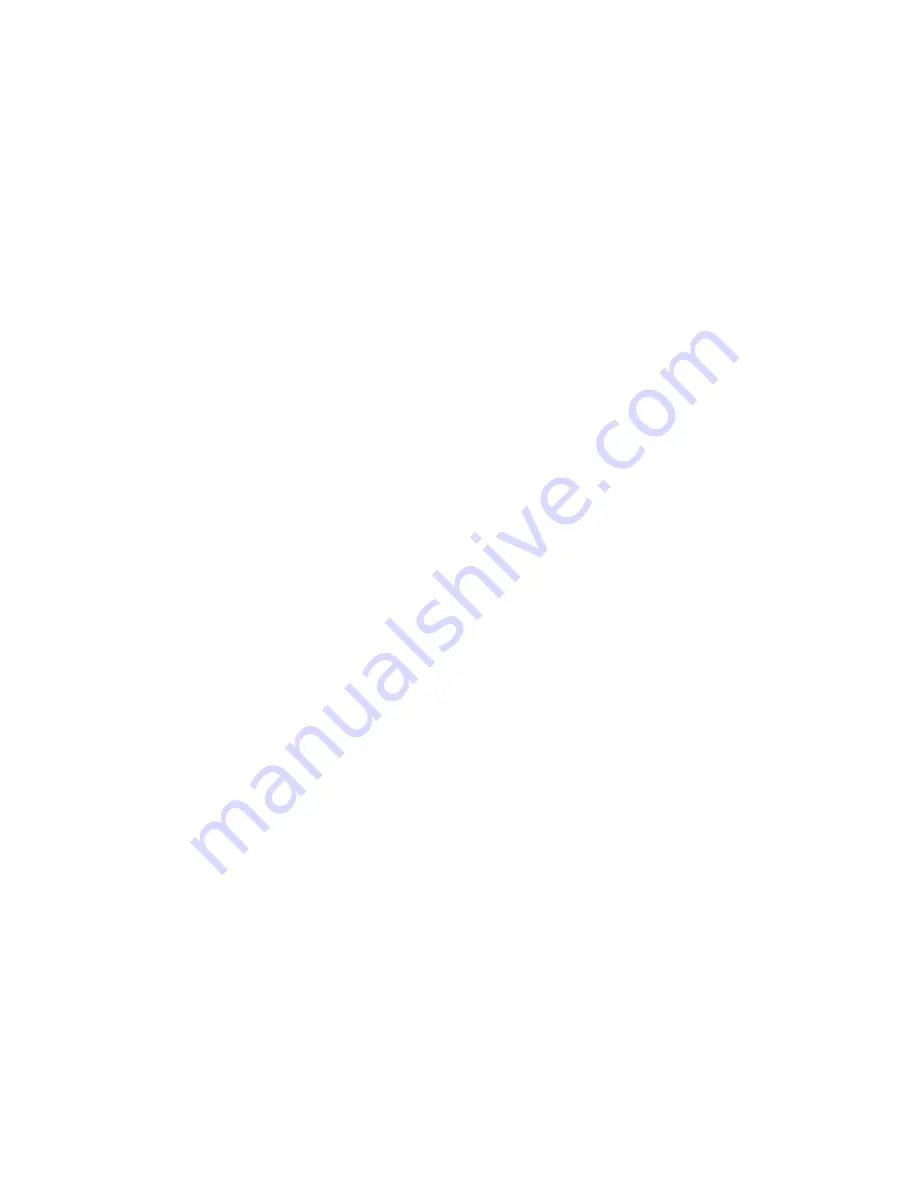
200
PC Software
The PC software can create, download and store in-
strument configurations & profiles. If the recorder fea-
ture is fitted, its recordings can be downloaded and
analysed via the software. In addition, changes can
be made to the instrument operation by adding extra
screens, amending the contact details, alarm status
labels or to the functions and labels of the LED’s. The
software can download a new language file, change
the start-up “splash screen” or configure the “Super-
visor Mode” screens. An on-screen simulation of the
instrument can be setup and tested on a configurable
load simulator.
