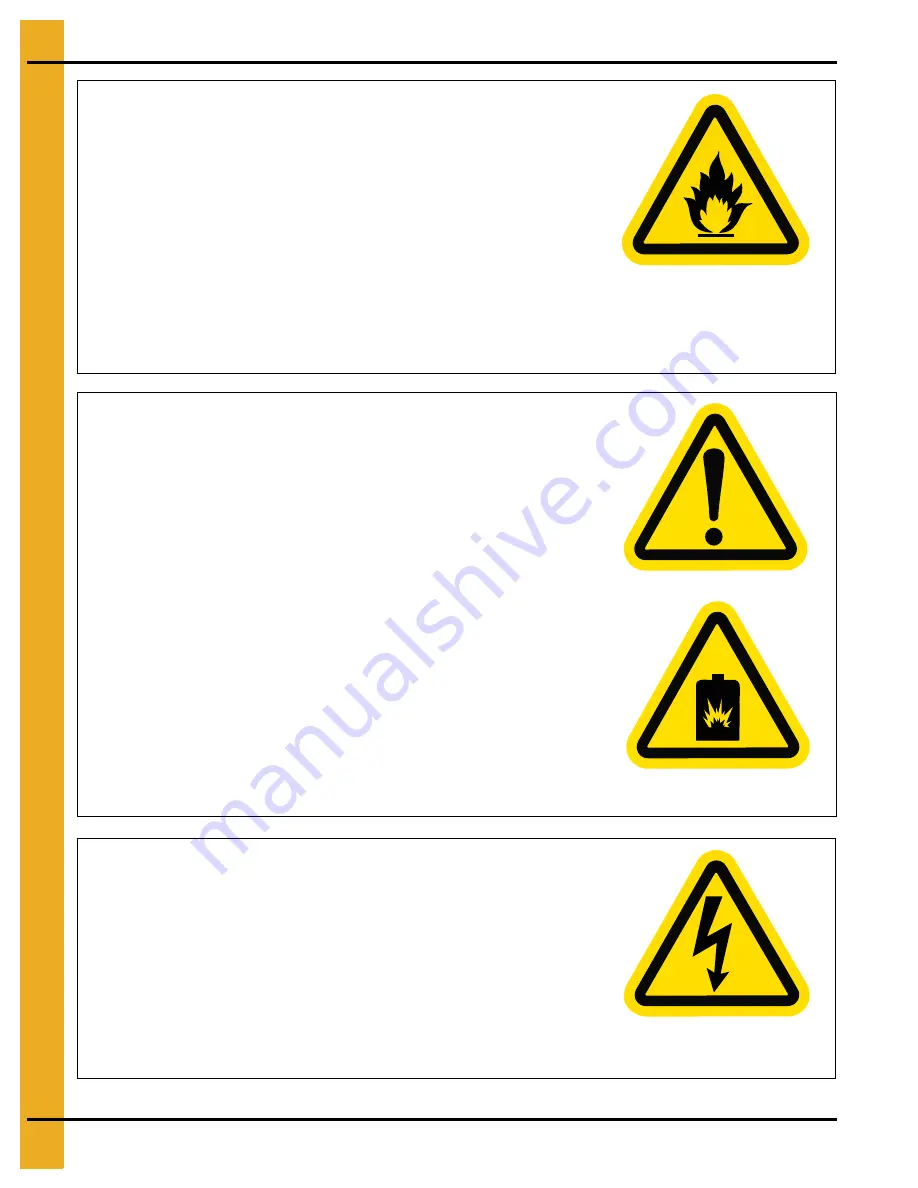
1. Safety
8
PNEG-1707
TM-Series Tower Dryer
Install and Operate Gas-Fired Equipment Properly
•
Gas-fired equipment should be installed by a qualified pipe
fitter and must conform with local codes.
• For Canada: The equipment shall be installed in accordance
with the
Natural Gas and Propane Installation Code, CSA
B149.1, or the Propane Storage and Handling Code, CSA
B149.2,
or applicable provincial regulations, which should be
carefully followed in all cases. Authorities having jurisdiction
should be consulted before installations are made.
• For the United States: The equipment shall be installed in
accordance with the
National Fuel Gas Code ANSI
Z223.1/NFPA 54.
ST-0016-2
For Your Safety
•
If you smell gas:
- Do not try to light any appliance.
- Extinguish any open flames.
- Do not touch any electrical switch.
- Immediately call your gas supplier. Follow the gas supplier’s
instructions.
- If you cannot reach your gas supplier, call the fire department.
•
The use and storage of gasoline and other flammable vapors and
liquids in open containers in the vicinity of this appliance is
hazardous.
•
Improper installation, adjustment, alteration, service or maintenance
can cause property damage, injury or death. Read the installation,
operating and maintenance instructions thoroughly before installing
or servicing this equipment. Installation and service must be
performed by a qualified installer, service agency or the gas
supplier.
ST-0024-1
Install and Operate Electrical Equipment Properly
•
Electrical controls must be installed by a qualified electrician
and must meet the standards set by the National Electric Code,
Canadian Electrical Code, and all local and state codes.
• Lock-out power source before making adjustments, cleaning, or
maintaining equipment.
ST-0027-2