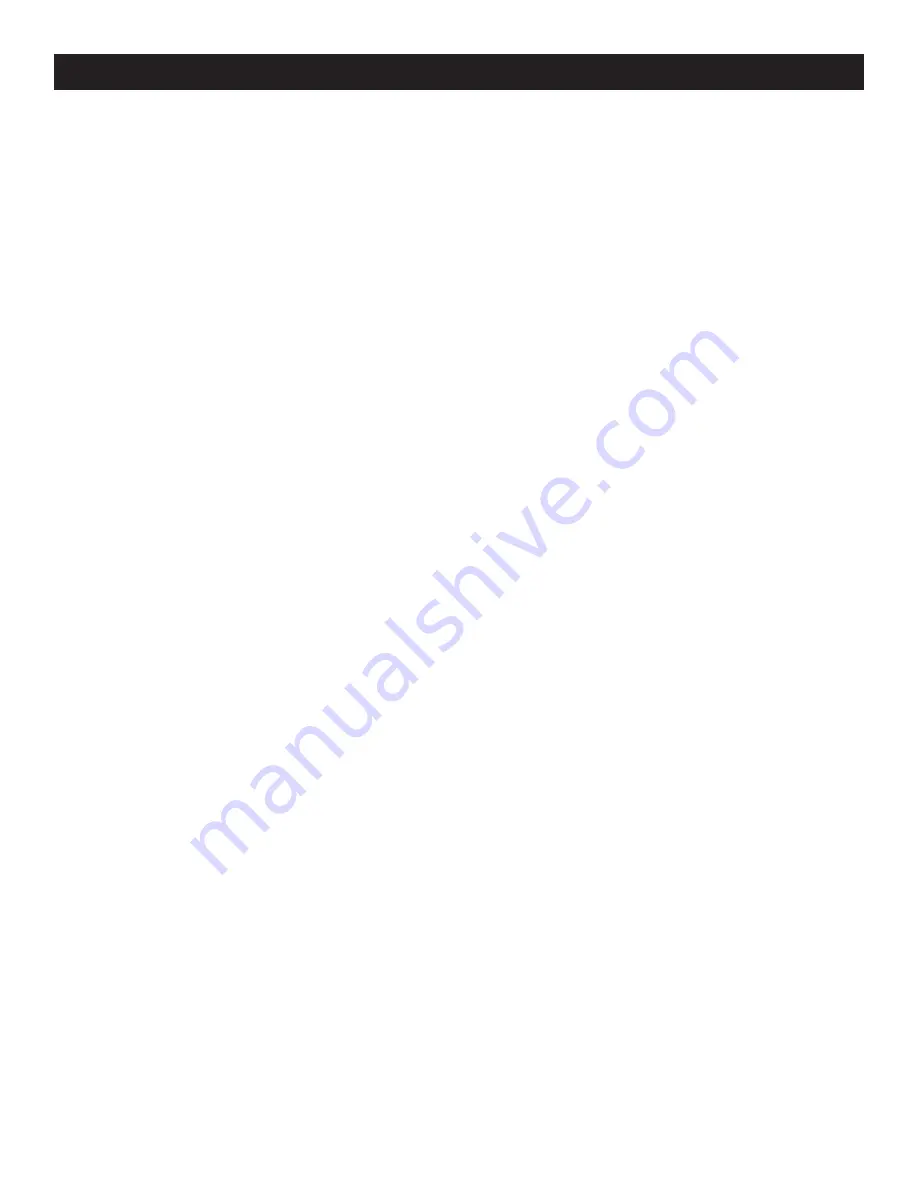
Making Water and Electrical Connections at the Stove
•
After the stove has been placed on the concrete or pads, remove the panel at the back of the stove.
•
The return (cold water) pipe must be connected to the fitting at the upper position and the supply (hot water) at the fitting
toward the bottom of the stove. If multi-pole locations are to be heated, tees must be added on both the supply (hot) and
return (cold). It is necessary to use brass fittings between the stainless and other metals.
•
The stove has been pre-wired at the factory; therefore, it is only necessary to connect the common from the wire from the
trench to the common from the stove, neutral to neutral, ground to ground. Ensure that the connections are water tight.
•
Return the panel to the back of the stove.
Piping Inside the Building
It is recommended that piping used is able to withstand 100 PSI at 180°
F, and is at least 1” (inch) in diameter.
1 1/4“
(Inch) piping is
recommended for larger systems.
•
For each building, a circulation pump is needed. The pump can be located on the supply side (hot water).
•
Before each pump, a filtering device must be installed. This filter will minimize the contaminants in the water and maximize
the life of the circulation pump.
•
If the central heating system in the building is a forced air furnace, it is important to select the appropriate water to air
exchanger. Contact your heating contractor for proper size. The coil is to be installed in the furnace plenum. If there is an air
conditioning evaporator coil in the plenum, install the water to air coil after the a/c coil.
•
If the central heating system is a hot water boiler system, a water to water heat exchanger is needed. The water from an
open system will contaminate the closed system if the waters are mixed together.
•
It is advisable to install ball valves, isolation flanges, etc. to make the removal and the replacement components easier.
Wiring Inside the Building
•
The electrical wiring must be done by an experienced HVAC technician to ensure the system will operate as desired and is
safe.
•
It is recommended that the circulation pump or pumps run continuously.
•
The existing forced air circulation blower needs to be wired through the circuit board to a 24-volt wall thermostat which is
dedicated for this purpose. The other wall thermostat which is for the forced air (Oil, LP, NG or Electric) is left intact. The new
24-volt wall thermostat will cause the circulation blower to run without the burners coming on. An experienced HVAC
technician needs to perform the wiring.
•
The electrical for a boiler system is more complicated because the existing boiler wall thermostat is used but the burners on
the (Oil, LP, NG or Electric) boiler are not to operate when the water from the water stove is to provide heat. It is necessary to
have an experienced HVAC technician wire this configuration.
•
If air conditioning is used you must add a relay DPDT to prevent the condenser from turning on when the fan is energized.
Electrical Requirements
•
Electrical Rating: 120 AV Volts, 6 AMPS, 60 Hz. Wire must be rated and approved for direct burial if it is to be buried in the
same trench as the water lines. Boiler power connection box is located at rear of boiler inside back cover. Minimum supply 15
AMPS. Maximum device 15 AMPS.
USE COPPER CONDUCTORS ONLY.
INSTALLATION
15
Summary of Contents for Crown Royal Stoves Multi-Pass 7200MP
Page 2: ......
Page 4: ......
Page 6: ...6 ...
Page 8: ...8 ...
Page 11: ...FURNACE FLOOR PLAN Model 7200MP Model 7300MP 11 ...
Page 12: ...FURNACE FLOOR PLAN Model 7400MP Model 7500MP 12 ...
Page 22: ...22 ...
Page 30: ...30 ...
Page 31: ...ELECTRICAL WIRING DIAGRAM 7200MP 7300MP 7400MP 31 ...
Page 32: ...ELECTRICAL WIRING DIAGRAM 7500MP 32 ...
Page 38: ...38 ...
Page 42: ...Model 7500MP 42 ...
Page 51: ...51 ...
Page 52: ...OWNER S MANUAL ...