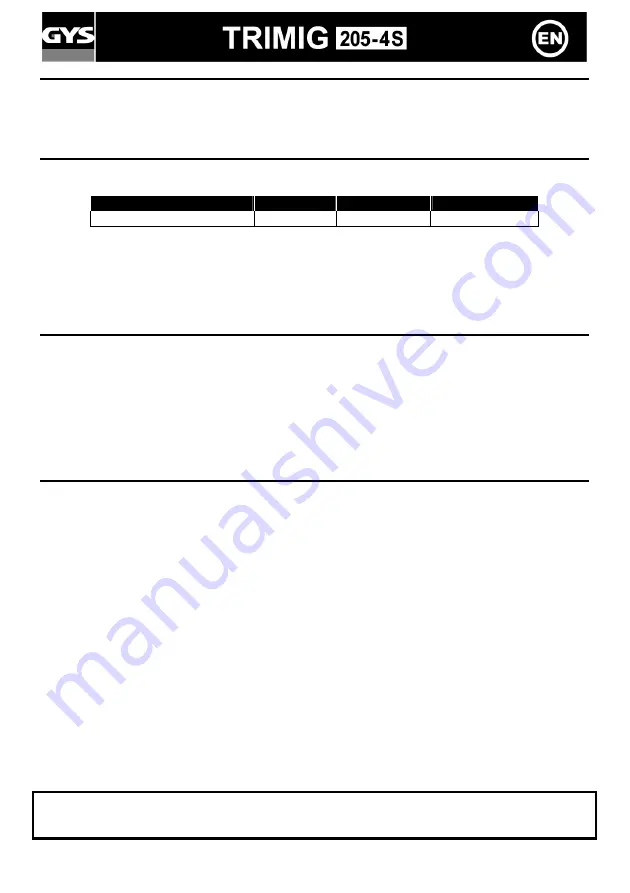
14
ADVICE & THERMAL PROTECTION
•
Respect the basic rules of welding.
•
Leave the air holes of the device open to allow air circulation.
•
Leave the device plugged in after welding to allow cooling.
•
Thermal protection: The light turns on requiring a cooling duration, typically a couple of minutes according to
the ambient temperature.
DUTY CYCLE & WELDING ENVIRONMENT
•
The welding unit describes an output characteristic of "constant current" type. The duty cycles following the
norm EN60974-1 (at 40°C on a 10mn cycle) as indicated in the table here below:
X / 60974-1 @ 40°C (T cycle = 10 min)
I max
60% (T cycle = 10 min)
100% (T cycle = 10 min)
Trimig 205-4 S
22% @ 150 A
120 A
95 A
Note: The warming test was done at room temperature and the duty cycle at 40°C was determined by simulation.
•
These are A-class devices. They are designed to be used in an industrial or professional environment. In a different
environment, it can be difficult to ensure electromagnetic compatibility, due to conducted disturbances as well as radiation.
•
This device complies with IEC 6100-3-12, provided that the power of the short-circuit Ssc is equal to or greater than
1.8MVA at the interface between the machine and the mains power network. It is the responsibility of the installer or user
of the equipment to ensure - if necessary by consulting the operator of the mains electricity, that the equipment is only
connected to a power supply where the power of short-circuit ssc is equal to or greater than 1.8MVA.
MAINTENANCE
•
The maintenance has to be done by a qualified person.
•
Cut the power supply unplugging the device, wait for the ventilator to stop before working on the welding unit. Inside,
tensions and currents are high and dangerous.
•
Regularly remove the metal cover and dust with compressed air. Take the opportunity to have the electrical
connections checked by a qualified person with an insulated tool.
•
Regularly check the good condition of the power supply cord. If damaged, it has to be changed by the manufacturers
after sales service or a qualified person, to avoid any danger.
SECURITY
MIG/MAG welding can be dangerous and cause serious or even lethal wounds. Protect yourself and
protect the others.
Respect the following safety instructions :
Arc radiations
Protect yourself with a helmet fitted with filters in compliance with EN169 or EN 379.
Rain, steam, dampness
Use your welding unit in a clean environment (pollution factor ≤ 3), laid down flat and more
than one meter far from the part to be welded. Do not use in rain or snow.
Electric shock
This device must only be used with a three-phase power supply with 3 wires and a neutral
connected to earth. Do not touch the parts under tension. Check that the supply net is well
adapted to the unit.
Falls
Do not move the unit over people or objects.
Burns
Wear fire-proof working clothes (cotton, overalls or jeans).
Work with protection gloves and a fire-proof apron.
Protect the others installing fire-proof protection walls or telling them not to look at the arc and
to keep sufficient distances.
Fire risks
Remove all flammable products from the working area. Do not work in presence of flammable
gases.
Fumes
Do not inhale welding gases and fumes. Use the device in a correctly ventilated environment,
with artificial extraction if welding indoor.
Additional
Any welding operation:
Precautions
- in rooms where there are increased electric shock risks,
- in closed rooms,
- in presence of flammable or explosive material,
must always be approved by a "responsible expert", and made in presence of people trained to
intervene in case of urgency.
Technical protection means described in the Technical Specification CEI/IEC 62081 must be
implemented.
Welding in raised positions is forbidden, except where safety platforms are used.
People wearing Pacemakers must see their doctor before using these devices.
Do not use the welding unit to unfreeze pipes.
Handle the gas bottle with care, there might be risks if the bottle or its valve get damaged.
Summary of Contents for TRIMIG 205-4S
Page 3: ...3 FIG 4 FIG 5 1 4 2 3 5...
Page 30: ...30 SYNERGIC SPOOL GUN 041486 100 CO2 Ar CO2 1 2 4 5 3 1 2 4 5 3...
Page 33: ...33 15 20 MIG MAG Spool Gun Spool Gun spool gun...
Page 45: ...45 EN 169 EN 379 3 CEI IEC 62081...
Page 46: ...46 3 15 20...
Page 50: ...50 SCH MA LECTRIQUE CIRCUIT DIAGRAM SCHALTPLAN...