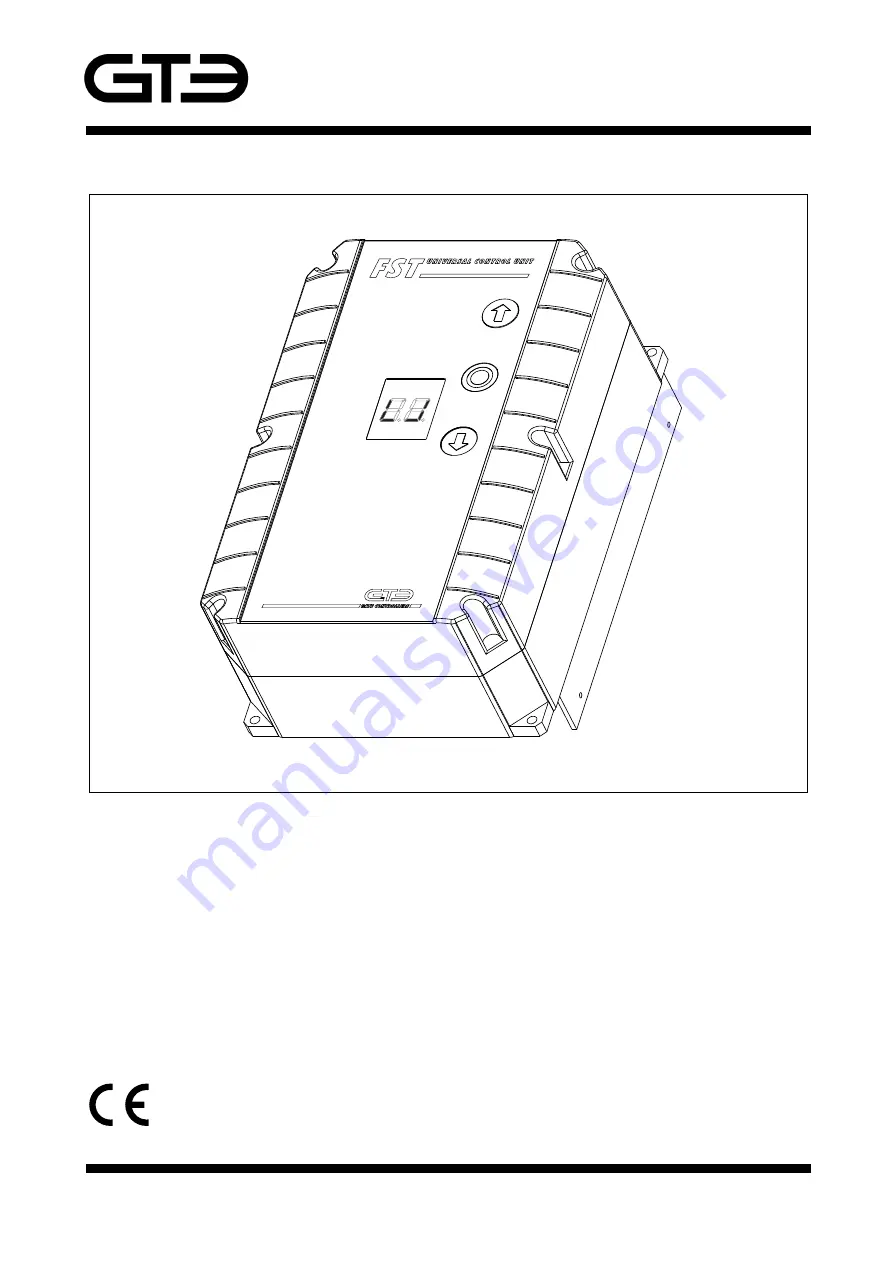
GTE Industrieelektronik GmbH
Tel. +49 2162 3703-0
Helmholtzstr.21, 38-40
Fax +49 2162 3703-25
41747 Viersen
E-mail: [email protected]
GERMANY
Internet: www.gte.de
FST-75
FST-150
This document is subject to change without notification!
260-2210-002 EN064
FST 75 / 150
Operating Instructions
- Translation -
Frequency Converter Control Unit for
sectional doors, roller doors, high-speed doors, roller-grilles,
sliding gates, hinged gates, folding doors and barriers