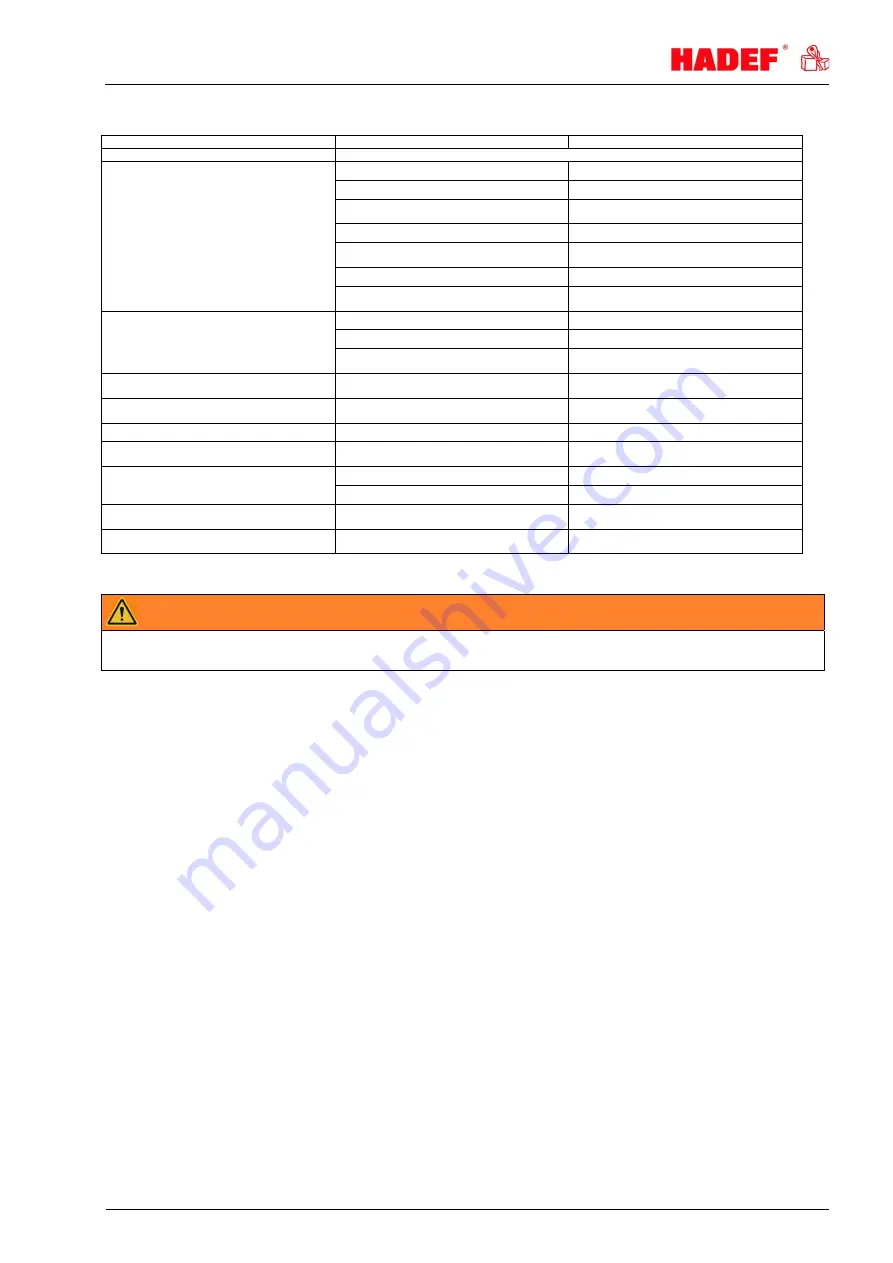
5.52.127.01.01.02
23
15 Remedy
Problem Cause Remedy
Load is not lifted
Overload
reduce the load to nominal load
load got stuck
set the load free again
brake linings are worn
Do maintenance and
exchange the brake linings
Load chain is twisted
Align the load chain
Defect of chain, gear or chain wheels
Do maintenance and replace defective parts by original
spare parts
Pawl does not engage properly
Check the pawl and replace it if necessary
Pawl spring is missing
Do maintenance and replace defective parts by original
spare parts
It is difficult to lift the load
Overload
reduce the load to nominal load
Dirty chains, gear or chain wheels
Do maintenance, lubricate chains, gear and chain wheels
Defect of chain, gear or chain wheels
Do maintenance and replace defective parts by original
spare parts
Load is lifted with interruptions
Pawl spring is missing or defective
Do maintenance and replace defective parts by original
spare parts
Hoist does not lift without load
Brake spring is missing
Do maintenance and replace defective parts by original
spare parts
Hoist does not lift the whole distance long
Hook stucks, chain is twisted
Place hooks and chains in correct position
Brake remains closed
(stuck)
The load hook was pulled against the housing and got
stuck there.
Release the hook, suspend the load again, lower the load,
unload the hoist.
Hoist does not lower the load
Brake too tight
Lift the brake.
Brake too tight due to rust
Replace rusty parts and effect periodic inspection
Load slips down partially during lowering
Foreign-object between the brake discs
Remove the foreign-object, clean the surface
Should the surface show lines, replace the brake disc
Load slips down during lowering
Brake discs are missing, are installed incorrectly or are
worn
Replace the brake discs resp. install them correctly
16 Decommissioning
WARNING!
It is essential that the following points are observed in order to prevent damage to the equipment or critical
injury when the device is being decommissioned:
It is mandatory that all steps for decommissioning the machine are carried out in the indicated sequence:
First secure the working area for decommissioning, leaving plenty of space.
Read the chapter "Safety instructions".
Disassembly is carried out in reverse order to the assembly.
Please make sure that all operating material is disposed of in accordance with environmental regulations.
16.1 Temporary
decommissioning
Measures are as above.
Also read the chapter “Transport and storage”.
16.2 Final
decommissioning/disposal
Measures are as above.
After disassembly, ensure that the disposal of the equipment and any materials it contains is carried out
in accordance with environmental regulations.