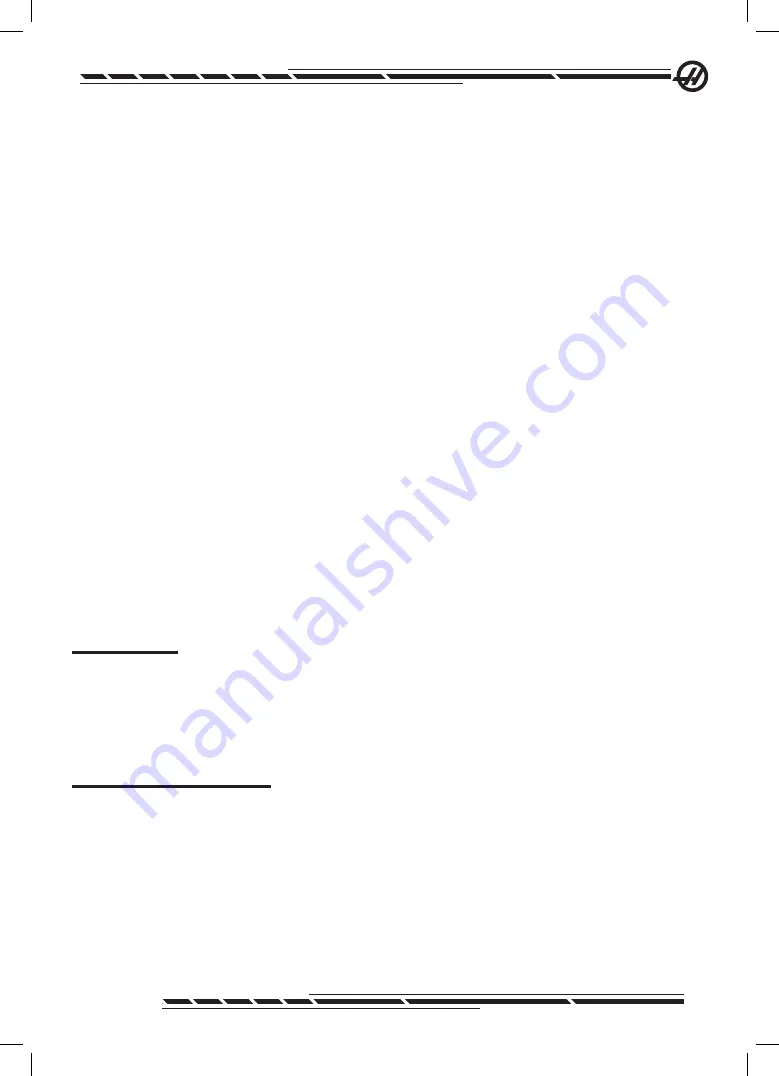
5
96-0198 Rev V
March 2012
Spindle Operating Guidelines
• Check the pullstud torque before the pullstud is loaded into the spindle.
• Roughing operations should use 3/8" diameter or smaller tools.
• Roughing operations should be at 10,000 rpm or higher.
• Roughing depth of cut should be 20% or less of tool diameter.
• Roughing width of cut should be 25% or less of tool diameter.
• Finishing operations require appropriate “G” code. The program must provide
enough data points and arcs for the desired path, using ultra-ine (0.00005" or
smaller) tolerance limits in the CAD/CAM process.
• All tools should be as short as possible.
• All tools must be balanced to G2.5 at 30,000 rpm.
CAUTION
Heavy tool weights should be distributed evenly in the tool
changer. This means heavy tools should be located across
from one another, not next to each other. Ensure adequate
clearance between tools in the tool changer.
Spindle General Precautions and Safety
• The 30K option is for high rpm/low torque applications.
• Do not operate the spindle at any time without a tool holder in the spindle taper.
• Use only speciied ISO20 tooling without drive slots.
• Use only tooling that has been balanced as an assembly (G1.0 or better, per ANSI
S2.19/ISO 1940). Tooling should be re-balanced every time the tool is changed or
moved in the tool holder.
• The Maximum collet size is 3/8".
• Tool lengths should be under 10 times the diameter from the gauge line with tool
-
ing above 1/4" diameter.
• Maximum tap size is 1/4-20 x 1/4" depth in aluminum, 10-32 x 1/4" depth in steel.
• Run the Daily Warm-Up program before running the spindle.
• Use only ER16 collet type toolholders.
Spindle Run-in
You must run the spindle run-in program before any machining use (especially when the
machine is irst installed or transported). The spindle can overheat and fail if it is not run-in.
Make sure a balanced ISO20 toolholder is in the spindle, then run program #O02025
(SPINDLE RUN-IN). The program will take approximately six hours to complete.
Spindle Warm-Up Programs
Program #O02024 20 MIN SPINDLE WARM-UP is supplied with the machine. It slowly in
-
creases spindle speed over 20 minutes to distribute spindle lubricant and thermally stabilize
the spindle. You must run this program prior to machine use if the machine has been off or
idle for more than two hours. The machine control shows a reminder each day to warm up
the spindle.