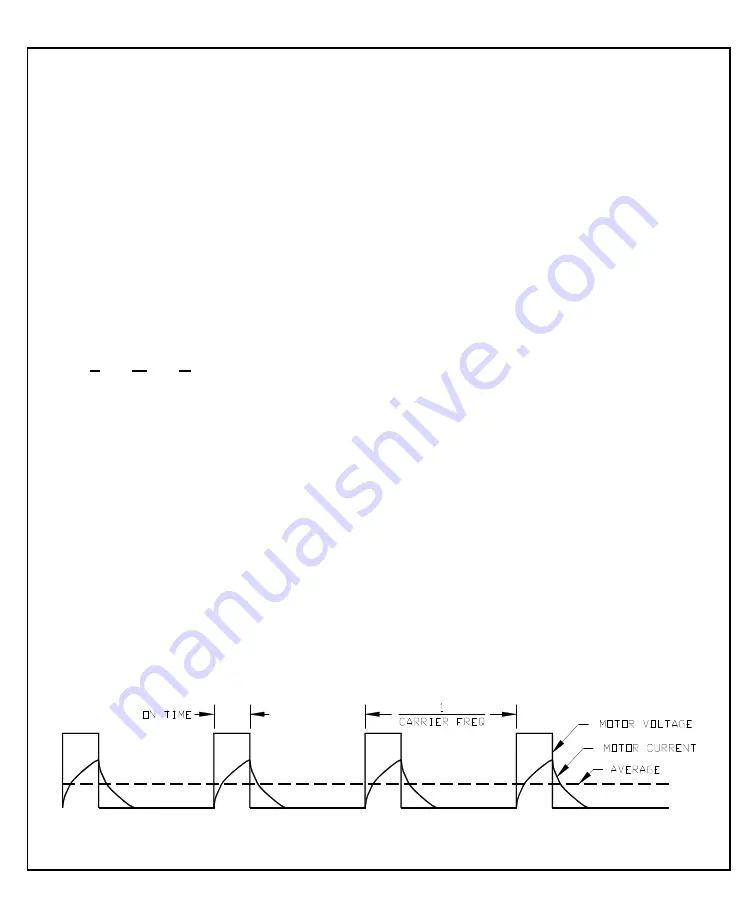
9
GLENTEK Inc. 208 Standard Street, El Segundo, California 90245, U.S.A. (310) 322-3026
SMA7215 MANUAL
Chapter Two: Theory of Operation
2.1 Introduction:
This chapter contains the basic control theory of how brush type and brushless servo
motors and amplifiers operate. It also compares and contrasts the advantages and
disadvantages of brushless and brush type motors and amplifiers to help you select which is
best suited for your application. The following is a summary of the topics:
•
The theory behind an amplifier driving DC servo motors.
•
A comparison between brush type and brushless motors.
•
Operation of output switching transistors.
•
“
H Type
”
output bridge configuration.
•
Pulse-Width-Modulation (PWM).
•
Current-Loop and Velocity-Loop operation..
•
Protection circuits.
2.2 Driving DC Servo-Motors:
The torque of any DC motor is proportional to motor current: the stronger the magnetic
field, the stronger the pull. Motor current may be controlled in two ways: linear and PWM
(P
ulse-W
idth M
odulation). Linear control is achieved by simply inserting a resistance in
series with the motor. This resistance is usually a partially turned on transistor. The
transistor is said to be in its "linear" region. Linear amplifiers are simple, accurate, and
effective. However, they are very inefficient and they generate a lot of heat. Linear amplifiers
are used when low electrical noise, high bandwidths (2KHz or higher) and or low inductance
(less than 1mH) motors are used. In pulse-width modulation the control devices (output
transistors) are rapidly turned full on and full off. The ratio of the on time (the pulse width) and
off time determines the average motor current. Refer to figure 2.1. For example: if the output
is on 25% of the time and off 75% of the time, the average motor current is approximately
25% of maximum.
A coil of wire, such as the windings of a motor, forms an inductor. Inductors resist
changes in current. This resistance to change, known as reactance, acts to dampen or
average the high-current spikes that would otherwise occur when the output devices are on.
In fact, if motor inductance is low, external inductors may have to be added in series with
each motor lead to ensure proper operation.
A brush type motor may be run from a steady DC voltage since the brushes and
commutator switch the current from winding to winding. However, a brushless motor requires
that the voltage be switched from winding to winding externally; the voltage that drives a
brushless motor is a constantly changing AC waveform. Section 2.5 discusses these
waveforms.
Figure 2.1
Pulse Width Modulation Waveform