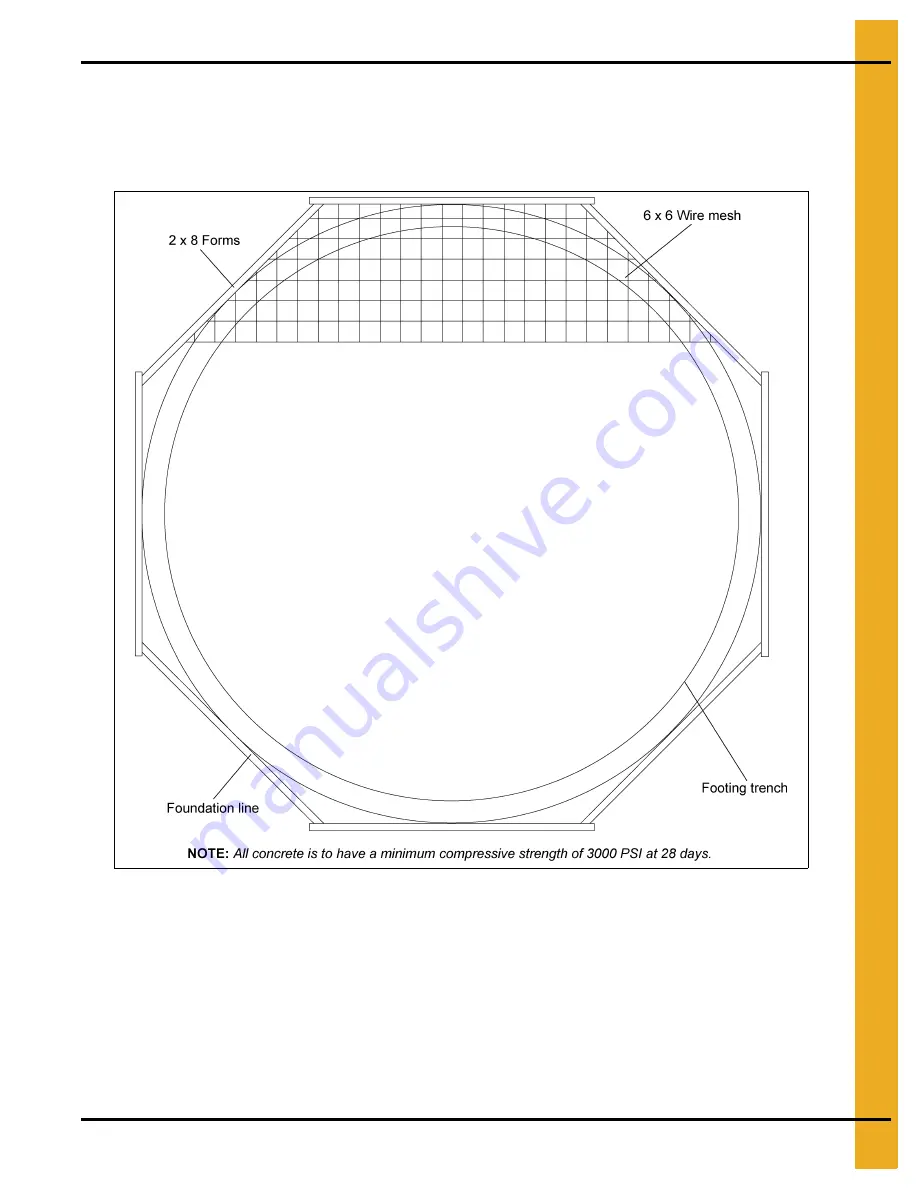
3. Foundation Requirements
PNEG-1276
Top Dry Autoflow Construction Manual 24', 30' and 36'
11
Foundation Requirements for Top Dry Bins (4.00" Top Dry
Bin Corrugation) (Continued)
Second Style of Foundation
Figure 3C
Place the Reinforcement
Once the forms and trench have been prepared, begin the placement of reinforcement rods at various
levels in the foundation’s footing. See the appropriate charts and drawings for the bin to determine
requirements and positions of the reinforcement. The reinforcement rods offer their greatest strength
when lapped properly and connected by wiring or welding. Next, place a minimum of 2" of compacted sand
on the inside section of the foundation to provide a good base for the concrete and protect against rodents.
The sand should then be covered with four (4) mil polyethylene plastic which will act as a moisture barrier.
Two (2) layers of 6 x 6 wire mesh should then be added to the entire area of the foundation to complete
the preparation of the bins foundation.