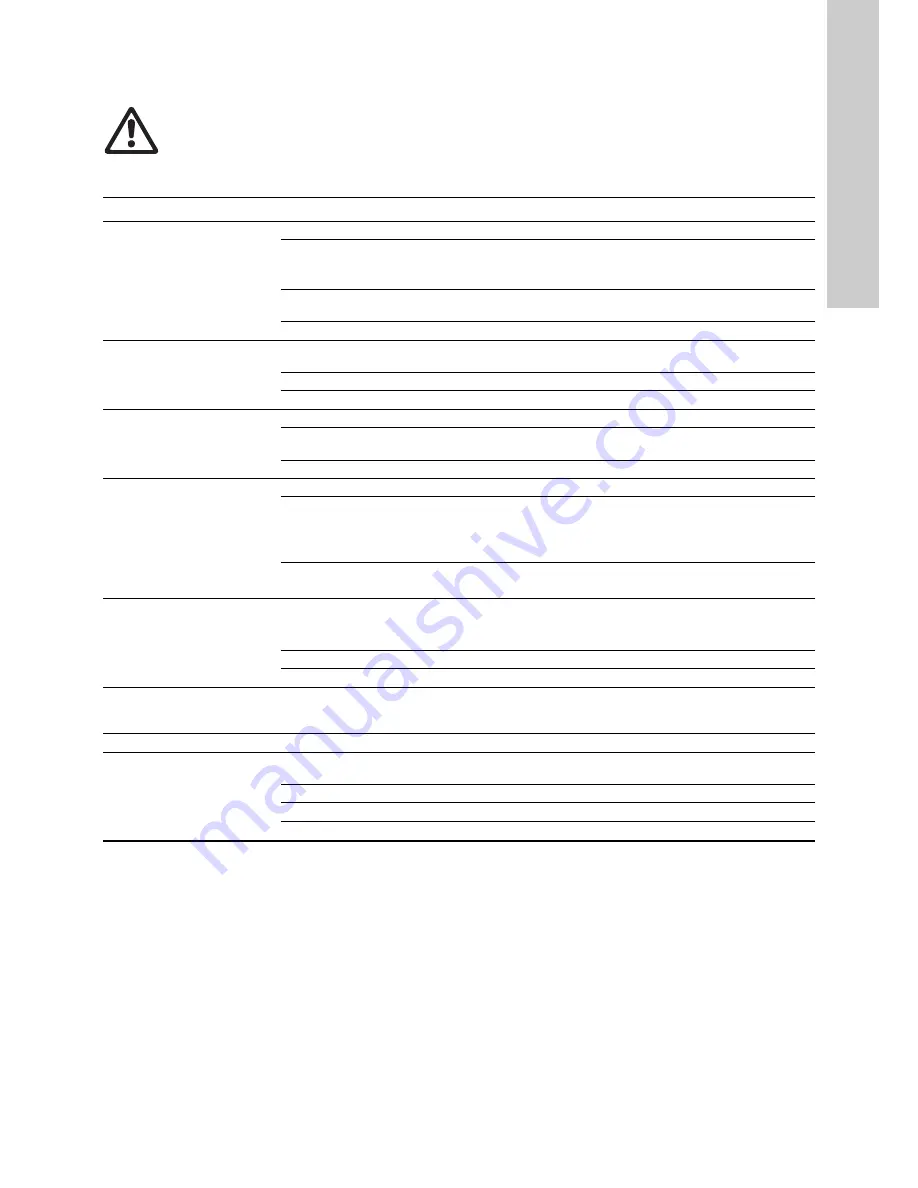
English (GB)
9
7. Fault finding
Warning
Remove the fuse, pull out the plug, or switch off the
power supply. Make sure that the power supply
cannot be accidentally switched on.
All rotating parts must have stopped moving.
The product must only be serviced by trained service
personnel.
Fault
Cause
Remedy
1. Motor does not start when
the level in the tank reaches
the start level.
a) Supply failure.
Check the power supply.
b) Fuse blown.
If new fuse blows at once, either cable
or motor is faulty.
Replace the fuse.
Measure cable and motor. If cable or motor is defective,
replace the defective parts.
c) Impeller/grinder stuck; thermal switch
tripped.
Free the impeller/grinder, and wait until the motor is
cooled down and the thermal switch has reset.
d) Pressure switch pipe blocked.
Remove the pressure switch and clean the pipe.
2. Motor hums but does not
operate.
a) Impeller/grinder stuck.
Free the impeller/grinder and check that it can rotate
freely.
b) Motor or capacitor defective.
Replace the motor or capacitor.
c) Control board defective.
Replace the control board.
3. Motor runs continuously or
at irregular intervals.
a) Water leaking from inlet into tank.
Check for leaking appliances.
b) Water leaking back into tank from
discharge pipe.
Check the non-return flap.
c) Pressure switch defective.
Replace the pressure switch unit.
4. Motor runs but does not
evacuate water.
a) Pump or tank blocked.
Remove blockage.
b) Air lock in pump or vent hole in pump
housing blocked.
Check operation of vent valve in the tank.
Check that the carbon filter is not wet.
Check that the vent hole in the pump housing is not
blocked.
c) Discharge port or pipe blocked.
Remove blockage.
Check the non-return flap.
5. The lifting station evacuates
slowly.
a) Discharge pipe is too long or has an
excessive number of bends.
Increase discharge pipe size.
Change pipework to reduce number of bends.
Change bends to swept bends.
b) The pump housing is leaky.
Replace the pump housing.
c) Hydraulics or grinder blocked.
Check and clean the hydraulics and grinder.
6. Rattling noise from the lifting
station, but water is
evacuated.
a) Foreign body hitting the
impeller/grinder.
Remove the foreign body.
7. Odour from the tank.
a) Carbon filter contaminated.
Replace the carbon filter.
8. Water from shower or
another appliance
connected to the lower inlets
drains off slowly.
Backflow from the lifting
station.
a) Non-return flap in inlet stuck, does not
open or does not close sufficiently.
Check the non-return flap.
b) Hydraulics or grinder blocked.
Check and clean the hydraulics and grinder.
c) The start level has changed.
Check and clean the hydraulics and grinder.
d) Inlet pipe diameter is too small.
Use a pipe with a larger diameter.
Summary of Contents for Sololift2
Page 1: ...Sololift2 50 Hz 1 Service instructions GRUNDFOS INSTRUCTIONS...
Page 11: ...English GB 11 9 Exploded views 9 1 WC 1 TM05 0003 0911...
Page 12: ...English GB 12 9 2 WC 3 TM05 0004 0911...
Page 13: ...English GB 13 9 3 CWC 3 TM05 0002 0911...
Page 14: ...English GB 14 9 4 C 3 TM05 0001 0911...
Page 15: ...English GB 15 9 5 D 2 TM05 0005 0911...
Page 16: ...16...