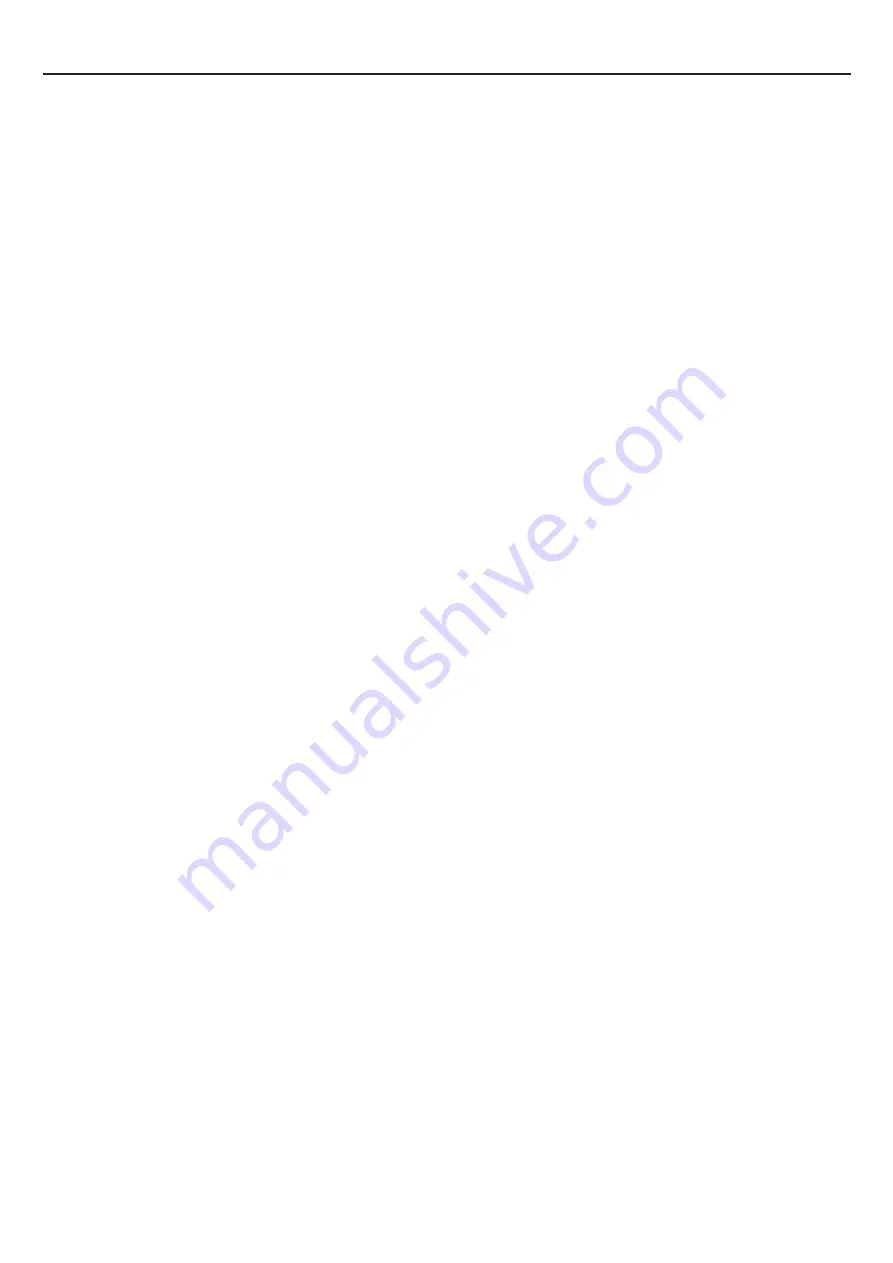
1
2
3
4
5
6
7
8
9
10
11
12
13
14
15
16
17
18
19
20
21
22
23
24
25
26
27
28
29
30
31
32
33
34
35
36
37
38
39
40
41
42
43
44
45
46
47
48
49
50
51
End Cap
Extractable Stop Rail
Scale I
Stop Rail Extrusion
Scale II
Screw M5x6
Scale III
Extension Stop Rail
Set Screw M6x12
Guide Plate
Bush 6mm
Nut
Clamp
Washer 6mm
Wing Screw
Guide Plate
Shaft
Washer 6mm
Screw
Wing Screw
Washer 6mm
Magni
Þ
er
Flip stop
Shaft
Guide Plate
Support Bracket
Carriage Bolt M8x20
Washer 8mm
Hex Nut M8
Hex Nut M16x1.5
Sliding Table Frame Assembly
Seat - Stop Block
Pin
Scale
Wing Screw
Bush
Washer 6mm
End Cap
Square Nut
Hexagon Screw M6x10
Washer 6mm
Position Pin
Screw M6x10
Bolt M6x20
Tapped Screw
End Cap
Swing Arm Assembly
Hex head screw M10X25
Washer 10mm
Seat - Swing Arm
Hex head screw M8X25
52
53
54
55
56
57
58
59
60
61
62
63
64
65
66
67
68
69
70
71
72
73
74
75
76
77
78
79
80
81
82
83
84
85
86
87
88
89
90
91
92
93
94
95
96
97
98
99
100
101
102
Hex nut M8
Washer 8mm
End Cap
Extension Arm
Roller
Screw M6X10
Washer 6mm
Shaft
Bearing
Shaft
Hex head screw M6X30
Pin
Plate
Grub Screw
Hex Set screw M6X16
Washer 6mm
Washer 8mm
Thumb Screw
Support Plate
End Cap
Tapped Screw
Square Nut M8
Screw M8X16
Seat - Sliding Carriage
Countersunk Head Screw M6x16
Limiting Stoper
Limiting Screw
End Cap
Limiting Stoper
Screw M6x25
Sliding Carriage
Sliding Ball
Felt
Frame
Handle
Hex Nut
Position Handle
Knob
Washer
Clamp Plate
Square Nut
Stop Block
Nut M6
Adjustable Seat
Limiting Screw
Nut
Wing Screw
Washer
Thrust Bearing
Washer
Nut
No. Part Description
No. Part Description
24
Summary of Contents for TS250SC
Page 1: ...20 7 08 W460 HAFCO ST1265 SAWBENCH PARTS MANUAL ...
Page 17: ...14 12 Wiring Diagrams Wiring Diagram 230V Wiring Diagram 400V ...
Page 20: ...17 ...
Page 21: ...18 ...
Page 22: ...19 ...
Page 23: ...20 ...
Page 28: ...25 ...