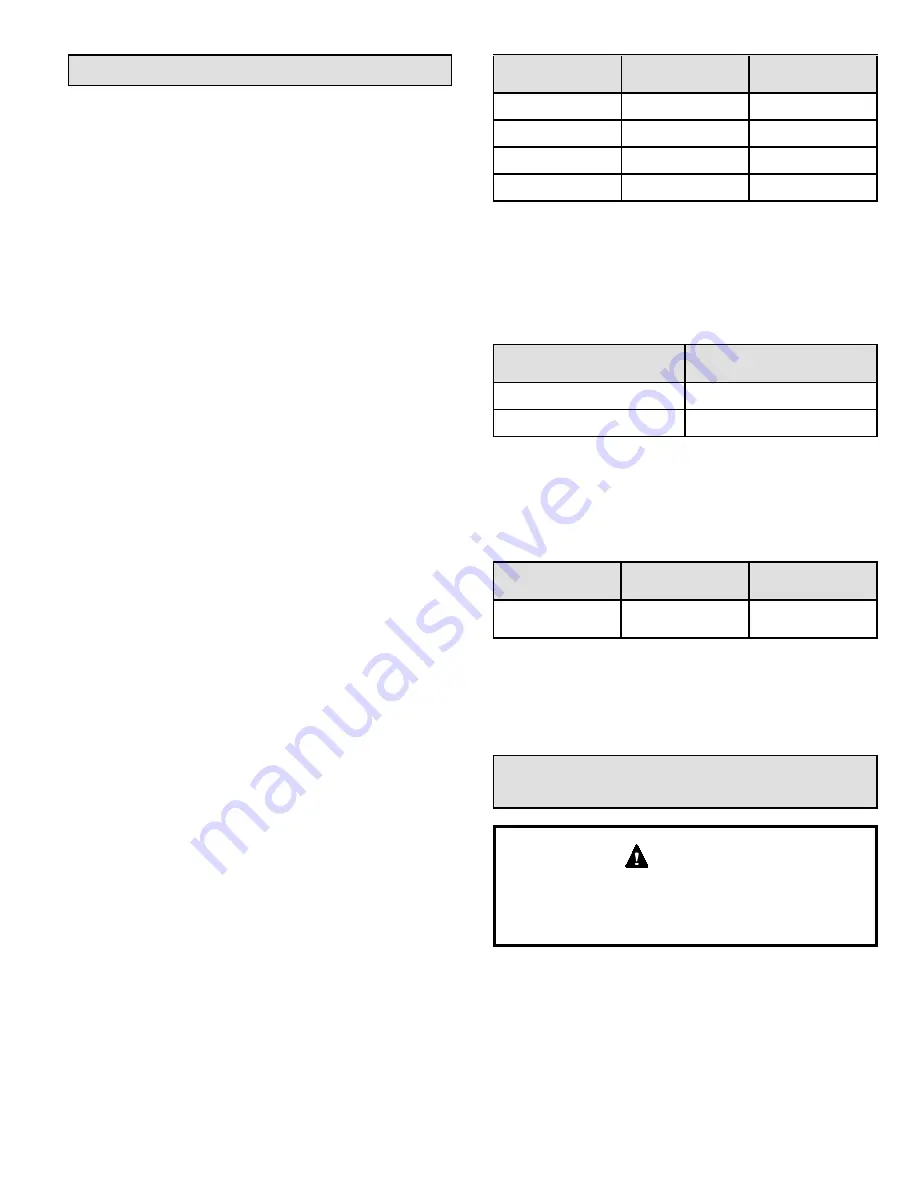
508145-01G / 31-5000660
Issue 2220
Page 29 of 38
Integrated Control DIP Switch Settings
NF80DT units are equipped with a two-stage integrated
control. This control manages ignition timing, heating
mode fan off delays and indoor blower speeds based on
selections made using the control dip switches and jumpers.
The control includes an internal watchguard feature which
automatically resets the ignition control when it has been
locked out. After one hour of continuous thermostat
demand for heat, the watchguard will break and remake
thermostat demand to the furnace and automatically reset
the control to relight the furnace.
Heating Operation DIP Switch Settings
Switch 1 -- Thermostat Selection --
This unit may be
used with either a single-stage or two-stage thermostat.
The thermostat selection is made using a DIP switch which
must be properly positioned for the particular application.
The DIP switch is factory-positioned for use with a two-
stage thermostat. If a single-stage thermostat is to be
used, the DIP switch must be repositioned.
1. Select “OFF” for two-stage heating operation controlled
by a two-stage heating thermostat (factory setting);
2. Select “ON” for two-stage heating operation controlled
by a single-stage heating thermostat. This setting
provides a timed delay before second-stage heat is
initiated.
Switch 2 -- Second Stage Delay (Used with Single-Stage
Thermostat Only) --
This switch is used to determine the
second stage on delay when a single-stage thermostat is
being used. The switch is factory-set in the OFF position,
which provides a 7-minute delay before second-stage heat
is initiated. If the switch is toggled to the ON position, it
will provide a 12-minute delay before second-stage heat is
initiated. This switch is only activated when the thermostat
selector jumper is positioned for SINGLE-stage thermostat
use.
Indoor Blower Operation DIP Switch Settings
Switches 3 and 4 -- Heating Mode Blower-Off Delay --
The blower-on delay of 30 seconds is not adjustable. The
blower-off delay (time that the blower operates after the
heating demand has been satisfied) can be adjusted by
moving switches 3 and 4 on the integrated control. The
unit is shipped from the factory with a blower-off delay of
90 seconds.
The blower off delay affects comfort and is adjustable to
satisfy individual applications. Adjust the blower off delay to
achieve a supply air temperature between 90° and 110°F at
the exact moment that the blower is de-energized. Longer
off delay settings provide lower supply air temperatures;
shorter settings provide higher supply air temperatures.
Table 10 provides the blower off timings that will result from
different switch settings.
Blower Off Delay
Seconds
Switch 3
Switch 4
60
On
Off
90 (factory)
Off
Off
120
Off
On
180
On
On
Table 10.
Blower Off Heating Mode Delay Switch
Settings
Switch 5 -- Cooling Mode Blower-Off Delay--
The unit
is shipped from the factory with the dip switch positioned
OFF for a 45 second delay. Table 11 provides the cooling
mode off delay settings.
Blower Off Delay Seconds
Switch 5
45 (factory)
Off
2
On
Table 11.
Blower Off Cooling Mode Delay Switch
Settings
Switches 6 and 7 -- Continuous Fan Mode --
Low Heat
Speed is the only available setting for Continuous Fan
Continuous Fan
Mode
Switch 6
Switch 7
Low Heat Speed
(factory)
Off
Off
Table 12. Continuous Fan Mode Settings
Switch 8 -
DIP Switch 8 is not powered and not used.
Switching from on/off will not change any output.
On-Board Links and Diagnostic Push
Button
Carefully review all configuration information provided.
Failure to properly set DIP switches, jumpers and on-
board links can result in improper operation!
WARNING
On-Board Link W914 Dehum
On-board link W914, is a clippable connection between
terminals R and DS on the integrated control. W914 must
be cut when the furnace is installed with a thermostat which
features humidity control. If the link is not cut, terminal “DS”
will remain energized not allowing the blower to reduce to
low cool speed upon a call for dehumidification.