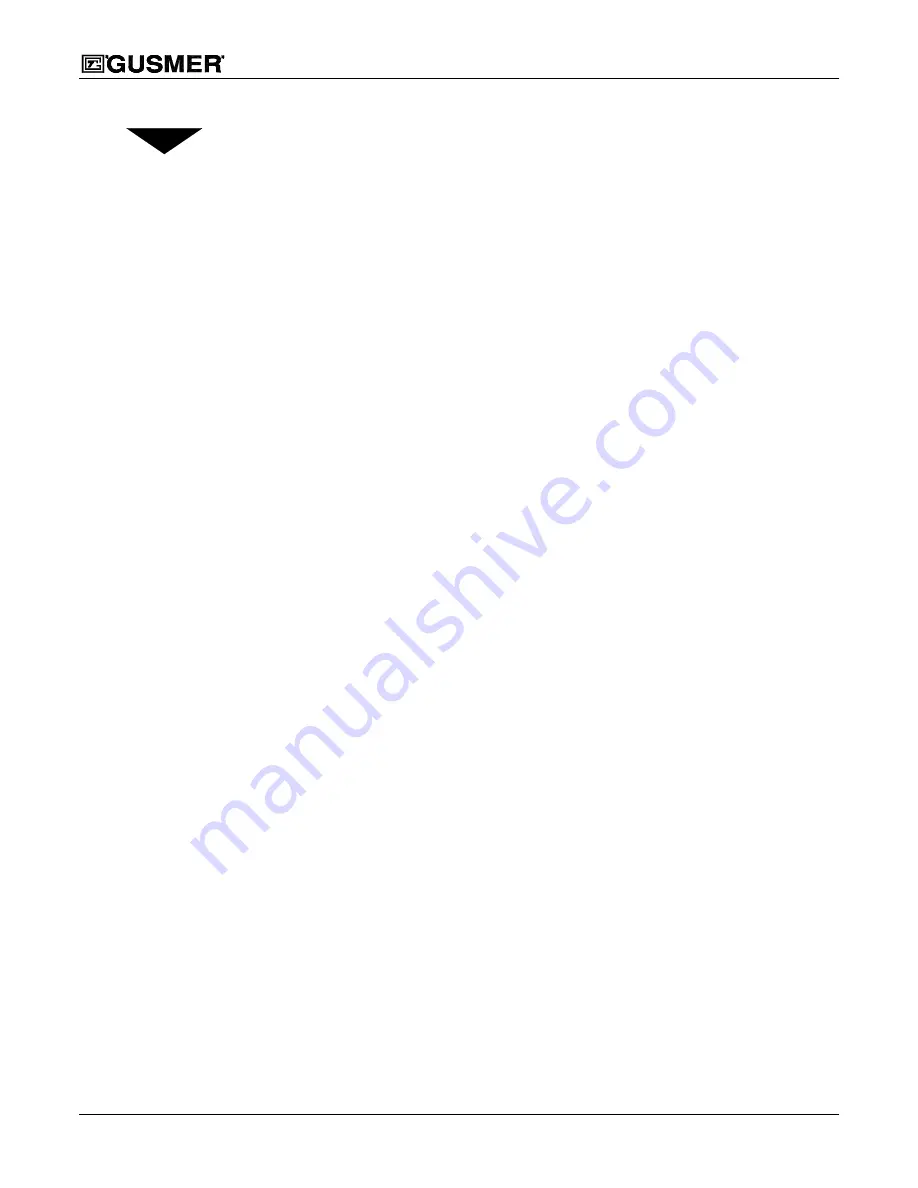
GAP Pro Spray Gun
6
36943-1, Issue 1
GENERAL SAFETY INFORMATION
It is necessary to understand and follow the instructions in this manual to ensure proper
and safe operation of the equipment.
As with most mechanical equipment, certain safety precautions must be taken when the
equipment discussed in this manual is operated or serviced. Severe bodily injury or
damage to equipment and property may result if the instructions and precautions listed
throughout this manual are not followed.
Needless to say, sufficient guidelines cannot be developed to eliminate the need for good
common sense in the use and servicing of this equipment, and in the use and application
of the products, this equipment has been designed to process. Users of this equipment
must therefore, make their own determination as to the suitability of the information
contained in this manual to their specific operation and requirements. There should be
no assumption made that the safety measures and instructions contained herein are all-
inclusive, and that other safety measures may not be required for specific use or
application.
The following safety guidelines are generally applicable to the safe and efficient use of
the equipment.
Acceptable Equipment Uses
The equipment is designed for the dispensing of polyurethane foams, two-component
coating systems such as polyureas, and some two-component epoxy systems. Under no
circumstances should any acid or corrosive chemicals be used in the unit. Consult
GUSMER if there is any doubt about the compatibility of the chemical system to be used
in this equipment.
Any use of this equipment other than as indicated above constitutes misuse unless
express written approval is obtained from GUSMER.
Your Gusmer equipment incorporates design parameters, features, and functionality
developed in over 40 years of plural component equipment design and manufacture. It is
manufactured under the stringent standards of ISO 9001, and is backed by the Gusmer
Warranty included herein.
The use of genuine Gusmer replacement parts is recommended for your equipment.
Substitution of parts not designed, manufactured, or recommended by Gusmer may result
in reduced performance of, and/or damage to, your Gusmer equipment. Any alterations
to, or substitutions for, genuine Gusmer parts shall void the provisions of the Gusmer
Warranty.