Refer to the PC software and use sections of this man-
ual for full details.
Also refer to: LEDs and Supervisor Mode.
PD Control
Proportional and Derivative (PD) control combines pro-
portional control with derivative action. It is similar to
PID control, but without Integral action.
Also refer to: Derivative; Integral; PID Control; Propor-
tional Control and Tuning.
PI Control
Proportional and Integral Control (PI) combines propor-
tional control with integral action. It is similar to PID
Control, but without derivative action. It is often used
for modulating valves, dampers or motor speed con-
trol, where derivative action can sometimes cause in-
stability or wear of mechanical components like valves,
due to excessive movement.
Also refer to: Derivative; Integral; Modulating Valve; PID
Control; Proportional Control; Tuning and Valve Motor
Control.
PID Control
Proportional Integral and Derivative control maintains
accurate and stable levels in a process (e.g. when con-
trolling temperature or humidity etc). Proportional con-
trol avoids the oscillation characteristic of on-off con-
trol by continuously adjusting the correcting variable
output(s) to keep the process variable stable. Integral
action eliminates control deviation errors, and Deriva-
tive action counters rapid process movements.
Also refer to: Control Action; Control Deviation; Control
Enable; Control Type; Controller; Correcting Variable;
Derivative Action; Gain Scheduling; Integral Action;
Manual Mode; On-Off Control; PD Control; PI Control;
PID Sets; Primary Proportional Band; Process Variable;
Secondary Proportional Band; Setpoint and Tuning.
PID Gain Sets
The instrument contains PID 5 sets for each control
loop, allowing the instrument to be pre-set for differing
conditions. Each set has individual values for the pro-
portional bands; overlap/deadband; on-off differential
and integral & derivative times. These values are en-
tered in the control configuration sub menu or via the
automatic tuning. The PID sets might be configured for
different applications, or to allow for differing process
or load conditions that might occur in a single applica-
tion. In these cases one set at a time would be selected
as the “Active PID” set for that loop. The PID sets are
also used by the automatic gain scheduling feature.
Also refer to: Derivative Action; Gain Scheduling; Inte-
gral Action; On-Off Control; PID; Primary Proportional
Band; Secondary Proportional Band and Tuning.
PLC
This stands for Programmable Logic Controller. A mi-
croprocessor based device used in machine control. It
is particularly suited to sequential control applications,
and uses “Ladder Logic” programming techniques.
Some PLC’s are capable of basic PID control, but tend
to be expensive and often give inferior levels of control.
Also refer to: PID.
Pre-Tune
The Pre-Tune facility artificially disturbs the process
variable normal start-up pattern, so that an approxima-
tion of the PID values can be made prior to the setpoint
being reached. During pre-tune, the controller outputs
full primary power until the process value reaches the
“tuning point”. With Standard Pre-Tune this is halfway
to the setpoint, but an alternative method allows the
user to specify the process value to tune at. Pre-tune
can be selected from the automatic tuning menu and
will automatically disengage once complete.
If self-tune is enabled, it will be suspended while pre-
tune runs. A pre-tune can be configured to run at every
power up using the Auto Pre-Tune function.
Refer to the Automatic Tuning section of this manual
for full details.
Also refer to: Auto Pre-Tune; PID; Process Variable;
Self-Tune; and Tuning.
Power Output Limits
Used to limit the correcting variable. Normally the con-
trol algorithm can set these outputs to any value be-
tween 0% and 100%. If this is undesirable in a particu-
lar application, individual settings can limit the primary
power upper and lower levels and the secondary power
upper and lower levels for each control loop. The upper
limit values must be higher than the lower limits. These
parameters are not applicable if that output is set for
on-off control. Use with caution: The instrument will not
be able to control the process if the limits do not allow
the outputs to be set to the correct values needed to
maintain setpoint.
Also refer to: Correcting Variable; On-Off Control; PID
and Setpoint.
Primary Proportional Band
The portion of the input span over which the primary
output power level is proportional to the process vari-
able value. Applicable if the control type is single or
Summary of Contents for Chromalox 4081
Page 2: ...B ...